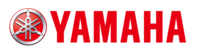
Catalog excerpts
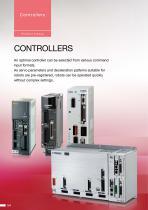
Product Lineup CONTROLLERS An optimal controller can be selected from various command input formats. As servo parameters and deceleration patterns suitable for robots are pre-registered, robots can be operated quickly without complex settings.
Open the catalog to page 1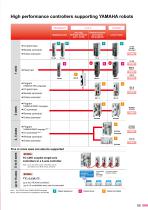
High performance controllers supporting YAMAHA robots TRANSERVO Stepping motor • I/O point trace • Remote command • Online command [T4L/T5L] Small type servomotor (24 V • 30 W) Linear motor • Pulse train Program •(YAMAHA SRC language) • I/O point trace • Remote command • Online command Program •(YAMAHA BASIC language) • I/O command • Remote command • Online command Program •(YAMAHA BASIC language) • I/O command • Remote command • Online command Five or more axes can also be supported RCX240 YC-LINK couples single-axis controllers to a 4-axis controller Note : Up to four SR1 series...
Open the catalog to page 2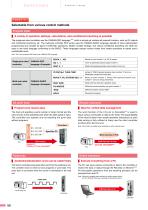
Product Lineup Program input | A variety of operation settings, calculations, and conditional branching is possible The single-axis robot controllers use the YAMAHA SRC language Note which is simple yet contains all required functions, such as I/O outputs and conditional branching, etc. The multi-axis controller RCX series uses the YAMAHA BASIC language capable of more sophisticated programming and includes all types of arithmetic operations, flexible variable settings, and various conditional branching, etc. Both are easy to use robot language conforming to the BASIC. These languages...
Open the catalog to page 3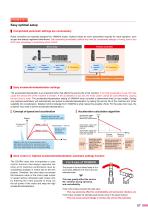
Easy optimal setup Complicated parameter settings are unnecessary Robot controllers are specially designed for YAMAHA robots. Optimal values for servo parameters required for robot operation, such as gain are already registered beforehand. Start operating immediately without any need for complicated settings or tuning, even if you don't have knowledge or experience about control. Servo amp Yamaha controller Control device and motion unit Gain adjustment (tuning) Motion 2. parameter settings Return-to-origin 3. System construction Control device Specify payload mass Servo parameter...
Open the catalog to page 4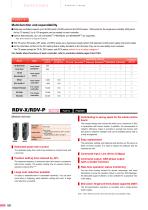
Product Lineup ControllersPOINT 3 Multi-function and expandability ■ Multi-axis controllers support up to 30,000 points (10,000 points for the RCX2 series, 1,000 points for the single-axis controller (255 points for the TS series)). Up to 100 programs can be created on each controller. ■ Various field networks, CC-Link, DeviceNet™, PROFIBUS, and EtherNet/IP™ are supported. Note. Some models do not support all networks. ■ The TS series, RD series, SR1 series, and RCX series use a dual-power supply system with separate control power supply and power supply. ■ As the controllers conform to the...
Open the catalog to page 5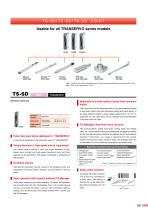
Note 1. The STH type vertical specifications and RF type sensor specifications do not support the TS-SD. Note 2. SG07 is only applicable to TS-SH. [Robot driver] Operation method | Pulse train input driver dedicated to "TRANSERVO" A robot driver dedicated to the pulse train input for "TRANSERVO". | Torque decrease in high-speed area is suppressed As a vector control method is used, the torque decrease in highspeed area is small and high-speed operation even with high payload can be performed. This greatly contributes to shortening of the tact time. | Excellent silence High-pitched operation...
