Excertos do catálogo
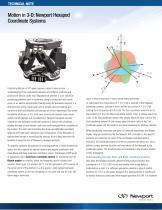
TECHNICAL NOTE Motion in 3-D: Newport Hexapod Coordinate Systems Controlling Motion in 3-D space requires a user to have a clear understanding of the relationship between end effector positions and positions of devices under test. Regardless of whether it is an industrial positioning platform used in machinery, using a cutting tool and a work piece, or an electro-optical beam steering setup for advanced research in a diffractometry using a laser beam and a sample, precise readings and controls of both end effectors and devices are of key importance. Due to the complexity of motion in 3-D, multi-axis systems can present many issues without careful design and considerations. Newport Hexapods provide innovative user-definable coordinate systems to answer this challenge, leading the way of user-friendly multi-axis positioning platforms available on the market. This tech note illustrates the three user-definable coordinate systems and helps with integration and configuration of the Hexapods in experimental setups or manufacturing process, thus to help maximize the benefits of using the line of Newport’s Hexapod products. To uniquely represent the position of a moving platform in three-dimensional space, one must specify its spatial location and angular orientation with three linear and three rotational coordinate values. The Newport HXP series of Hexapods uses a Cartesian coordinate system for translation and the Bryant angles for rotation, which are frequently used in robotics and aviation. (See Figure 1) A position (X Y Z U V W) represents a XYZ location of the center point of the platform in a 3-D space in right-handed Cartesian coordinate system as well as orientation in roll, pitch and yaw (U V W, TaitBryan angles definition). Figure 1: Setup Configuration for Optical Quality Testing with Gimbal To understand how the position (X Y Z U V W) is reached in the Hexapod coordinate systems, consider a move defined by position (X Y Z U V W) starting from the position (0 0 0 0 0 0). The Tool coordinate system is set to the position (X Y Z) in the Work coordinate system. Then, it rotates about the z axis of the Tool coordinate system (W), rotates about the new y axis of the Tool coordinate system (V) and rotates about the new x axis of the Tool coordinate system (U). All rotations are made clockwise for positive rotations. When positioning commands are given in Cartesian coordinates and Bryant angles, they are transformed by the Newport HXP controller to the specific positions and velocities for each of the six Hexapod actuators before execution. All individual positions for the six actuators are taken as a set to define a unique position (location and orientation) of the Hexapod in the coordinate system. The transformation of coordinate to the actuator lengths is fully transparent. Understanding the Tool, Work and Base coordinate systems How does the Hexapod uniquely determine the position (location and orientation in X Y Z U V W)? As we are familiar with scalar fields in mathematics, a point is a sufficient geometric element to specify spatial positions (X Y Z) in a 3-D space. However, this representation is insufficient to identify directions associated with angular positions (U V W). It is however
Abrir o catálogo na página 1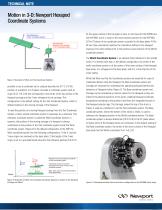
TECHNICAL NOTE Motion in 3-D: Newport Hexapod Coordinate Systems 0), the upper surface of the top plate is close to mid travel for the HXP50 and the HXP1000, and it is close to the lower extreme position for the HXP100); 3) The XY plane of the coordinate system is parallel to the base plate; 4) The W-axis (Yaw orientation) matches the orientation defined in the Hexapod drawing. (The motor cables point in the positive X-axis direction of the World coordinate system.) The World Coordinate System is an absolute fixed reference to the outside world. It is defined such that, in the default...
Abrir o catálogo na página 2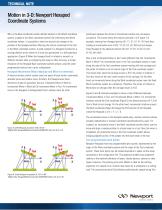
TECHNICAL NOTE Motion in 3-D: Newport Hexapod Coordinate Systems Why is the Base coordinate system defined relative to the World coordinate system, instead of the Work coordinate system? By referencing the World coordinate system, it is possible to take into account any change in the position of the Hexapod without affecting the motion commands of the Tool in the Work coordinate system. A good example is a Hexapod mounted on a moving platform at the center of a multi-axis goniometer in a diffractometry application. (Figure 4) When the Hexapod itself is rotated or moved to a different...
