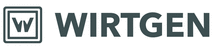

Catalog excerpts
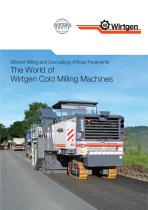
Efcient Milling and Granulating of Road Pavements The World of Wirtgen Cold Milling Machines
Open the catalog to page 1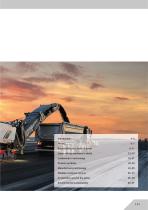
Small milling machines in detail Large milling machines in detail Product portfolio Manufacturing technology Reliable customer service In operation around the globe Environmental sustainability
Open the catalog to page 3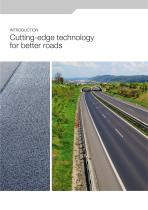
Cutting-edge technology for better roads
Open the catalog to page 4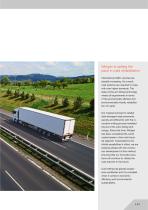
Wirtgen is setting the pace in road rehabilitation International trafc volumes are steadily increasing. As a result, road systems are required to cope with ever higher demands. The state-of-the-art milling technology meets all requirements in terms of the economically efcient and environmentally friendly rehabilitation of roads. Our inspired concept to rehabilitate damaged road pavements quickly and efciently with the innovative milling process heralded the era of the cold milling technology. Since that time, Wirtgen has been considered the world market leader in this multi-faceted segment....
Open the catalog to page 5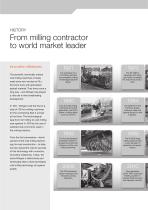
From milling contractor to world market leader Innovative milestones The powerful, technically mature cold milling machines of today need some two minutes to ll a 30-tonne truck with granulated asphalt material. They have come a long way – and Wirtgen has played a vital role in their breathtaking development. In 1971, Wirtgen built the rst of a total of 100 hot milling machines for the contracting eet it owned at that time. The technological leap from hot milling to cold milling was sparked in 1979 by the use of carbide tools commonly used in the mining industry. From the rst cornerstone –...
Open the catalog to page 6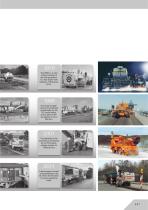
1979 The 3800 C, a cold milling machine of the first generation, is a rear loader with hydraulic milling drum drive. 1988 The range of applications is broadened considerably by the DC model range, which offers working depths of up to 300 mm. 2001 The flexibility of the machines is enhanced by the FCS quickchange system for milling drums. 2011 A dual-engine concept is implemented in the W 210 for the first time to reduce operating costs.
Open the catalog to page 7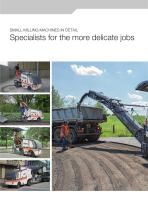
SMALL MILLING MACHINES IN DETAIL Specialists for the more delicate jobs
Open the catalog to page 8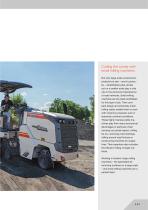
Cutting the corner with small milling machines Not only large-scale construction projects but also – and in particular – rehabilitation jobs carried out on a smaller scale play a vital role in the structural maintenance of road networks. Small milling machines are the ideal candidates for this type of job. Their compact design and extremely small milling radius enable them to work with maximum precision even in extremely conned conditions. These highly manoeuvrable machines play their many economical advantages in particular when carrying out partial repairs, milling tie-ins, removing road...
Open the catalog to page 9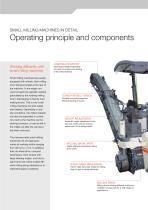
SMALL MILLING MACHINES IN DETAIL Operating principle and components Working efciently with small milling machines Small milling machines are usually equipped with wheels, their milling drum being arranged at the rear of the machine. A one-stage conveyor accepts the asphalt material granulated by the rotating milling drum, discharging it directly onto waiting trucks. This is why small milling machines are also called rear loaders. Depending on job site conditions, the milled material can also be deposited in a windrow next to the machine via the slewing conveyor, or can be left in the milled...
