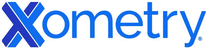

Catalog excerpts
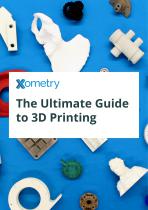
The Ultimate Guide to 3D Printing
Open the catalog to page 1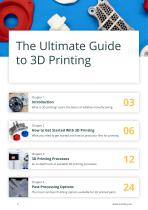
The Ultimate Guide to 3D Printing Chapter 1 Introduction What is 3D printing? Learn the basics of additive manufacturing. How to Get Started With 3D Printing What you need to get started and how to prep your files for printing. 3D Printing Processes An in-depth look at available 3D printing processes. Post-Processing Options The most common finishing options available for 3D printed parts.
Open the catalog to page 2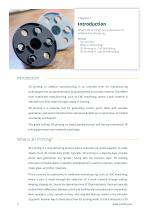
Introduction What is 3D printing? Learn the basics of additive manufacturing. Sections Introduction What is 3D Printing? 3D Printing vs. CNC Machining 3D Printing vs. Injection Moulding Introduction 3D printing, or additive manufacturing, is an umbrella term for manufacturing technologies that can generate parts by growing them out of base material. This differs from subtractive manufacturing, such as CNC machining, where a bulk material is reduced to its final shape through cutting or forming. 3D printing is a powerful tool for generating custom parts, often with complex geometries, and...
Open the catalog to page 3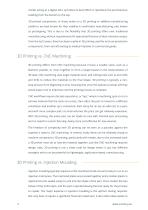
model, acting as a digital twin, and does its best effort to reproduce the part features, building from the bottom to the top. 3D printed components, or those made on a 3D printing or additive manufacturing platform, are best known for their viability in small-batch manufacturing, also known as prototyping. This is due to the flexibility that 3D printing offers over traditional manufacturing, without requirements for specialized fixtures or labor-intensive setups. Over the last 5 years, there has been a spike in 3D printing used for end-use production components, from aircraft ducting to...
Open the catalog to page 4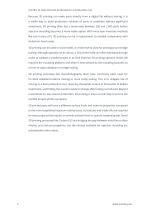
months to have the tool produced for a production run. Because 3D printing can make parts directly from a digital file without tooling, it is a viable way to build production volumes of parts in quantities without significant investment. 3D printing often has a break-even between 250 and 2,000 parts before injection moulding becomes a more viable option. With more lean inventory methods like just-in-time (JIT), 3D printing can be a replacement to molded components with limited on-hand needs. 3D printing can be used to build molds, or mold inserts used for prototype and bridge tooling....
Open the catalog to page 5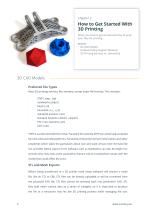
How to Get Started With 3D Printing What you need to get started and how to prep your files for printing. Sections • 3D CAD Models • Understanding Support Material • 3D Printing Services vs. Ownership 3D CAD Models Preferred File Types Most 3D printing services, like Xometry, accept major file formats. This includes: • Solidworks (sldprt) Dassault Systems (.3dxml, .catpart) STEP is a preferred CAD file format. Parasolid formats like STEP are universally accepted by most CAD and CAM platforms. Parasolids inherently hold unit information and other properties which takes the guesswork about...
Open the catalog to page 6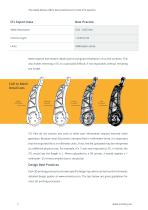
The table below offers best practices for most STL exports. Best Practice Mesh Resolution Chord Length Mesh exports lose feature detail due to triangular tessellation of curved surfaces. This also makes reversing a STL to a parasolid difficult, if not impossible, without remaking the model. CAD to Mesh Detail Loss Parasolid Features STL files do not contain any units or other part information beyond external mesh geometry. Because most 3D printers interpret files in millimeters (mm), it is important that the exported file is in millimeter units. If not, the file uploaded may be interpreted...
Open the catalog to page 7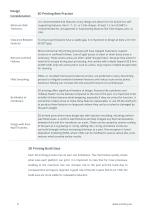
Design Consideration 3D Printing Best Practice Minimum Wall Thickness It is recommended that features of any design are above 0.6 mm (0.024”) on selfsupporting features, like X-, T-, O-, or C-like shapes. At least 1.2 mm (0.048”) is recommended for unsupported or load bearing features like I-like shapes, pins, or tabs. Clearance Between Features To ensure part features have a usable gap, it is important to design at least a 0.5 mm (0.020”) gap. Remove Confined Hollows Most commercial 3D printing processes will have trapped material or support structure in confined hollows. Line-of-sight...
Open the catalog to page 8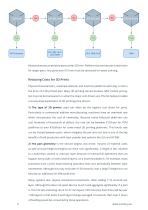
Most processes can produce parts under 229 mm. Platform size can become a restriction for larger parts. Any parts over 915 mm must be sectioned for easier printing. Reducing Costs for 3D Prints Physical characteristics, materials selected, and machine platforms each play a role in the price of a 3D printed part. Many 3D printing service bureaus offer instant pricing, but may not be transparent on what the major cost drivers are. The list below provides a survey-level explanation of 3D printing price drivers. 1) The type of 3D printer used can often be the highest cost driver for parts....
Open the catalog to page 9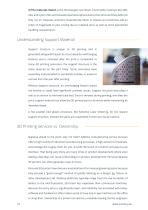
3) The material chosen is the third-largest cost driver. Commodity materials like ABS, ASA, and nylon often are the least expensive options due to their price and the platforms they run on. However, premium materials like Ultem or metals can sometimes add an order of magnitude to part costing due to material price as well as more specialized handling requirements. Understanding Support Material Support structure is unique to 3D printing and is generated along with the part to act as a base for overhanging features and is removed after the print is completed. In many 3D printing processes,...
Open the catalog to page 10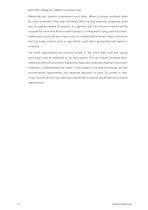
learning to design for additive manufacturing. Ownership and services complement each other. Where in-house machines allow for rapid verification, they may not always offer the best materials, properties, build size, or capacity needed for projects. As a general rule, if an in-house machine will be occupied for more than 48 hours with a project, it is likely worth using a service bureau. Additionally, service bureaus have access to multiple platforms with larger build areas that can easily produce parts in days which could take a personal printer weeks to complete. The more sophisticated...
Open the catalog to page 11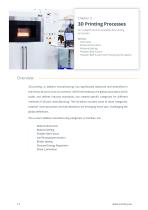
3D Printing Processes An in-depth look at available 3D printing processes. Sections Overview Material Extrusion Material Jetting Powder Bed Fusion Powder Bed Fusion Vat Photopolymerisation Overview 3D printing, or additive manufacturing, has significantly advanced and diversified in the nearly 40 years since its invention. ASTM International, the global association which builds and defines industry standards, has created specific categories for different methods of 3D part manufacturing. The list below includes some of those categories, however novel processes and hybridizations are...
Open the catalog to page 12