Open the catalog to page 6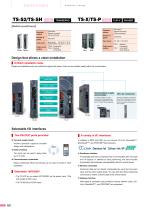
Product Lineup P.492 TRANSERVO TS-X/TS-P P.492 FLIP-X PHASER [Robot positioner] Operation method Operation method Design that allows a clean installation | Unified installation sizes Height and installation pitch are unified throughout the series. Units can be installed neatly within the control board. Absolute battery is neatly accommodated The absolute battery is stored inside the unit. Replacement can be performed easily from the front side. (TS-X and TS-SH supported) TS-X DIN rail installation On-board installation is made easy by the DIN rail installation mechanism that is standard on...
Open the catalog to page 7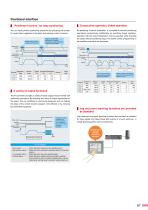
| "Positioner function" for easy positioning | Consecutive operation, linked operation You can easily perform positioning operations by specifying the number of a point that is registered in the data, and entering a start command. By specifying a branch destination, it is possible to execute positioning operations consecutively. Additionally, by specifying linked operation, operation with the branch destination can be executed while changing the speed without positioning stops; this allows control programming to be simplified and takt to be shortened. If jog input is within a specific time,...
Open the catalog to page 8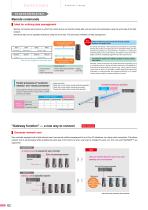
Product Lineup Remote commands are functions by which the control device can directly handle data such as points and parameters using the word area of the field network. Numerical data can be operated directly by using the word area. This promotes unification of data management. O: Parallel processing possible y Parallel processing is possible/ Big "Gateway function" — a new way to connect | Decrease network cost One controller equipped with a field network board can provide unified management of up to four I/O interfaces via a daisy-chain connection. This allows network cost to be...
Open the catalog to page 9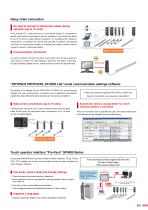
Daisy chain connection No need to connect or disconnect cables during operation (up to 16 units) From a single PC, handy terminal, or touch-panel display, it is possible to specify point data and parameters, perform operations, and monitor the status for up to 16 axes on daisy-chained controllers. For everything from design to maintenance, a connection to only the first controller is sufficient; any desired controller can be accessed simply by switching the station number, without having to connect or disconnect cables. Pro-face touch-panel Communication commands An easily handled command...
Open the catalog to page 10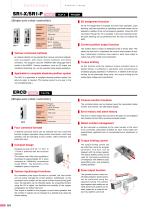
Product Lineup [Single-axis robot controller] Operation method | Various command methods An optimal method can be selected from various command methods, such as program, point trace, remote command, and online command. The program uses the YAMAHA SRC language that is similar to the BASIC. Various operations, such as I/O output and conditional branching, etc. can be executed using simple operations. | Applicable to complete absolute position system The SR1-X is applicable to complete absolute position system. No return-to-origin is needed. (The backup period is one year in the non-energizing...
Open the catalog to page 11All Yamaha Motor Co. catalogs and technical brochures
-
GF series
2 Pages
-
R series
3 Pages
-
SS series
6 Pages
-
LCMR200
27 Pages
-
YRG-2005SS
2 Pages
-
YAMAHA ROBOT CATALOG 2020/2021
673 Pages
-
YAMAHA Vision System Ivy2
6 Pages
-
NEW SCARA ROBOT : YK400XE
6 Pages
-
YAMAHA SCARA LINEUP Catalogue
95 Pages
-
YAMAHA SCARA No.1
2 Pages
-
Lineup Catalog
14 Pages
-
Infomation
32 Pages
-
Electric grippers
14 Pages
-
ROBOT VISION iVY2
13 Pages
-
Clean robots
44 Pages
-
Pick & place robots
10 Pages
-
SCARA robots
67 Pages
-
Cartesian robots
128 Pages
-
Linear motor single axis robots
27 Pages
-
Single axis robots
46 Pages
-
Vertically articulated robots
14 Pages
-
YAMAHA ROBOT Catalog 2018
627 Pages