

Catalog excerpts
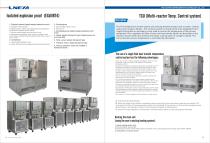
WUXI GUANYA REFRIGERATION TECHNOLOGY CO., LTD. Isolated explosion proof (EXdllBT4) TCU (Multi-reactor Temp. Control system) 1. Electrical cabinet (adopt Isolated explosion proof) A. Separate wiring chamber. B. Heating power >7.5KW, with independent heat dissipation aluminum fins explosion-proof cabinet. C. Electric cabinet adopts whole aluminum mold. D. Equipped with explosion-proof mouse, to operate 7-inch touch screen (optional Siemens explosion-proof touch screen - 7 inch, 12 inch). A. Using isolated explosion proof. B. Adopt Terminal block packaging process (Intrinsically safe) The TCU temperature control system uses existing thermal energy (such as steam, cooling water, and cryogenic liquids - the "primary system") infrastructure to be integrated into a single fluid system or secondary circuit used to control the temperature of the process equipment. This completes the flow of only one heat transfer liquid into the jacket of the reaction vessel (rather than directly into steam, cooling water or cryogenic liquid). The entire reaction process temperature is controlled by calculation. A. Using isolated explosion proof The use of a single fluid heat transfer temperature control system has the following advantages: A. the user can get a closed, repeatable temperature control in a wide temperature range, can achieve -120 degrees to 300 degrees temperature control; B. Avoid the replacement of traditional equipment and facilities and the maintenance of jacket; the small fluid volume also ensures the rapid response of the control loop and the thermal reaction delay is small; C. Built-in electric heating heat transfer oil auxiliary system, which can automatically turn on the auxiliary heating system according to the demand to reduce the steam use pressure; D. It can achieve accurate energy saving by accurately matching the heat demand with fast operation; E. Control the temperature of the whole reaction process through precise and fast calculation, and perform rapid response control for the exothermic and endothermic reactions in the whole reaction process; F. Reserve a standardized interface, which can increase the heat source heat exchange module according to actual needs; G. optionally controlling the reaction process temperature and the single fluid temperature, and the temperature difference between the reaction process temperature and the thermal single fluid temperature is settable and controllable; H. can carry out recipe management and production process records; A. Fully enclosed pipe design. B. Open the Angle of the electric regulating valve according to the instructions given by the system PLC, and control the flow of low-temperature liquid into the jacket of the reactor, so as to achieve energy saving and efficiency. All signals fed back to the process are based on temperature C. Ensure the safe operation of the system, and the electric valve can be fully opened manually Heating the main unit (using the user's existing heating system): 1. electric heating system host Schematic diagram see example According to the system needs heating power and jacket volume, heat storage volume design power 50kW~1000kW 2. Using steam as a power source
Open the catalog to page 1All Wuxi Guanya Temperature Refrigeration Technology Co. Ltd.. catalogs and technical brochures
-
LNEYA-33-Freezer-1
1 Pages
-
LNEYA-32-Thermostatic Bath
1 Pages
-
LNEYA-31-Heating Circulator
1 Pages
-
LNEYA-factory
1 Pages
-
LNEYA-2-Company Profile
1 Pages
-
Heating Circulator
1 Pages
-
LNEYA-3-Products Catalogue
1 Pages