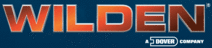
Catalog excerpts
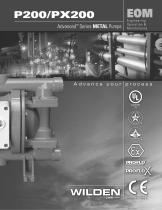
P200/PX200 Advanced™ Series METAL Pumps Engineering Operation & Maintenance Advance your process
Open the catalog to page 1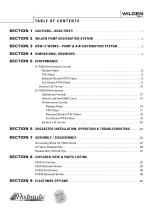
TA B L E O F C O N T E N T S SECTION 1 CAUTIONS—READ FIRST! SECTION 2 WILDEN PUMP DESIGNATION SYSTEM SECTION 3 HOW IT WORKS—PUMP & AIR DISTRIBUTION SYSTEM . . . . . . . . . . . . . . . . . . 3 SECTION 4 DIMENSIONAL DRAWINGS . . . . . . . . . . . . . . . . . . . . . . . . . . . . . . . . . . . . . . . . . . . . . . . . . . 4 SECTION 5 PERFORMANCE A. P200 Performance Curves Rubber-Fitted . . . . . . . . . . . . . . . . . . . . . . . . . . . . . . . . . . . . . . . . . . . . . . . . . . . . . . . . . . . . . . 8 TPE-Fitted . . . . . . . . . . . . . . . . . . . . . . . . . . . . . . . . . . . ....
Open the catalog to page 2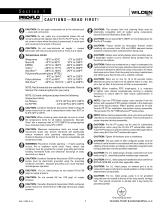
Section 1 CAUTIONS—READ FIRST! CAUTION: Do not apply compressed air to the exhaust port — pump will not function. CAUTION: The process uid and cleaning uids must be chemically compatible with all wetted pump components. Consult Chemical Resistance Guide (E4). CAUTION: Do not, under any circumstance loosen the set screw located at the adjuster dial of the Pro-Flo X™ pump. If the set screw is loose when the pump is pressurized, it could eject and cause injury to anyone in the area. CAUTION: Do not exceed 82°C (180°F) air inlet temperature for Pro-Flo X™ models. CAUTION: Pumps should be...
Open the catalog to page 3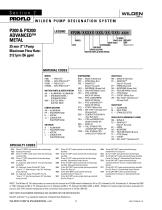
XP200 / XXXX X / XXX / XX / X XX / XXXX MODEL ATEX 25 mm (1") Pump Maximum Flow Rate: 212 lpm (56 gpm) O-RINGS VALVE SEAT SPECIALTY CODE VALVE BALLS (if applicable) DIAPHRAGMS AIR VALVE CENTER SECTION WETTED PARTS & OUTER PISTON DIAPHRAGMS BNS = BUNA-N (Red Dot) EPS = EPDM (Blue Dot) FSS = SANIFLEXTM [Hytrel® (Cream)] NES = NEOPRENE (Green Dot) PUS = POLYURETHANE (Clear) TEU = PTFE w/EPDM BACK-UP (White) TNU = PTFE w/NEOPRENE BACK-UP (White) TSU = PTFE w/SANIFLEX™ BACK-UP (White) VTS = VITON® (White Dot) WFS = WIL-FLEXTM [Santoprene® (Orange Dot)] XBS = CONDUCTIVE BUNA-N (Two Red Dots) TXU...
Open the catalog to page 4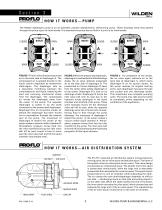
Section 3 HOW IT WORKS—PUMP The Wilden diaphragm pump is an air-operated, positive displacement, self-priming pump. These drawings show ow pattern through the pump upon its initial stroke. It is assumed the pump has no uid in it prior to its initial stroke. FIGURE 1 The air valve directs pressurized air to the back side of diaphragm A. The compressed air is applied directly to the liquid column separated by elastomeric diaphragms. The diaphragm acts as a separation membrane between the compressed air and liquid, balancing the load and removing mechanical stress from the diaphragm. The...
Open the catalog to page 5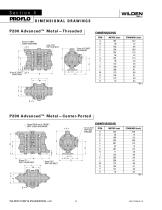
PROGRESSIVE PUMP TECHNOLOGY DIMENSIONAL DRAWINGS P200 Advanced™ Metal— Threaded LIQUID DISCHARGE LIQUID INLET WILDEN PUMP & ENGINEERING, LLC
Open the catalog to page 6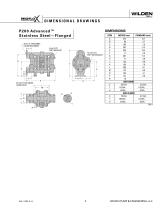
DIMENSIONAL DRAWINGS Stainless Steel — Flanged LIQUID DISCHARGE WILDEN PUMP & ENGINEERING, LLC
Open the catalog to page 7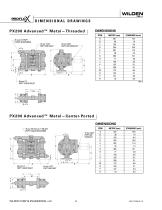
DIMENSIONAL DRAWINGS LIQUID DISCHARGE FNPT LIQUID INLET WILDEN PUMP & ENGINEERING, LLC
Open the catalog to page 8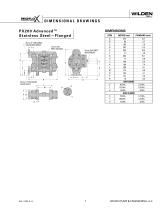
DIMENSIONAL DRAWINGS Stainless Steel — Flanged LIQUID DISCHARGE WILDEN PUMP & ENGINEERING, LLC
Open the catalog to page 9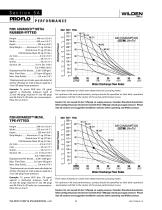
'Displacement per stroke was calculated at 4.8 bar (70 psig) air inlet pressure against a 2 bar (30 psig) head pressure. against a discharge pressure head of 3.3 bar (48 psig) requires 4.1 bar (60 psig) Water Discharge Flow Rates Flow rates indicated on chart were determined by pumping water. For optimum life and performance, pumps should be specified so that daily operation -parameters will fall in the center of the pump performance curve. Caution: Do not exceed 8.6 bar (125psig) air supply pressure. Canadian Standards Association (CSA) configured pumps should not exceed 6.9 bar (100psig)...
