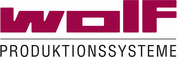

Catalog excerpts
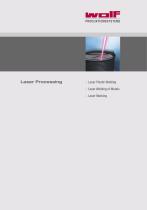
Laser Processing Laser Plastic Welding Laser Welding of Metals Laser Marking
Open the catalog to page 1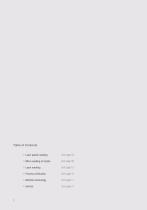
Table of Contents Laser plastic welding Micro welding of metals Laser marking Process verification Machine technology Service from page 04 from page 09 from page 12 from page 16 from page 17 from page 21
Open the catalog to page 2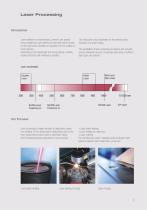
Laser radiation is monochromatic, coherent, can spread almost parallel and can therefore be extremely well focussed, so that high beam intensities are possible over the smallest of cross-sections. Depending on the wavelength and energy density, a widely varying interaction with materials is possible. This interaction is also dependent on the selected pulse frequency and pulse energy. The possibilities of laser processing are diverse and complex, and are delivered using an increasingly wide range of different laser types and systems. Diode Laser Nd:YAG Laser Nd:YAG Laser Frequency x3...
Open the catalog to page 3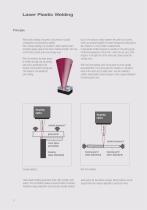
With plastic welding, the parts to be joined are usually overlapped and transmission welded. With overlap welding, it is possible to attain welding seam strengths largely equal to the basic material strength, with very small melting zones and a low energy input. With this method, the laser beam is emitted through the top joining part and is absorbed by the surface of the bottom joining part. This results in the absorbing part melting. Due to the surface contact between the parts to be joined, which are pressed together, the laser-transparent joining part is also melted on a very limited,...
Open the catalog to page 4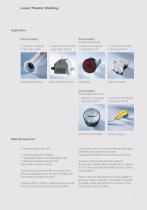
cycle time: 3,2 s per part laser output: 2x50 W Butt joint welding cycle time: 3 s per part laser output: 28 W Overlap welding Contour welding process cycle time: 4 s per part laser output: 40 W cycle time: 6 s per part laser output: 50 W Overlap welding Quasi-simultaneous process cycle time: 4,5 s per part laser output: 120 W cycle time: 3,6 s per part laser output: 200 W Material Selection It is always possible to laser-weld: all thermoplastics with themselves thermoplastic elastomers with thermoplastics and different thermoplastics with each other using the laser transmission method. The...
Open the catalog to page 5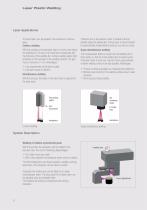
The laser beam can be applied to the workpiece in various ways: Contour welding With this process, a focused laser beam is moved once along the welding line. The size of the focal spot corresponds with the thickness of the welding line. Contour welding places high demands on the evenness of the welding surfaces. The gap must not exceed 0.1 mm, Advantages: Low requirements on the beam quality Low laser output is sufficient Simultaneous welding With this process, the shape of the laser beam is adjusted to the weld seam. Therefore, the to be welded contour is heated uniformly steadily along...
Open the catalog to page 6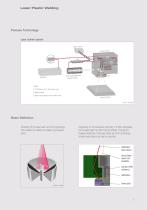
Laser scanner system Beam Deflection Deflection of the laser beam via mirror technology. Depending on the workpiece geometry, it is often impossible This enables the welding of rotation-symmetrical for the laser beam to reach the joint directly. Through the parts. targeted deflection of the laser beam via mirror technology, covered weld seams can also be reached,
Open the catalog to page 7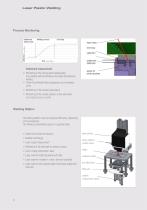
Settlement measurement Monitoring of the sinking depth (setting path), only possible with simultaneous and quasi-simultaneous welding Check the deflection/time progression via an envelope curve Monitoring of the process temperature Monitoring of the contact pressure at the weld seam via a digital pressure monitor The welding stations may be configured differently, depending on the workpieces. The following characteristics apply on a general basis: Stable and precise construction Modular technology Laser output measurement Monitoring of the weld path by distance sensor Quick change...
Open the catalog to page 8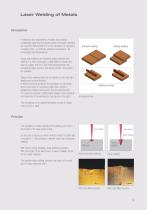
In electronic and mechatronic modules and products increasingly expanding functional scopes and power densities are required. Miniaturisation is on the increase. It is necessary to design joints - in particular electrical connections - for increasingly high temperatures. Gluing and soldering are frequently being replaced with welding. It is often necessary to weld different metals here, such as copper with iron. Wolf Produktionssysteme has developed a laser process, with which precise micro-welds are possible. Typical micro-welding tasks can be divided up into butt joint welding and overlap...
Open the catalog to page 9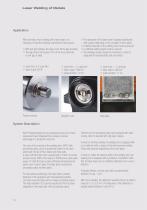
With automatic micro-welding with a laser beam, it is necessary to take the following requirements into account: With butt joint welding, the beam must hit the gap precisely. The gap should not exceed 10% of the focus diameter. A zero-gap is ideal. The absorption of the laser beam fluctuates significantly with copper, depending on the condition of the surface. A defined diameter of the welding zone must be ensured A sufficient welding depth must be ensured. The welding process should be monitored, in order to safeguard the reproducibility and avoid faults. cycle time: 0,7 s per Part laser...
Open the catalog to page 10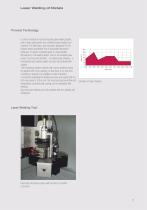
In order to enable a high and reproducible welding depth, both a high pulse power and a defined pulse duration are required. The fibre laser used has been designed for this. Despite these possibilities, the unfavourable absorption behaviour of copper materials leads to unacceptable fluctuations in the welding depth. Due to the variable pulse power over the pulse duration - so-called pulse shaping - a consistently high welding depth can also be achieved with copper. The monitoring systems familiar with macro-welding cannot be applied with micro-welding, so that there is no real-time...
Open the catalog to page 11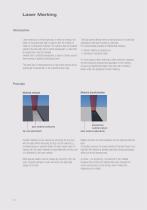
Laser marking is a thermal process, in which an energy-rich beam of focussed laser light is used to alter the surface or inside of a transparent material. This requires that the material absorbs the laser light with a certain wavelength, in order that its appearance may be changed. Viewed from a practical perspective, a laser is a beam source that transmits a tightly bundled light beam. This laser light is characterised by a high power density and a wavelength characteristic of the respective laser type. The high power density with a small focal spot is of particular significance with laser...
Open the catalog to page 12All Wolf Produktionssysteme GmbH & Co.KG catalogs and technical brochures
-
Special Soldering
22 Pages
-
Assembly Automation
16 Pages
-
Image brochure
20 Pages