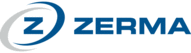
Catalog excerpts
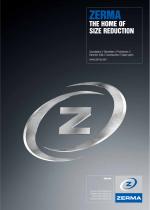
THE HOME OF SIZE REDUCTION Granulators // Shredders // Pulverizers // Hammer mills // Accessories // Spare parts www.zerma.com PLASTIC SIZE REDUCTION RUBBER SIZE REDUCTION WOOD SIZE REDUCTION E-WASTE SIZE REDUCTION
Open the catalog to page 1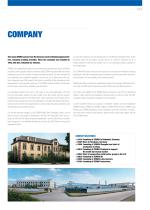
COMPANY The name ZERMA comes from the German word zerkleinerungsmaschinen, meaning crushing machine. Since the company was founded in 1943, this has remained our mission. ZERMA has traditionally focused on the development and production of size reduction machinery for the plastics industry. However, today ZERMA has expanded into related industries such as tire recycling, e-waste and wood recycling. Our core strength lies as a machinery and component producer. As such we are an ideal partner for systems integrators and OEM projects. We remain committed to the improvement and development of...
Open the catalog to page 2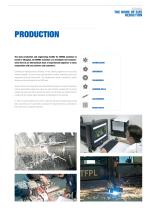
ZERMA THE HOME OF SIZE REDUCTION PRODUCTION The main production and engineering facility for ZERMA machines is based in Shanghai. All ZERMA machines are developed and manufactured here by an international team of experienced engineers in close cooperation with our partners and customers. Everything is manufactured by ourselves, we are avoiding suppliers and out sourcing wherever possible. This has only be made possible by modern machining centres and experienced and well trained staff. This independence makes it possible to quickly develop and test prototypes for our R&D team. Quality...
Open the catalog to page 3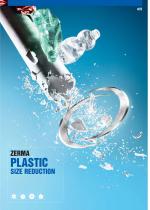
ZERMA PLASTIC SIZE REDUCTION
Open the catalog to page 4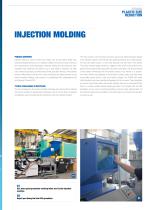
ZERMA PLASTIC SIZE REDUCTION INJECTION MOLDING PROCESS OVERVIEW Injection molding is used to create many things such as wire spools, bottle caps, automotive dashboards and so on. Injection molding is the most common method of part manufacturing. Some advantages of injection molding are high production rates, repeatable high tolerances, the ability to use a wide range of materials, low labor cost, minimal scrap losses, and little need to finish parts after molding. In the injection process melted plastic is forced into a mold creating the part. Most polymers can be used for injection molding,...
Open the catalog to page 5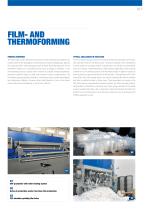
FILM- AND THERMOFORMING PROCESS OVERVIEW Thermoforming and film blowing are processes in which generally thin products are created mainly for the packaging. Common products include shopping bags, packing film, agricultural film, food packaging as well as thicker thermoforming parts for the automotive industry or in household articles such as fridges or bathtubs. In the thermoforming process a plastic sheet is heated to a pliable forming temperature, formed to a specific shape in a mold, and trimmed to create a usable product. The film blowing process basically consists of a extruding a tube of...
Open the catalog to page 6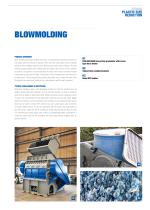
ZERMA PLASTIC SIZE REDUCTION BLOWMOLDING PROCESS OVERVIEW Blow molding also known as blow forming is a manufacturing process by which hollow plastic parts are formed. In general, there are three main types of blow molding: extrusion blow molding, injection blow molding, and stretch blow molding. The blow molding process begins with melting down the plastic and forming it into a parison or preform. The parison is a tube-like piece of plastic with a hole in one end in which compressed air can pass through. The parison is then clamped into a mold and air is pumped into it. The air pressure...
Open the catalog to page 7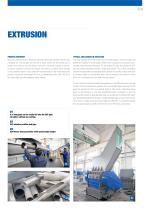
EXTRUSION PROCESS OVERVIEW Pipe and profile extrusion is defined as a process of forcing the polymer melt through a shaping die. The extrudate from the die is sized, cooled and the formed pipe is pulled to the winder or a cut off device. Prior to this, the plastic material in the form of polymer granules is fed into the hopper, conveyed by a rotating screw through a long cylindrical barrel. This is subjected simultaneously to high temperature and pressure, forcing the melt through the die at a predetermined rate. After PVC, PE is the most widely used thermoplastic piping material. TYPICAL...