Abrir o catálogo na página 3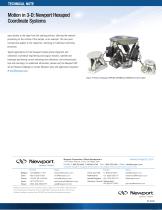
Motion in 3-D: Newport Hexapod Coordinate Systems axes relative to the beam from the starting position, allowing the material processing on the surface of the sample, as an example. This two pivot concept also applies to the inspection, metrology or traditional machining processes. Typical applications for the Hexapod include optical alignment and calibration, biomedical engineering and surgical robotics, satellite and telescope positioning, sensor metrology and calibration, and semiconductor test and metrology. For additional information, please visit the Newport HXP series Hexapod webpage...
Abrir o catálogo na página 4Todos os catálogos e folhetos técnicos MICRO-CONTROLE / Spectra-Physics
-
Precision Motion Control
27 Páginas
-
Motorized Linear Stage Selection Guide
43 Páginas
-
OPTICAL FIBER ALIGNMENT
6 Páginas
-
VGEN/SPFL Component Selection Guide
4 Páginas
-
Wavelength Tunable Faraday Isolators
2 Páginas
-
SA2_90028936F
1 Páginas
-
10BPF10-370_ROHS
1 Páginas
-
10BPF10-320_ROHS
1 Páginas
-
10BPF10-310
1 Páginas
-
M-401
1 Páginas
-
Tunable Diode Lasers
16 Páginas
-
Custom Component Solutions
6 Páginas
-
New Focus Tunable Diode Lasers Brochure
28 Páginas
-
Vision IsoStation Brochure
5 Páginas
-
Nanopositioning Solutions
55 Páginas
-
newport ressource
1640 Páginas
-
Motion PL30
24 Páginas
-
CONEX-AG-LS25-27P
2 Páginas
-
Nanopositioners
40 Páginas
-
Prisms and retroreflectors
9 Páginas
-
Beamsplitters
34 Páginas
-
Spherical and aspherical lenses
35 Páginas
-
Optrical mirror
33 Páginas
-
Electronic Autocollimator CONEX-LDS
10 Páginas
-
Systems Solutions brochure
6 Páginas
-
Fast Steering Mirrors
4 Páginas
-
Optical Delay Line Kit
1 Páginas
-
Long Scan Autocorrelator
1 Páginas
-
I-V Test Station
2 Páginas
-
Projects in Optics
2 Páginas
-
Projects in Interferometry
2 Páginas
-
Azimuth / Elevation Gimbals
2 Páginas
-
Air-Bearing System
2 Páginas
-
Large Motorized Mirror Mounts
2 Páginas
-
X-Ray Diffractometer
2 Páginas
-
Motion System
2 Páginas
-
Pick & Place Machine
2 Páginas
-
Single Axis Air-Bearing System
2 Páginas
-
Metrology Positioning System
2 Páginas
-
SlimLine™ Workstation Table Systems
2 Páginas
-
Ergonomic Workstation Accessories
4 Páginas
-
SG Series Scientific Grade Breadboards
2 Páginas
-
IG Series Industrial Grade Breadboards
2 Páginas
-
I-500 Series Pneumatic Isolators
1 Páginas
-
LabLegs™ Upgrade Kits
1 Páginas
-
UCS Series Cleanroom Tables
1 Páginas
-
TE Series Table Enclosures
1 Páginas
-
RS Series Research Grade Optical Tables
3 Páginas
-
LTE Series Light Tight Enclosure
1 Páginas
-
Oriel Integrating Spheres
5 Páginas
-
Oriel Inspection Probes
1 Páginas
-
Oriel Flanged Sample Compartment
1 Páginas
-
Oriel Cuvettes and Cuvette Holders
1 Páginas
-
Oriel Focusing Lens Assembly
2 Páginas
-
Flat Gratings for Oriel Spectrometers
2 Páginas
-
Xenon Flashlamps
2 Páginas
-
Oriel InstaSpec X CCD
3 Páginas
-
Oriel Mini Monochromator
3 Páginas
-
Oriel 77200 1/4 m Monochromator
