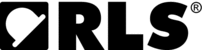
Excertos do catálogo
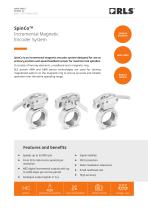
DATA SHEET SP3D01_07 Issue 7, 25th October 2023 SpinCoTM Incremental Magnetic Encoder System SPINDLE ENCODER SpinCo is an incremental magnetic encoder system designed for use as primary position and speed feedback sensor for machine tool spindles. HIGH SPEED It consists of two key elements, a readhead and a magnetic ring. RLS proven AMR and GMR sensor technologies are used for sensing magnetized pattern on the magnetic ring to ensure accurate and reliable operation over the entire operating range. ROBUST DESIGN Signal stability From 50 to 556 sin/cos periods per revolution ABZ digital incremental outputs with up to 4,096 steps per sin/cos period Wide installation tolerances Small readhead size Analogue output signals (1 Vpp) High accuracy INDUSTRIAL AUTOMATION HARSH ENVIRONMENT MOTOR CONTROL
Abrir o catálogo na página 1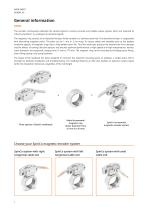
General information The encoder continuously calibrates the sensed signals to ensure accurate and reliable output signals, which are reported as industry standard 1 Vpp analogue incremental signals. The magnetic ring consists of an elastoferrite layer firmly bonded to a stainless steel hub. The elastoferrite layer is magnetised with alternating magnetic poles. The poles can be 1 mm or 2 mm long. To ensure safety and reliability even at the highest rotational speeds, all magnetic rings have a fully welded cover foil. This thin steel layer protects the elastoferrite from damage and the...
Abrir o catálogo na página 2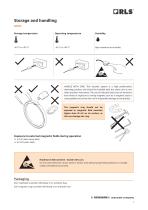
Storage and handling Storage temperature Operating temperature ߌ High resistance to humidity HANDLE WITH CARE. This encoder system is a high performance metrology product and should be handled with the same care as any other precision instrument. The use of industrial tools such as hammers and chisels or exposure to strong magnets such as a magnetic base is unacceptable and carries the risk of irreparable damage to the product. The magnetic ring should not be exposed to magnetic field densities higher than 25 mT on its surface, as this can damage the ring. Exposure to external magnetic...
Abrir o catálogo na página 3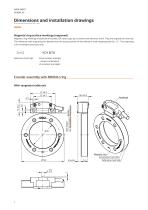
Dimensions and installation drawings Dimensions and tolerances are in mm. Magnetic ring surface markings (engraved) Magnetic ring markings include serial number, QR code, logo, part number and reference mark. They are engraved on the hub. The reference mark engraving can deviate from the actual position of the reference mark magnetization for ±5 °. The engraving is for orientation purposes only. YD1B70 Reference mark sign Serial number example - unique combination of six letters and digits Encoder assembly with MR063U ring With tangential cable exit 37 ±0.2 16.5 ±0.2 Ride height Magnetic...
Abrir o catálogo na página 4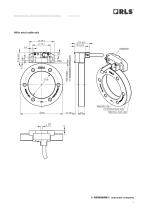
Dimensions and installation drawings With axial cable exit 37 ±0.2 Ride height Magnetic ring Incremental track side 4.5 ±0.5 Reference mark side Pole length
Abrir o catálogo na página 5
Dimensions and installation drawings Technical features Maximum speed Refer to Maximum speed calculator
Abrir o catálogo na página 6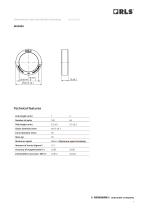
Dimensions and installation drawings Technical features Pole length (mm) Maximum speed Refer to Maximum speed calculator Moment of inertia (kgmm )
Abrir o catálogo na página 7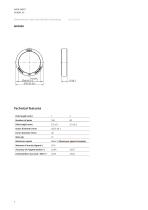
Dimensions and installation drawings Technical features Pole length (mm) Maximum speed Refer to Maximum speed calculator Moment of inertia (kgmm )
Abrir o catálogo na página 8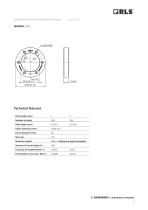
Dimensions and installation drawings Technical features Pole length (mm) Maximum speed Refer to Maximum speed calculator Moment of inertia (kgmm )
Abrir o catálogo na página 9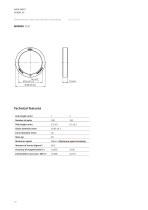
Dimensions and installation drawings Technical features Pole length (mm) Maximum speed Refer to Maximum speed calculator Moment of inertia (kgmm )
Abrir o catálogo na página 10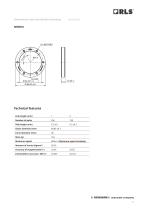