Open the catalog to page 8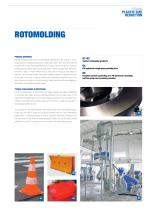
ZERMA PLASTIC SIZE REDUCTION ROTOMOLDING PROCESS OVERVIEW Rotational molding, also known as rotomolding, rotocasting or spin casting, is a molding process for creating many kinds of mostly hollow items. More than 80% of all the material used is from the polyethylene family. Typical products created in a rotational molding process include large volume water tanks, childrens playgrounds, barricades and traffic cones. A heated hollow mold is filled with a charge or shot weight of material, it is then slowly rotated causing the softened material to disperse and stick to the walls of the mold. In...
Open the catalog to page 9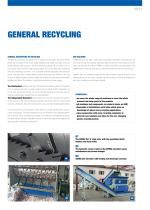
GENERAL RECYCLING GENERAL DESCRIPTION OF RECYCLING The general recycling is the oldest form of recycling. In the plastic industry it started pretty late compared to the much longer existing scrap metal and paper and card board collectors and recyclers. Also the achieved recycling rate at around 25% is much lower than in the two longer existing areas. This on the other hand makes the field very interesting as there‘s a lot of growth potential especially with raising oil prices. One thing which makes plastic recycling more and more difficult is the vast amount of different plastics and their...
Open the catalog to page 10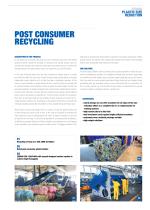
ZERMA PLASTIC SIZE REDUCTION POST CONSUMER RECYCLING DESCRIPTION OF THE PROCESS As the latest way of recycling the post consumer recycling is also one of the fastest growing markets, caused by shortage of resources and soaring energy costs. On one side new products are made from daily waste we produce and on the other side refused products with good caloric values are turned into e.g. fuels for boilers. In the case of turning waste into new raw materials the plastic stream is usually pre-sorted by either the consumer himself, through waste sorting plants or through independent waste...
Open the catalog to page 11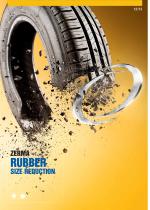
SIZE REDUCTION
Open the catalog to page 12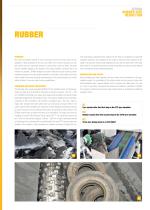
ZERMA RUBBER SIZE REDUCTION RUBBER OVERVIEW Due to the increasing number of cars and trucks all over the world, used tires are available in large quantities at very low cost. With a bit of clever recycling, you can get a whole lot out of used tires: granule in various sizes, steel and profit. The sales income naturally depeds on the quality of the output material a process that is as efficient as possible. ZERMA designed a system dedicated to tyre recycling, which ultimately produces very high-quality materials for recycling. Final products could be either shreds for thermal recycling,...
Open the catalog to page 13All ZERMA Europe GmbH & Co. KG catalogs and technical brochures
-
GSC 700
2 Pages
-
CM G/H/S/Q
20 Pages
-
CM Q
1 Pages
-
CM S
1 Pages
-
CM G/H
1 Pages
-
ZERMA products all
56 Pages
-
ZXS/ZSS/ZPS/ZIS/ZRS/ZHS
24 Pages
-
GSH
20 Pages
-
GST/GST/GSE
24 Pages
-
ZTS/ZTTS
2 Pages
-
ZHM
2 Pages
-
PM
2 Pages
-
ZRS
2 Pages
-
ZXS
2 Pages
-
ZHS+
2 Pages
-
ZHS
2 Pages
-
ZIS
2 Pages
-
ZSS/ZPS
2 Pages
-
GSP
2 Pages
-
GSH 1100
2 Pages
-
GSH 800
2 Pages
-
GSH 600/700
2 Pages
-
GSH 350/500
2 Pages
-
GST old Series
2 Pages
-
GSC 500
2 Pages
-
GSE 700
2 Pages
-
GSE 500
2 Pages
-
GSE 300
2 Pages
-
GSC 300
2 Pages
-
ZBS Compact shredder
2 Pages
-
Slow speed granulators GSL
11 Pages
-
GSL 300
2 Pages