Open the catalog to page 10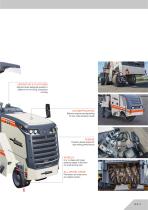
OPERATOR’S PLATFORM Ergonomically designed operator’s platform for non-tiring, productive working SOUNDPROOFING Effective engine soundproong for low noise emission levels ENGINE Powerful diesel engine for high milling performance WHEELS 3 or 4 wheels with large steering angles at the front for small turning radii ALL-WHEEL DRIVE Permanent all-wheel drive for reliable traction
Open the catalog to page 11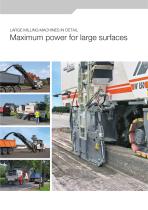
LARGE MILLING MACHINES IN DETAIL Maximum power for large surfaces
Open the catalog to page 12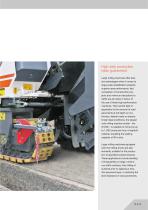
High daily production rates guaranteed Large milling machines offer decisive advantages when it comes to large-scale rehabilitation projects: superior area performance, fast completion of construction projects and minimum disruptions to trafc are all marks in favour of the use of these high-performance machines. Their central eld of application is the removal of road pavements at full depth on motorways, federal roads or airports. Under ideal conditions, the largest cold milling machine model – the W 250i – is capable of removing up to 1,200 tonnes per hour of asphalt material, equalling...
Open the catalog to page 13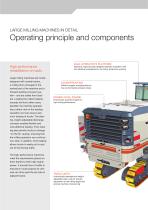
LARGE MILLING MACHINES IN DETAIL Operating principle and components DUAL OPERATOR’S PLATFORM High-performance rehabilitation of roads Large milling machines are mostly designed with crawler tracks, a milling drum arranged in the central part of the machine and a forward-loading conveyor system – and are called front loaders. Loading the milled material towards the front offers many benets: the machine operator has a direct view of the loading operation and can ensure optimum loading of trucks. The slewing, height-adjustable discharge conveyor enables exible and cost-effective loading. Front...
Open the catalog to page 14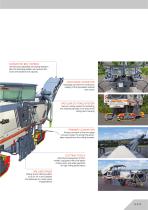
CONVEYOR BELT SPEED Continuously adjustable conveying speed to alter the discharge pattern and ensure that trucks are loaded to full capacity DISCHARGE CONVEYOR Discharge conveyor for continuous loading of the granulated material onto trucks VACUUM CUTTING SYSTEM Vacuum cutting system for extracting ne material particles in the area of the milling drum housing PRIMARY CONVEYOR Primary conveyor of the two-stage conveyor system to accept the granulated material from the milling chamber CUTTING TOOLS Optimized arrangement of toolholders, equipped with point-attack cutting tools, and edge...
Open the catalog to page 15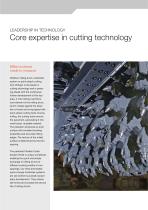
Core expertise in cutting technology Milled surfaces made to measure Whether milling drum, toolholder system or point-attack cutting tool: Wirtgen is the leader in cutting technology and is pressing ahead with the continuous further development of this key area. A cold milling machine’s core element is the milling drum, which rotates against the direction of travel and is equipped with point-attack cutting tools. During milling, the cutting tools remove the pavement, granulating it into small-sized, reusable material. The operation produces an even surface with excellent bonding properties...
Open the catalog to page 16All Wirtgen catalogs and technical brochures
-
COLD MILLING MACHINE W 210 F (i)
44 Pages
-
Cold Milling Machine W 200 Hi
52 Pages
-
COLD MILLING MACHINE W 200 F i
46 Pages
-
W 35 Ri COLD MILLING MACHINE
32 Pages
-
SP 64 / SP 64i
24 Pages
-
Slipform paver SP 1200
24 Pages
-
Side Feeder ISF 94 / ISF 94i
20 Pages
-
4200 SM
40 Pages
-
Cold Milling Machine W 210 XP
56 Pages
-
W 205 Cold Milling Machine
20 Pages
-
Foamed bitumen
28 Pages
-
S-Pack
8 Pages
-
Job reports and references
8 Pages
-
Surface Miner 2200 SM 3.8
36 Pages
-
Surface Miner 2200 SM
40 Pages
-
Cold Milling Machine W 1900
24 Pages
-
Side feeder ISF 850
8 Pages
-
Cold recycler 3800 CR
26 Pages
-
Slipform paver SP 1600
8 Pages
-
Surface Miner 2500 SM
22 Pages
-
Cold milling machine W 60i
20 Pages
-
Cold milling machine W 50 DC
32 Pages
-
Cold milling machine W 50
24 Pages
-
Cold milling machine W 35 DC
24 Pages
-
Dinting machine 2600
8 Pages
-
Slipform paver SP 150
20 Pages
-
Binding agent spreaders
20 Pages
-
Cold recycler 2200 CR
32 Pages
-
Recycler/Stabilizer WR 2000
28 Pages
Archived catalogs
-
Cold Milling Machine W35 Ri 2020
36 Pages