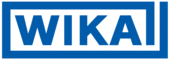

Catalog excerpts

Pressure Temperature Level Force Flow the iron and steel industry IwikaII ^ Part of your business
Open the catalog to page 1
Alexander Wiegand, Chairman and CEO, WIKA About us As a family-run business acting globally, with over 10,000 highly qualified employees, the WIKA group of companies is a worldwide leader in pressure and temperature measurement. The company also sets the standard in the measurement of level and flow, and in calibration technology. With manufacturing locations around the globe, WIKA ensures flexibility and the highest delivery performance. Every year, over 50 million quality products, both standard and customer-specific solutions, are delivered in batches of 1 to over 10,000 units. Founded...
Open the catalog to page 2
To increase productivity and product quality in primary metallurgy, WIKA supports you with a comprehensive portfolio of process instrumentation that enables flexible operation and complete process monitoring. Our robust and reliable measuring instruments have been developed on the basis of many years of application experience and can withstand even extreme process conditions. Customers trust our instrumentation solutions for measurements under high-pressure conditions up to 10,000 bar or at extreme process temperatures up to 2,000 °C, e.g. for the melting of metals or in applications with...
Open the catalog to page 3
Integrated steel works Steel is one of the most important materials for almost all sectors in civil engineering, in machine and tool building and through to precision engineering. Due to the harsh process conditions and the enormous demand for raw materials and energy, the optimisation of production processes is given high priority. The product quality and reproducibility of batches are of the utmost importance as they reduce the cost of the process. Iron and steel production processes require robust measurement technology that is capable of detecting faults reliably while keeping the...
Open the catalog to page 4
Integrated steel works Sinter plant Coke plant Pellet plant Blast furnace Direct reduced iron plant Basic oxygen furnace Electric arc furnace Ladle furnace Continuous casting plant Page 6 Page 8 Page 10 Page 12 Page 14 Page 16 Page 18 Page 20 Page 22
Open the catalog to page 5
Sinter plant Productivity and efficiency With sintering, a mixture of fine ores, coke, recycled process materials and other aggregates is prepared, through melting, for further use in the blast furnace to ensure gas permeability for the reducing gases. For the sintering process, the control of the sintering hood and its associated burner and the temperature in the furnace are crucial. A lost oven can result in complete process stop and fluctuating temperatures affect the quality of the product being produced. WIKA has a portfolio of high-performance measuring instruments that are tailored...
Open the catalog to page 6
Pressure Force Temperature Flow Level Calibration
Open the catalog to page 7
Coke plant Cost effectiveness and quality In the coke plant, the coal is converted to coke by heating the prepared coal mixture batch, in the absence of air, to a temperature of 1,000 to 1,300 °C for a period of 16 to 30 hours. In order to achieve optimal process conditions in coke plants, the furnace pressure and the furnace temperature in the individual furnaces are monitored individually. Coke, as a reducing agent, has a major impact on the cost-effectiveness of the process and the quality of the final product. In the coke plant, high-precision load cells ensure a controlled mixture of...
Open the catalog to page 8
Product recommendation Coke plant
Open the catalog to page 9
Pellet plant Productivity and efficiency Pellets are small balls of iron ore that are used in the production of steel. They are made with technology that utilises the powder that is produced during ore extraction. The process of granulation combines the blending of the raw material and a thermal treatment that burns the soft green pellets into hard balls. The raw material is rolled into a ball and then fired in a furnace or in a travelling grate to sinter the particles into a hard ball. WIKA offers durable and high-quality process instrumentation for the production of the highest-quality...
Open the catalog to page 10
Product recommendation Pellet plant
Open the catalog to page 11
Blast furnace High reliability for high availability During the blast furnace process, sinter or pellets, in addition to ore, coke and lime, serve to bind the unwanted constituents of the ore in the slag and also reduce the melting temperature of the iron. They are fed from above into the blast furnace, while hot compressed air is introduced from the tuyères in the lower part. Auxiliary reducing agents or fuels – such as coal, fuel oil, natural gas or other sources – can also be injected from the bottom of the furnace. The monitoring of fuel pressure and temperature, as well as the...
Open the catalog to page 12
Product recommendation Blast furnace
Open the catalog to page 13
Direct reduced iron plant Process safety Direct reduced iron (DRI), an alternative way of producing iron, has been developed to overcome the difficulties of conventional blast furnaces. DRI is successfully implemented in various parts of the world using natural gas or coal technology. On the one hand, the DRI process is very energy-efficient; on the other hand, further energy gains can be realised if the hot material is immediately transferred to an EAF melting operation (EAF = electric arc furnace). In this way, the heat from the direct reduced iron process reduces the cost of melting the...
Open the catalog to page 14
Product recommendation Direct reduced iron plant
Open the catalog to page 15
Basic oxygen furnace Ensuring the steel quality The pig iron produced in the blast furnace is used in the steel works in a liquid state where it is converted into crude steel in the converters. Here, the carbon contained in the pig iron is burnt by blowing in pure oxygen. iron, such as carbon, silicon, sulphur and phosphorus, are removed in the basic oxygen furnace (BOF) by blowing in oxygen. In doing this, temperatures of up to 1,700 °C are generated in the converter. An important trend in steel metallurgy is the rise in steel grades with increasing flexibility of metallurgical plants, in...
Open the catalog to page 16
Product recommendation Basic oxygen furnace
Open the catalog to page 17All WIKA Alexander Wiegand SE & Co. KG catalogs and technical brochures
-
FSD-3
4 Pages
-
Model CTH6200
7 Pages
-
Calibration and service centre
16 Pages
-
Standard product portfolio
116 Pages
-
Competence in flow measurement
16 Pages
-
Management Manual
24 Pages
-
Models 111.10, 111.12
5 Pages
-
Autoclavable instrumentation
2 Pages
-
Precise. Fast. Compact.
4 Pages
-
Nuclear power generation
24 Pages
-
Machine building
52 Pages
-
Heating technology
36 Pages
-
Power generation
24 Pages
-
Innovative SF6 solutions
36 Pages
-
WIKA image brochure
16 Pages
-
A-10
12 Pages
-
990.10
6 Pages
-
SC58
3 Pages
-
CS6H, CS6L, CS6S
8 Pages
-
CS4R
5 Pages
-
CPG500
6 Pages
-
CPG1500
11 Pages
-
PM 01.15
2 Pages
-
BWX
5 Pages
-
BA, BAX
5 Pages
-
A2G-40
3 Pages
-
Portable process calibrator
4 Pages
-
Sapphire-design thermocouple
4 Pages
-
Process transmitters
12 Pages
-
EPC Contractor Business
16 Pages
-
Water & Wastewater Technology
56 Pages
-
Thermische Solarenergie
20 Pages
-
Renewable Energies
24 Pages
-
Sanitary applications
44 Pages
-
Mobile working machines
24 Pages
-
Valve test benches
12 Pages
-
Handbook Calibration technology
73 Pages
-
Electronic Pressure Measurement
74 Pages