3 Páginas
-
Oriel 77250 Series 1/8 m Monochromator
3 Páginas
-
Reflection and Fluorescence Probes
1 Páginas
-
OSM2 Series Spectrometers
2 Páginas
-
Oriel IS Series Minispectrometers
3 Páginas
-
Light Sources for Minispectrometers
1 Páginas
-
Integrating Spheres and Cosine Corrector
1 Páginas
-
Fiber Optics for Minispectrometers
2 Páginas
-
Oriel MS127i™ 1/8 m Imaging Spectrograph
3 Páginas
-
Oriel MS125™ 1/8 m Spectrograph
1 Páginas
-
Oriel Optical Choppers
2 Páginas
-
Oriel Low Cost Electronic Shutter
1 Páginas
-
Electronic Safety Shutters
1 Páginas
-
Oriel Electronic Fast Shutters
2 Páginas
-
Oriel Optical Shutter
1 Páginas
-
Iris Diaphragms
1 Páginas
-
Beam Apertures for Light Sources
1 Páginas
-
Adaptor Washers, Screw Sets
1 Páginas
-
Mounting Bridles
1 Páginas
-
Adaptors and Retaining Rings
1 Páginas
-
Opto-Mechanical Components Set 2
1 Páginas
-
Opto-Mechanical Components Set 1
1 Páginas
-
X95 Structural Rails and Carriers
5 Páginas
-
X26 Series Mirror Mount
1 Páginas
-
X26 Series Cylindrical Laser Mounts
1 Páginas
-
X26 Series Lens Mounts and Holders
4 Páginas
-
X48 Series Aluminum Rails and Carriers
1 Páginas
-
Precision Optical Rails and Carriers
2 Páginas
-
Mini Optical Rails and Carriers
2 Páginas
-
Slotted Bases
2 Páginas
-
SDS Series Angle Brackets
1 Páginas
-
Rotation Adaptor
1 Páginas
-
PI Series Intermediate Adaptor Plates
1 Páginas
-
PBN Series Base Plates
1 Páginas
-
Mounting Plates and Platforms
1 Páginas
-
Modular Riser Plates
1 Páginas
-
Magnetic Bases
2 Páginas
-
Kinematic Stops and Nudgers
1 Páginas
-
Kinematic Bases
2 Páginas
-
Fixed Height Platforms
1 Páginas
-
EQ3 Series Angle Brackets for M-UMR3.5
1 Páginas
-
EQ Series Angle Brackets
2 Páginas
-
Base Clamps
1 Páginas
-
360 Series Angle Brackets
1 Páginas
-
VALUMAX® Posts and Post Holders
1 Páginas
-
Rod Platforms
1 Páginas
-
Rod Clamps
1 Páginas
-
Posts and Post Holders
3 Páginas
-
Post Clamps and Accessories
1 Páginas
-
Pedestal-Base Post Holders
2 Páginas
-
Modular Construction System
1 Páginas
-
Holders for Pedestal Posts
1 Páginas
-
Heavy Duty Rod Systems
2 Páginas
-
Dual Rod Systems
1 Páginas
-
Breadboard Support Posts
1 Páginas
-
Pedestal Post System
2 Páginas
-
VersaStar™ Modular Filter Wheel
1 Páginas
-
Motorized Filter Wheels
1 Páginas
-
Manual Filter Wheels
1 Páginas
-
Indexed Filter Wheel Mounts
1 Páginas
-
Filter Holders
1 Páginas
-
Filter and Optic Holders
1 Páginas
-
V-Blocks
1 Páginas
-
Tip/Tilt Polarizer Rotation Mount
1 Páginas
-
Precision Beam Steerers
1 Páginas
-
Polarizer Rotation Mounts
1 Páginas
-
Pockels Cell Positioner
1 Páginas
-
Kin-a-Flip Mount
1 Páginas
-
Diffraction Grating Mount
2 Páginas
-
Cube Beamsplitter Holders
1 Páginas
-
Beam Steerers
1 Páginas
-
Aegis Qube™ Beam Routing System
5 Páginas
-
Variable Lens Holder
1 Páginas
-
Self-Centering Lens Mounts
1 Páginas
-
Rotatable Lens/Polarizer Mounting System
1 Páginas
-
Precision XY Optic Positioners
1 Páginas
-
Multi-Axis Lens Positioners
4 Páginas
-
Lens Focusing Mount
1 Páginas
-