Dimensions and installation drawings Technical features Pole length (mm) Maximum speed Refer to Maximum speed calculator Moment of inertia (kgmm )
Abrir o catálogo na página 11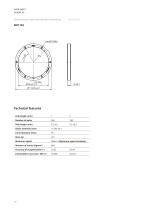
Dimensions and installation drawings Technical features Pole length (mm) Maximum speed Refer to Maximum speed calculator Moment of inertia (kgmm )
Abrir o catálogo na página 12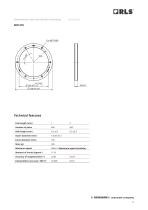
Dimensions and installation drawings Technical features Pole length (mm) Maximum speed Refer to Maximum speed calculator Moment of inertia (kgmm )
Abrir o catálogo na página 13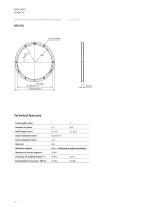
Dimensions and installation drawings Technical features Pole length (mm) Maximum speed Refer to Maximum speed calculator Moment of inertia (kgmm )
Abrir o catálogo na página 14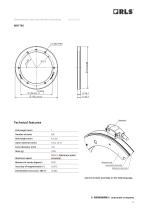
Dimensions and installation drawings Maximum speed Refer to Maximum speed calculator Magnetic ring Incremental track side Reference mark side See the encoder assembly on the follo
Abrir o catálogo na página 15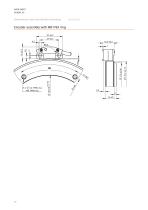
Dimensions and installation drawings Encoder assembly with MR176X ring 37 ±0.2 4.3
Abrir o catálogo na página 16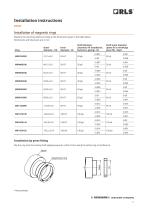
Installation instructions Installation of magnetic rings Machine the mounting shaft according to the dimensions given in the table below. Dimensions and tolerances are in mm. Shaft diameter (clearance fit installation, fasteners, gluing) - Ds Shaft outer diameter (press fit or shrinkage press fit) - Dspd 20 r6 Installation by press-fitting Slip the ring onto the mating shaft applying equal or uniform force along the whole ring circumference. Shaft* Magnetised ring
Abrir o catálogo na página 17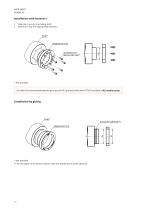
Installation with fasteners 1. 2. Slide the ring onto the mating shaft. Attach the ring with appropriate fasteners. Magnetised ring Shaft* Magnetised ring See table of recommended tightening torques for RLS products (document TTD01) available at RLS media center. * Not provided. ** For the depth of the groove, please check the specifications of the adhesive. Shaft* Magnetised ring Magnetised ring
Abrir o catálogo na página 18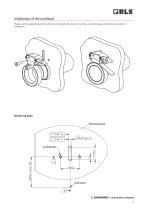
Installation of the readhead Please use the supplied spacer for optimum ride height. For proper mounting, a mounting base should be made prior to installation. Drawing created. Mounting base Mounting surface Shaft center
Abrir o catálogo na página 19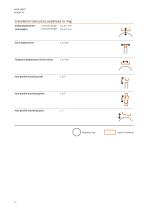
Installation tolerances (readhead to ring) Radial displacement (ride height) 1 mm pole length 2 mm pole length Axial displacement Tangential displacement of the sensor Non-parallel mounting (roll) Non-parallel mounting (pitch) Magnetic ring
Abrir o catálogo na página 20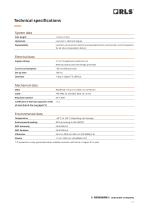
Technical specifications System data Pole length Less than 1 electrical degree Less than ±2 counts for maximum interpolation factor and less than unit of resolution for all other interpolation factors Electrical data Supply voltage 5 V ±10 % (absolute maximum 6 V) Reverse polarity and overvoltage protected Current consumption Set-up time Mechanical data Mass Readhead: 120 g (1 m cable, no connector) Coefficient of thermal expansion (CTE) of steel hub of the ring (ppm/°C) Environmental data Temperature Environmental sealing * IP protection is only guaranteed when suitable connector with same...
Abrir o catálogo na página 21Todos os catálogos e folhetos técnicos RLS
-
ArtosTM_DBD01_05
21 Páginas
-
Artos_DRD01_03
21 Páginas
-
RE58_RE58D04_04
22 Páginas
-
RE22_RE22D01_10
9 Páginas
-
RM22_RM22D01_05
9 Páginas
-
MR_MR01D01_06
55 Páginas
-
MR_MR02D02_04
41 Páginas
-
LM13_LM13D01_13
17 Páginas
-
LM10 Series
20 Páginas
-
AksIM-2_MBD07_05
14 Páginas
-
RE16 / RM16
15 Páginas
-
AksIM-2_MBD01_11
53 Páginas
-
FlexINTM
2 Páginas
-
OnAxis™ Redundant_RDD01_01
14 Páginas
-
Orbis™
2 Páginas
-
DRD01_03
21 Páginas
-
SARD01_02
15 Páginas
-
ArtosTM_DBD01_05
21 Páginas
-
encoder products photosensors
1 Páginas
-
MS Incremental Magnetic Scales
26 Páginas
-
AksIM-4
14 Páginas