

Catalog excerpts
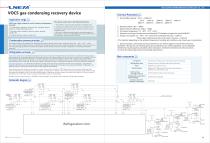
WUXI GUANYA REFRIGERATION TECHNOLOGY CO., LTD. Technical Parameters VOCS gas condensing recovery device The device works well in the following districts: 1. Tank districts: emptying valve respiratory volatilization loss; 2. Loading and unloading area: tanker exhaust volatilization loss; 3. Production delivery area: cylinder, stirred tank reactor solvent volatilization loss; 4. All kinds of volatile chemicals loading, chemical storage and transportation, chemical and pharmaceutical industry generated by the recovery of various volatile VOCS gas. Application range VOCS gas single material or multi-material condensation recovery. 1. Hydrocarbons: gasoline, crude oil, fuel, kerosene, diesel, heavy oil, mixed hydrocarbons etc. 2. Aromatic class: benzene, toluene, xylene, styrene, naphtha etc. 3. Alcohols, ethers, ketones, esters etc. Condensation process principle The volatile VOCS gas is introduced into the equipment cold box (device sets the max. condensing temp. 3°C -40^ -75°C -115*0 ) can customize other temperature zone, condensation and liquefied step by step. Some continuous production process in low temp zone has two-way switching process (if one side of the ice block, directly switch to the other cold box condensation, ice blocking with defrost treatment). Refrigreation principle 800m3/h 1000m3/h 1500m3/h 2000m3/h 2X Operating power: 3kw ~ 300kw 3n System pressure difference: 250pa ~ 450pa 4X The lowest temperature: 3°C -40°C -75°C -115°C 5X Explosion-proof type: Positive pressure EXpxdmbll CT4 Isolation of explosion-proof EXdll BT4 6X energy consumption: 3°C -40°C -75°C three level condensate recovery > 100m3/h Three-stage condensing recovery unit power consumes < 0.2kw/m3 (This indicator depending on the ambient temperature, humidity, site conditions and solvent gas concentration) 7% Exhaust emission: solvent gas recovery & treatment, can meet of 20g/m3 environmental emissions standards; if the gas has a low boiling point gas (condensation but without liquefied), can be separated, treated and recycled again by activated carbon adsorption, membrane treatment and other processes, to ensure the exhaust gas meet environmental requirements. Main components Compressor refrigeration compressor discharge of high temp, and pressure refrigerant into the condenser is condensed into high pressure supercooled liquid, go through expansion valve change into low temp, pressure vapor and liquid mixture, then go into the evaporator (Primary heat exchanger,secondary heat exchanger, third heat exchanger), the refrigerant absorbs medium heat to vaporize and sucked into the compression chamber by the compressor to continue next cycle. Medium is transferred by pump to the VOCS gas condensing cold box and heat exchange with the VOC gas. By continuous repeat of the below process, so VOC gas can realized recovery and continuous reduction. VOCS gas condensate - gas inside the condensing unit heat exchanger will be cooled after transfer heat to refrigerant, using different material in different temp, with saturated vapor pressure difference, cooling the oil and gas to the supersaturated state, condensation into liquid and recycle, small amount of gas enters the back stage for reprocessing. Some process requires continuous production, in order to ensure the continuity of VOCS gas recovery in this process, Double gas path channel condensing unit VOCS gas recovery equipment can be chosen (- 40<€ & - Tb'C) .when one side air pressure drops to the set value, the system automatically switch to the other standby system. Meanwhile, ice block channel will defrost, after defrost it will auto recover to constant temp, control state, ensure continuous and stable recovery of overflow gas. Standard cold box heat exchanger is: SUS304 fin heat exchanger, can customize other materials VOC gas heat exchanger. Schematic diagram Firstgrade low temp, pretreatment shell and tube heat exchanger t ir-sr 10Kpa@1t-5t: TF-501 Fifth grade general cooling treatment shell and tube heat exchanger -40t~-45t a-45t-50t Sixth grade cryogenic treatment shell and TK-ED1 : Second grade general cooling treatment shell and tube heat exchanger -40*C - -45-C !-45t~50t Third grade cryogenic 1 j treatment shell and ^ tube heat exchanger (Exhaust emission Fourth grade heat recovery shell and tube heat exchanger | Refrigeration Unit TKOOI-LS-OD2 High liquid level 7K0DFL5H-O01 I High limit alarm level I Recovery oil output pump Drain outlet Recycle oil _ TK002-L2-OOI I I TK~QQ£ -L -L Low liquid level lOKpa @-80t -50t P~003 Oil and gas TT n' i Recovery oil output pump _ recovery tank | i _ t~ _ h^9q4 Drain outlet 1 Recovery oil output pump —h»4---^ Drain outlet
Open the catalog to page 1All Wuxi Guanya Temperature Refrigeration Technology Co. Ltd.. catalogs and technical brochures
-
LNEYA-33-Freezer-1
1 Pages
-
LNEYA-32-Thermostatic Bath
1 Pages
-
LNEYA-31-Heating Circulator
1 Pages
-
LNEYA-factory
1 Pages
-
LNEYA-2-Company Profile
1 Pages
-
Heating Circulator
1 Pages
-
LNEYA-3-Products Catalogue
1 Pages