Fixed Lens Mounts
1 Páginas
-
Cylindrical Lens Holders
1 Páginas
-
Compact Lens Positioners
1 Páginas
-
Adjustable Lens Mounts
1 Páginas
-
Adjustable Cylindrical Lens Mount
1 Páginas
-
UV Objective Lenses
1 Páginas
-
Reflective Microscope Objectives
2 Páginas
-
Precision Objective Lenses
1 Páginas
-
Objective Lenses
1 Páginas
-
Laser Diode Objective Lenses
1 Páginas
-
Ultrafast Laser Thin Film Polarizers
1 Páginas
-
Ultrafast Laser Output Coupler Mirrors
1 Páginas
-
Ultrafast Laser Chirped Mirrors
2 Páginas
-
Ultrafast Laser Broadband 45° Mirrors
1 Páginas
-
Ultrafast Laser Beam Sampler
1 Páginas
-
Broadband Hollow Retroreflectors
1 Páginas
-
Volume Bragg Gratings™
1 Páginas
-
Plane Holographic Reflection Gratings
1 Páginas
-
Plane Ruled Reflection Gratings
2 Páginas
-
Variable Attenuator/Beamsplitters
1 Páginas
-
UV Non-Polarizing Cube Beamsplitters
1 Páginas
-
Pellicle Beamsplitters
1 Páginas
-
Laser Line Non-Polarizing Beamsplitters
1 Páginas
-
Laser Line Polarizing Cube Beamsplitters
1 Páginas
-
Broadband Beam Samplers
1 Páginas
-
Broadband Dielectric Beamsplitters
1 Páginas
-
Zero-Order Quartz Wave Plates
1 Páginas
-
Zero-Order Precision Wave Plates
1 Páginas
-
Precision Linear Polarizers
1 Páginas
-
Polarcor™ Linear Polarizers
1 Páginas
-
Multiple-Order Quartz Wave Plates
1 Páginas
-
Glan-Laser Calcite Polarizers
1 Páginas
-
Glan-Thompson Calcite Polarizers
1 Páginas
-
Broadband Polarizing Cube Beamsplitters
1 Páginas
-
Broadband Polarization Rotators
1 Páginas
-
Achromatic Zero-Order Wave Plates
1 Páginas
-
Infrared Lenses
1 Páginas
-
BK 7 Precision Plano-Concave Lenses
1 Páginas
-
BK 7 Precision Plano-Convex Lenses
2 Páginas
-
BK 7 Precision Bi-Convex Lenses
2 Páginas
-
BK 7 Precision Bi-Concave Lenses
1 Páginas
-
Molded Glass Aspheric Lenses
3 Páginas
-
Aspheric Condenser Lenses
1 Páginas
-
Spherical Ball Micro Lenses
1 Páginas
-
Precision Cylindrical Lens Sets
1 Páginas
-
Precision Achromatic Doublet Lenses
2 Páginas
-
Gradient Index Micro Lenses
2 Páginas
-
BK 7 Precision Cylindrical Lenses
2 Páginas
-
Three-Axis Spatial Filters
2 Páginas
-
Precision Singlet Lens Sets
3 Páginas
-
OptiSet™ Optics Sets
2 Páginas
-
Laser Collimator
1 Páginas
-
Laser Beam Expanders
2 Páginas
-
High-Energy Pinhole Apertures
1 Páginas
-
High-Energy Variable Attenuators
3 Páginas
-
High-Energy Laser Beam Expanders
2 Páginas
-
Faraday Optical Isolator, Free-Space
3 Páginas
-
Electronic Shutter System
1 Páginas
-
Compensated Attenuators
1 Páginas
-
Compact Five-Axis Spatial Filters
2 Páginas
-
UV Beam Viewer
1 Páginas
-
Shear Plate Collimation Tester
1 Páginas
-
Sapphire Windows
1 Páginas
-
Interferometer Flats
1 Páginas
-
High-Energy Laser Wedged Windows
1 Páginas
-
Parallel Windows
1 Páginas
-
Light Pipe Homogenizer
1 Páginas
-
Replicated Hollow Metal Retroreflectors
1 Páginas
-
VALUMAX® Right-Angle Prisms
1 Páginas
-
Precision Right-Angle Prisms
1 Páginas
-
VALUMAX® Broadband Mirrors
2 Páginas
-
Utility Broadband Metallic Mirrors
1 Páginas
-
Ultra-Low Loss SuperMirrors™
