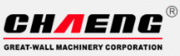

Catalog excerpts
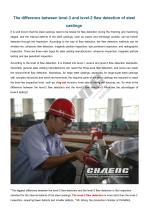
The difference between level-3 and level-2 flaw detection of steel castings It is well known that the steel castings need to be tested for flaw detection during the finishing and machining stages, and the internal defects of the steel castings, such as cracks and shrinkage cavities, can be further detected through the inspection. According to the way of flaw detection, the flaw detection methods can be divided into: ultrasonic flaw detection, magnetic particle inspection, dye penetrant inspection, and radiographic inspection. There are three main types for steel casting manufacturers: ultrasonic inspection, magnetic particle testing and dye penetrant inspection. According to the level of flaw detection, it is divided into level-1, level-2 and level-3 flaw detection standards. Generally, general steel casting manufacturers can reach the three-level flaw detection, and some can reach the second-level flaw detection. Nowadays, for large steel castings, especially for large-scale steel castings with complex structures and harsh environments, the required parts of the steel castings are required to reach the level two inspection level, such as: slag pot trunnion, inner side of rolling mill housing, etc. So what is the difference between the level-2 flaw detection and the level-3 flaw detection? What are the advantages of level-2 testing? "The biggest difference between the level-2 flaw detection and the level-3 flaw detection is the inspection standard for the internal defects of the steel castings. The level-2 flaw detection is more strict than the level-3 inspection, requiring fewer defects and smaller defects. " Mr. Wang, the production minister of CHAENG
Open the catalog to page 1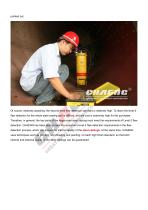
Of course, relatively speaking, the second-level flaw detection standard is relatively high. To reach the level-2 flaw detection for the whole steel casting part is difficult, and the cost is extremely high for the purchaser. Therefore, in general, the key parts of the large-scale steel casting must meet the requirements of Level-2 flaw detection. CHAENG has been able to meet the customer's level-2 flaw detection requirements in the flaw detection process, which can ensure the internal quality of the steel castings. At the same time, CHAENG uses techniques such as grinding, shot blasting...
Open the catalog to page 2All Xinxiang Great Wall Machinery Co. catalogs and technical brochures
-
slag grinding plant+CHAENG
1 Pages
-
slag pot manufacturing
1 Pages
-
Vertical Lime Kiln of CHAENG
1 Pages
-
Slag Vertical Roller Mill
1 Pages
-
Kiln supporting roller
1 Pages
-
Stone crusher
4 Pages
-
Vertical roller mill
5 Pages
-
Ball mill
5 Pages
-
The supporting roller
4 Pages
-
Slag pot manufacturer-CHAENG
3 Pages
-
Riding ring of rotary kiln
4 Pages
-
features
5 Pages
-
Ball mill end cover
5 Pages
-
Vertical mill rocker arm
4 Pages
-
Cement rotary kiln
4 Pages
-
Slag pot
5 Pages
-
Kiln tyre
4 Pages
-
Active lime production line
4 Pages
-
Cement grinding plant
5 Pages
-
Cement ball mill
4 Pages
-
CRUSHING PLANT
3 Pages
-
COAL VERTICAL MILL
4 Pages
-
DUST COLLECTOR
3 Pages
-
FEEDING MACHINE
3 Pages
-
VERTICAL CEMENT MILL
4 Pages
-
GRATE COOLER
3 Pages
-
COAL MILL
4 Pages
-
GRINDING TABLE
4 Pages
-
ROD MILL
3 Pages
-
RAW MATERIAL VERTICAL MILL
4 Pages
-
ROATRY DRYER
3 Pages
-
GRINDING ROLLER
4 Pages
-
GIRTH GEAR
5 Pages
-
CONE CRUSHER LINER
3 Pages
-
BALL MILL TRUNNION
3 Pages
-
WEAR-RESISTANT STEEL BALL
3 Pages
-
PREHEATER
3 Pages
-
JAW CRUSHER
2 Pages
-
BALL MILL LINER
3 Pages
-
Slag grinding plant
8 Pages
-
kiln sipporting roller
4 Pages
-
lime rotary kiln
4 Pages
-
Cement rotary kiln,
4 Pages
Archived catalogs
-
GRM Series
2 Pages