Open the catalog to page 10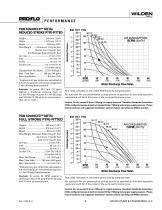
REDUCED STROKE PTFE-FITTED 'Displacement per stroke was calculated at 4.8 bar (70 psig) air inlet pressure against a 2 bar (30 psig) head pressure. against a discharge pressure head of 3.2 bar (47 psig) requires 4.1 bar (60 psig) Water Discharge Flow Rates Flow rates indicated on chart were determined by pumping water. For optimum life and performance, pumps should be specified so that daily operation -parameters will fall in the center of the pump performance curve. Caution: Do not exceed 8.6 bar (125psig) air supply pressure. Canadian Standards Association (CSA) configured pumps should...
Open the catalog to page 11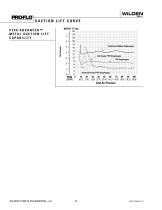
SUCTION LIFT CURVE METAL SUCTION LIFT Traditional Rubber Diaphragms WILDEN PUMP & ENGINEERING, LLC
Open the catalog to page 12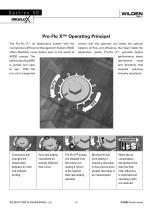
Pro-Flo XTM Operating Principal The Pro-Flo X™ air distribution system with the control dial, the operator can select the optimal revolutionary Efciency Management System (EMS) balance of ow and efciency that best meets the offers exibility never before seen in the world of application needs. Pro-Flo X™ provides higher performance, lower industry standards. $ Turning the dial changes the relationship between air inlet and exhaust porting. Each dial setting represents an entirely different ow curve WILDEN PUMP & ENGINEERING, LLC Pro-Flo X™ pumps are shipped from the factory on setting 4,...
Open the catalog to page 14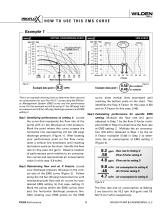
Example 1 SETTING 4 PERFORMANCE CURVE Example data point = Example data point = This is an example showing how to determine ow rate and air consumption for your Pro-Flo X™ pump using the Efciency Management System (EMS) curve and the performance curve. For this example we will be using 4.1 bar (60 psig) inlet air pressure and 2.8 bar (40 psig) discharge pressure and EMS setting 2. Figure 2 ow multiplier air multiplier curve, draw vertical lines downward until reaching the bottom scale on the chart. This identies the ow X Factor (in this case, 0.58) and air X Factor (in this case, 0.48)....
Open the catalog to page 15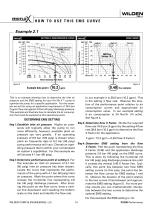
Example 2.1 SETTING 4 PERFORMANCE CURVE Example data point = This is an example showing how to determine the inlet air pressure and the EMS setting for your Pro-Flo X™ pump to optimize the pump for a specic application. For this example we will be using an application requirement of 18.9 lpm (5 gpm) ow rate against 2.8 bar (40 psig) discharge pressure. This example will illustrate how to calculate the air consumption that could be expected at this operational point. In our example it is 38.6 lpm (10.2 gpm). This is the setting 4 ow rate. Observe the location of the performance point...
Open the catalog to page 16All Wilden Pump catalogs and technical brochures
-
PX4 - 38 mm (1 1/2'') Metal Pump
32 Pages
-
Compact Pumps OEM Solutions
4 Pages
-
FAM-ORG-BRO
32 Pages
-
P800/PX800 Advanced? Series
55 Pages
-
P400/PX400
63 Pages
-
FAM-ADV-BRO
32 Pages
-
UNITEC™ Ultrapure™ pumps
2 Pages
-
UNITEC Brochure
8 Pages
-
Original™ Series METAL Pumps
35 Pages
-
HIGH PRESSURE PUMP SOLUTIONS
4 Pages
-
Peristaltic Pump
4 Pages
-
Mag-drive Pumps
2 Pages
-
TM1 & TM2
23 Pages
-
Drum Pump Kit
2 Pages
-
Sanifl o™ Series
27 Pages
-
Advanced™ Series PLASTIC Pumps
41 Pages
-
PX400 P L A S T I C
10 Pages
-
Chemical Transfer Pumps
2 Pages
-
Pro-Flo X™
2 Pages
-
Natural Gas Powered Pumps
2 Pages
-
ADVANCED BROCHURE
32 Pages