2 Páginas
-
Off-Axis Replicated Parabolic Mirrors
1 Páginas
-
Laser Line Dielectric Mirrors
2 Páginas
-
High-Energy Nd:YAG Laser Mirrors
2 Páginas
-
High-Energy Excimer Laser Mirrors
2 Páginas
-
Ellipsoidal and Paraboloidal Reflectors
2 Páginas
-
Concave Broadband Metallic Mirrors
1 Páginas
-
Broadband SuperMirrors™
1 Páginas
-
Broadband Metallic Mirrors
2 Páginas
-
Broadband Dielectric Mirrors
2 Páginas
-
Oriel Thermopile Detector Preamplifier
1 Páginas
-
Oriel TE Cooler Controller
1 Páginas
-
Oriel Laboratory Power Supply
1 Páginas
-
Oriel Current Preamplifier
1 Páginas
-
Oriel Wide Bandwidth Voltage Amplifiers
1 Páginas
-
Oriel Photomultiplier Tube Power Supply
1 Páginas
-
High Resolution CCD Laser Beam Profiler
1 Páginas
-
Micro-Beam Profiler
1 Páginas
-
Laser Beam Profiler
2 Páginas
-
High-Speed Photodetectors, GHz
7 Páginas
-
Oriel TE Cooled HgCdZnTe Detectors
1 Páginas
-
Oriel Silicon Detectors
2 Páginas
-
Oriel Pb and PbSe Detectors
2 Páginas
-
Oriel InGaAs and Ge Detectors
2 Páginas
-
Oriel Miniature Thermopile Detectors
2 Páginas
-
Oriel Photomultiplier Tubes
2 Páginas
-
Portable Optical Power Meter, 842-PE
2 Páginas
-
Laser Power Meter, Analog, 407A
2 Páginas
-
Fiber Optic Detectors
2 Páginas
-
PulseScout Autocorrelator
2 Páginas
-
Heat Control Filters
1 Páginas
-
Colored Glass Filters
3 Páginas
-
Bandpass Filters
4 Páginas
-
Laser Line Filters
2 Páginas
-
Infrared Neutral Density Filters
1 Páginas
-
Absorptive Neutral Density Filters
2 Páginas
-
Short and Long-Wave Pass Filters
2 Páginas
-
Oriel Order Sorting Filters
1 Páginas
-
Photonics Control Devices, Conex™
4 Páginas
-
UZ Series Vertical Linear Stages
2 Páginas
-
VP-5ZA Precision Vertical Linear Stages
2 Páginas
-
LDS-Vector Electronic Autocollimator
2 Páginas
-
HXP100 Hexapod
2 Páginas
-
Microscopy Tools Micromanipulators
4 Páginas
-
NanoPositioning Linear Stages
4 Páginas
-
Objective NanoFocusing Stages
2 Páginas
-
NanoPositioning Piezo Translators
2 Páginas
-
Accessories Controller/Driver Cables
1 Páginas
-
TRA Series Compact Motorized Actuators
2 Páginas
-
Miniature Linear Actuator NewStep Series
1 Páginas
-
LTA Series Precision Motorized Actuators
2 Páginas
-
CMA Series Compact Motorized Actuators
2 Páginas
-
URS Series Precision Rotation Stages
3 Páginas
-
NewStep NSR Series Universal Rotator
2 Páginas
-
BG Series Goniometric Cradles
4 Páginas
-
VP-25X Precision Compact Linear Stages
3 Páginas
-
MFA Series Miniature Linear Stages
2 Páginas
-
GTS Series High-precision linear stages
2 Páginas
-
EL/EN Series Lab Jacks
1 Páginas
-
ECN/ECR Series Lab Jacks
2 Páginas
-
271/281 Series High Load Lab Jacks
2 Páginas
-
Single-Mode Fiber Couplers
1 Páginas
-
Precision Single-Mode Fiber Couplers
1 Páginas
-
Multimode Fiber Couplers
2 Páginas
-
GRIN Lens Fiber Couplers
1 Páginas
-
FPH Series Fiber Chucks and Holders
1 Páginas
-
Fiber Optic Positioners
3 Páginas
-
561/562 Series ULTRAlign™ Accessories
4 Páginas
-
466A Series Options and Accessories
3 Páginas
-
466A Series XYZ Flexure Stages
