

Catalog excerpts
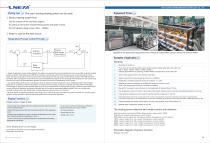
♦ It can be set control the temperature difference between the jacket and reactor material. ♦ Air-venting display. ♦ Simple Menu to use. ♦ Display clear curve. ^LNEy/l"- Heating host (The user's existing heating system can be used) 1. Electric heating system host See the example of the schematic diagram According to the system required heating power and jacket volume, thermal capacity design, power 50kw ~ lOOOkw 2. Steam is used as the heat source Temperature Process Control Principle 1. Adopt changing the control setting method, the system can response the process lag behind as soon as possible, to get the smallest system overshoot. Controlled by two PID(PID is a variable in each group) control loop structure, known as the two sets of control loops: the main circuit and from the circuit, the main control loop from the loop output as the settings. System with feedforward PV, the master PID loop operation results of the PV output and feedforward signals as the composite of the settings from the control loop, through such control of the temperature gradient to ensure the accuracy of temperature control system. 2. Our special design predictor will come about a dynamic signal yc(t) which instead of PV y(t) as a feedback signal. And will take a signal e(t) for controller to make the anticipation of control not too big delay, so that the controller will always make a reasonable control signal. In other word, the dynamic signal yc(t) will be in normal work even though with big delay. However, using common PID control will become obviously time delay in process, and will not get the reasonable feedback signal in the time of delay when controller output, in that case, totally result in system response overshoot even out of control. 3. By three points for sampling (material process temp, point, outlet temp, point and inlet temp, point) and with our company special dynamic control calculation combine with resist feedforward concatenation algorithm. Display Functions Display various images & data ♦ Touchscreen Color Display Functions. Clearly show the real-time control of various temperatures. ♦ Shows the liquid level of the heat conducting medium in the expansion vessel. ♦ Displays the temperature control ( materials temperature control mode, heat conducting medium temperature control) ♦ There is the function of setting refrigeration temperature and heating temperature individually. Clear Temperature Curve Display Can enlarge or shrink the curve and support U drive data exporting in excel format. WUXI GUANYA REFRIGERATION TECHNOLOGY CO., LTD. Applied to the production equipment, each module is independent, placed next to the reaction kettle Examples of application Working The heating power selection and coolant control unit selection Heating system host selects 250kw Regenerative tube selects 1500L Selection of coolant temperature control system 250L 500L reactor select ZLF-25 2group coolant temperature control system 1000L reactor select ZLF-40 coolant temperature control system 2000L reactor select ZLF-80 coolant temperature control system 3000L reactor select ZLF-120 coolant temperature control system 5000L reactor select ZLF-200 coolant temperature control system Schematic diagram of system structure Details on p.35
Open the catalog to page 1All Wuxi Guanya Temperature Refrigeration Technology Co. Ltd.. catalogs and technical brochures
-
LNEYA-33-Freezer-1
1 Pages
-
LNEYA-32-Thermostatic Bath
1 Pages
-
LNEYA-31-Heating Circulator
1 Pages
-
LNEYA-factory
1 Pages
-
LNEYA-2-Company Profile
1 Pages
-
Heating Circulator
1 Pages
-
LNEYA-3-Products Catalogue
1 Pages