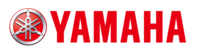
Catalog excerpts

The Conveyor Solution Book Solutions to conveyance issues ear h lin roug akth ncept bre A r co veyo con A ne w comp act co n ve y o r c o n c e p t th a t o ffe r s b o th speed an d f l exi bility 1. LCM100 linear conveyor VS conventional types 2. Examples of solutions LCM100 conveyor 3. Message from the LCM100 developers
Open the catalog to page 1
Conventional type conveyors • Mechanical stoppers or sensors are required at each stop position. • Complicated control due to various conveyor components. • Stopper adjustments are required each time the stop position is changed. • Fixed productivity rate. • Requires various process for productivity. LCM100 Linear Conveyor Module • Direct-drive carriages. • Programmable stop positions. • No mechanical stoppers or external sensors required. • Maximum speed of 3 m/sec for better transfer time. • Adjustable transfer speed for total line flow coordination. • Actual task times can be easily...
Open the catalog to page 2
2. Examples of solutions LCM100 can offer Switch to the LCM100 from conventional conveyor for shorter conveyance tact times For a speedy assembly line without stops due to line problems Conventional conveyor issues Tact time too long? Frequent stops due to line problems? Various unnecessary line components? Free-flow conveyors, suchas roller conveyors and belt Conventional type conveyors are the most common transport method in Forced stop by stopper Slow conveyance speed assembly lines. However, these conventional conveyor types tend to have slow transfer speeds which increase the tact...
Open the catalog to page 3
2. Examples of solutions LCM100 can offer Flexibility in line design: Setting desired speed, direction, and stop positions. Build sophisticated forking and merging lines. Conventional conveyor issues The manufacturing line floor space too large? Too many in-progress workpieces between processes? Conventional conveyors move only in the forward Conventional type The same process exists at 2 locations on the line direction (one way only). Therefore, in cases where the same process exists at multiple line locations, the equipment for repeating that process is required at each of those...
Open the catalog to page 4
2. Examples of solutions LCM100 can offer Perform assembly tasks directly on the conveyor line. Reducing assembly equipment space. Conventional conveyor issues Need to increase productivity? Need to reduce line footprint? Production efficiency would be greatly enhanced by the Conventional type ability to perform assembly tasks, etc., with the workpieces remaining on the line itself. The low rigidity of conventional Workpiece is pulled from the line conveyors does not mechanically support process tasks to Workpieces must be moved between the line pallet and the task stand (extra work) be...
Open the catalog to page 5
2. Examples of solutions CM100 can offer A perfect fit for small-lot production Flexibility in optimal line layout for product type and operation. Conventional conveyor issues Time consuming setup changeovers and stop position changes? Time-consuming startup. Once a conventional conveyor line has been built, it Conventional type Changing the conveyor line configuration requires time and labor Stopper positions must be changed requires considerable time and effort to reconfigure it. Doing so require changes in both hardware and software, such as adjusting the stopper positions and sensor...
Open the catalog to page 6
2. Examples of solutions LCM100 can offer • Long recovery time after a system failure. • Single-axis robots are expensive items, and replacement parts cannot be kept in stock. • Line down for extended periods. When using a single-axis robot in conveyance applications, keeping expensive replacement parts in stock can be cost prohibitive. In such cases, considerable time is required from the point when a part is ordered until system recovery is possible. • Standardized parts for easy maintenance. • Simple part replacements. • Conveyor down time can be minimized. The LCM100 component parts...
Open the catalog to page 7
3. Messages from the developers Message from the development leaders of YAMAHA's innovative leap from a "flow" to a "move" conveyor concept The next-generation LCM100 conveyor supersedes belt and roller conveyors The LCM100 was developed as the successor to belt and roller conveyors. A single LCM100 module comprises a linear motor, slider, and controller, with workpieces being placed on the slider. The slider speed and stop positions, etc., are determined by the controller, resulting in an extremely flexible format that enables high-speed, high-accuracy conveyance. Conventional conveyors...
Open the catalog to page 8All Yamaha Motor Co. catalogs and technical brochures
-
ROBOT CATLOG 2021-2022
771 Pages
-
GF series
2 Pages
-
R series
3 Pages
-
SS series
6 Pages
-
LCMR200
27 Pages
-
YRG-2005SS
2 Pages
-
YAMAHA Vision System Ivy2
6 Pages
-
NEW SCARA ROBOT : YK400XE
6 Pages
-
YAMAHA SCARA LINEUP Catalogue
95 Pages
-
YAMAHA SCARA No.1
2 Pages
-
Lineup Catalog
14 Pages
-
Infomation
32 Pages
-
Electric grippers
14 Pages
-
ROBOT VISION iVY2
13 Pages
-
Clean robots
44 Pages
-
Pick & place robots
10 Pages
-
Controllers
132 Pages
-
SCARA robots
67 Pages
-
Cartesian robots
128 Pages
-
Linear motor single axis robots
27 Pages
-
Single axis robots
46 Pages
-
Vertically articulated robots
14 Pages
-
YAMAHA ROBOT Catalog 2018
627 Pages
Archived catalogs
-
YAMAHA ROBOT CATALOG 2020/2021
673 Pages