1 Páginas
-
SM Series Vernier Micrometers
1 Páginas
-
DM Series Differential Micrometers
2 Páginas
-
BM Series Micrometers
2 Páginas
-
BHC Series Precision Adjustment Screws
1 Páginas
-
UTR Series Precision Rotation Stages
3 Páginas
-
RS Series Low-Profile Rotation Stages
1 Páginas
-
30 Series Multi-Axis Tilt Platforms
2 Páginas
-
TSX-1D Series Dovetail Linear Stages
1 Páginas
-
MT Series Compact Dovetail Linear Stages
2 Páginas
-
MS Series Miniature Linear Stages
4 Páginas
-
DS Series Compact Dovetail Linear Stages
2 Páginas
-
Oriel® Radiometric Fiber Optic Source
1 Páginas
-
Apex Fiber Illuminators
2 Páginas
-
Series Q Deuterium Sources
1 Páginas
-
Deuterium Lamp Power Supplies
1 Páginas
-
Deuterium Lamps
2 Páginas
-
Apex Deuterium Lamp Sources
1 Páginas
-
Spacer Tubes for Light Sources
1 Páginas
-
Oriel Ozone Eater
1 Páginas
-
Ozone Blowers
1 Páginas
-
Flange Mounted Cells
1 Páginas
-
Digital Light Intensity Controller
2 Páginas
-
Beam Turning Assemblies
2 Páginas
-
Aspherab Lens Assemblies
2 Páginas
-
Mounts for Beam Probes
1 Páginas
-
Manual Iris Diaphragms for Light Sources
1 Páginas
-
Liquid Filters for Light Sources
1 Páginas
-
Input Hood for Light Sources
1 Páginas
-
Holders for Oriel Single Fibers
2 Páginas
-
Holders for Oriel Flanged Components
2 Páginas
-
Flexible Light Shields for Light Sources
1 Páginas
-
Flanged Mounts for Fiber Bundles
1 Páginas
-
Filter Holder for Beam Probes
1 Páginas
-
Diffusing Beam Probes for Fiber Bundles
1 Páginas
-
Coupling Rings for Light Sources
1 Páginas
-
Beam Splitting Module for Beam Probes
1 Páginas
-
Flood Exposure Sources
6 Páginas
-
Mask Alignment Tools
4 Páginas
-
Reference Solar Cell and Meter
1 Páginas
-
Class A Solar Simulators
3 Páginas
-
1600 W Oriel Solar Simulators
4 Páginas
-
150 - 300 W Solar Simulators
2 Páginas
-
150 W Low Cost Solar Simulator
2 Páginas
-
Apex Monochromator Illuminators
4 Páginas
-
7340 Series Monochromator Illuminators
2 Páginas
-
Quartz Tungsten Halogen Lamps
3 Páginas
-
Blackbodies
2 Páginas
-
Apex Quartz Tungsten Halogen Sources
2 Páginas
-
Apex Infrared Light Sources
2 Páginas
-
Bandpass Filters for Solar Simulators
1 Páginas
-
Xenon Flashlamp Systems
2 Páginas
-
Uniform Illuminators
3 Páginas
-
Simplicity Series Arc Sources
2 Páginas
-
Series Q Lamp Housings
4 Páginas
-
Series Q Arc Lamp Sources
2 Páginas
-
Silicon Carbide Light Source
1 Páginas
-
Oriel PhotoMax Lamp Housing
3 Páginas
-
Fading Test System
1 Páginas
-
Digital Arc Lamp Power Supplies
2 Páginas
-
Modular Infrared Light Sources
2 Páginas
-
Digital Radiometric Power Supplies
2 Páginas
-
DC Short Arc Lamps
3 Páginas
-
50 - 200 W Research Arc Lamp Sources
2 Páginas
-
450 - 1000 W Research Arc Lamp Sources
2 Páginas
-
1600 W Research Arc Lamp Sources
1 Páginas
-
Research Arc Lamp Housings
3 Páginas
-
Apex Arc Lamp Sources
2 Páginas
-
Calibrated Sources and Services
2 Páginas
-
200 - 500 W Hg Research Arc Sources
2 Páginas
-
Pencil Style Calibration Lamps
3 Páginas
-
High Power Spectral Calibration Lamps
2 Páginas
-
Laser Diode Adaptors
1 Páginas
-
Cylindrical Laser Mounts
1 Páginas
-
762 Series High-Power Laser Diode Mounts
3 Páginas
-
Laser Diode Drivers, 500B Series
2 Páginas
-
TEC Controller, 300B Series
2 Páginas
-
Solano Series Air-Cooled Ion Lasers
1 Páginas
-
163C AIR-COOLED ION LASER SYSTEMS
2 Páginas
-
163D AIR-COOLED ION LASER SYSTEMS
2 Páginas
-
163A AIR-COOLED ION LASER SYSTEMS
2 Páginas
-
VBG Raman Laser Modules
2 Páginas
-
Laser Diode Modules, LQN Series
2 Páginas
-
Alignment Laser
1 Páginas
-
Ultraviolet Safety Equipment
1 Páginas
-
Laser Safety Glasses and Goggles
4 Páginas
-
Laser Safety Windows
1 Páginas
-
Infrared IR Viewer
1 Páginas
-
177 Air-Cooled Ion Lasers
2 Páginas
-
Beam Dump
1 Páginas
-
Empower ® Q-Switched Laser
2 Páginas
-
V-Xtreme™ Q-Switched Laser
2 Páginas
-
HIPPO™ High Power Q-switched Laser
4 Páginas
-
Fiber Pigtailed Laser Diode
1 Páginas
-
488 nm CW Laser- Cyan™ OEM
2 Páginas
-
CW Lasers- Excelsior® OEM
4 Páginas
-
Automated Ultrafast OPA-TOPAS™
4 Páginas
-
Inspire™ OPO Family
2 Páginas
-
Unison™ Ultrafast Amplifier System
4 Páginas
-
Scan Series Nanosecond OPO Family
6 Páginas
-
3900S Titanium:Sapphire CW Laser
4 Páginas
-
WaveTrain® CW Frequency Doubler
2 Páginas
-
Excelsior™ Low Power CW Lasers
4 Páginas
-
Polarization Controller, Manual
2 Páginas
-
Polarization Beam Combiner/Splitter
1 Páginas
-
DPSS Lasers- Millenia® Prime™
3 Páginas
-
Fiber Optic In-Line Polarizers
1 Páginas
-
Spitfire® Pro XP Ultrafast Amplifier
2 Páginas
-
Fiber Optic Depolarizers
1 Páginas
-
Quanta-Ray® Nd-YAG Laser Family
5 Páginas
-
Fiber Optic Faraday Rotator Mirrors
1 Páginas
-
Mode Scrambler
1 Páginas
-
Index-Matching Fluid
1 Páginas
-
Fiber Optic Scribes
1 Páginas
-
Fiber Optic Mating Adapter Sleeves
1 Páginas
-
Fiber Jacket Stripper
1 Páginas
-
Variable Ratio Couplers
2 Páginas
-
Fixed Fiber Optic Attenuator
1 Páginas
-
Fiber Optic Switches
2 Páginas
-
Fiber Optic In-Line Isolators
1 Páginas
-
Kevlar® Shears
1 Páginas
-
Polarization Insensitive Circulators
1 Páginas
-
Fiber Preparation Kit
1 Páginas
-
Fiber Optic Splice
1 Páginas
-
Benchtop Couplers and WDMs
1 Páginas
-
Fiber Coating Stripper
1 Páginas
-
Ferrules for Oriel Fiber Bundles
1 Páginas
-
Electronic Fiber Cleavers
1 Páginas
-
Coupler for Oriel Fiber Bundles
1 Páginas
-
Fiber Optic Isolator
2 Páginas
-
Fiber Pigtailed Collimator
1 Páginas
-
Fiber Optic Collimators
2 Páginas
-
Tunable Bandpass Fiber Optic Filter
2 Páginas
-
Polarization Extinction Ratio Meter
1 Páginas
-
Single Mode Fibers, Bend-Insensitive
1 Páginas
-
Single Mode Fibers and Patch Cords
2 Páginas
-
Photosensitive Fiber for Fiber Gratings
1 Páginas
-
Photonic Crystal Fibers
4 Páginas
-
Oriel Multi-track Fiber Bundles
2 Páginas
-
Communication Grade Fibers
1 Páginas
-
Infrared Fibers
1 Páginas
-
Supercontinuum Generation Fiber Devices
1 Páginas
-
Single Branch Fiber Bundles
1 Páginas
-
Multi-Branch Fiber Optic Bundles
1 Páginas
-
Power Delivery Fibers
1 Páginas
-
Liquid Light Guides
2 Páginas