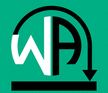

Catalog excerpts
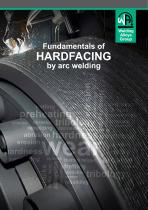
thermal fatigue cracks hardness hardness hardfacing buffer layer abrasion erosion tribology rebuilding corrosion abrasion buffer layer adhesion cracks thermal fatigue fretting cavitation abrasion
Open the catalog to page 1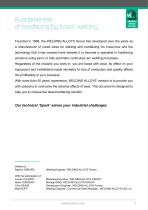
Fundamentals of hardfacing by fusion welding Founded in 1966, the WELDING ALLOYS Group has developed over the years as a manufacturer of cored wires for welding and hardfacing. Its know-how and the technology that it has created have allowed it to become a specialist in hardfacing solutions using semi- or fully automatic continuous arc welding processes. Regardless of the industry you work in, you are faced with wear. Its effect on your equipment and installations leads inevitably to loss of production and greatly affects the profitability of your business. With more than 50 years’...
Open the catalog to page 2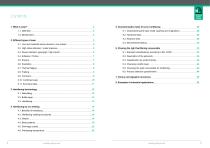
Contents 1. What is wear? 5. Characterisation tests for your hardfacing 2. Different types of wear 7. Various micrographic structures 8. Examples of industrial applications
Open the catalog to page 3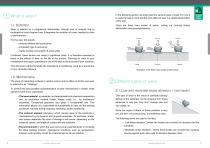
In the following section, we shall meet the various types of wear. For now it is useful to keep in mind that the main effect of wear is a visible deterioration of the part. There are three main modes of action: cutting (i.e. forming chips), deformation and gouging/chipping. Wear is defined as a progressive deterioration through loss of material due to prolonged or overly frequent use. It degrades the condition of a part, leading to a loss of performance. For the user, this entails: l i ncreased risks to personnel Pressure Speed reduced lifetime and productivity higher energy consumption &...
Open the catalog to page 4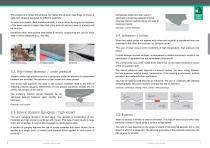
The sharper and harder the abrasive, the higher the abrasion rate. Page 30 shows a table with abrasive hardness for different materials. As there is no impact effect, substrate ductility is not an issue. As long as the hardness of the base material is higher than that of the external element, wear or abrasion will be very low. Hardfaced parts, heat treated steel plates & ceramic components are used to resist wear in these situations (e.g., 400 HB). Manganese steels are often used in applications involving repeated shocks, whereas titanium carbide alloys are ideal at resisting impacts....
Open the catalog to page 5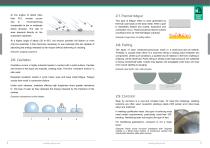
At low angles of attack (less than 30°), erosion occurs due to micromachining comparable to low or moderate stress abrasion. The rate of wear depends directly on the substrate's hardness. 2.7 Thermal fatigue This type of fatigue refers to wear generated by thermal cycle loads on the base metal. When a part is repeatedly heated and cooled, expansion and contraction occur. These processes lead to surface cracking known as “thermal fatigue cracking”. Example: Forge tools, hot rolling rollers. At a higher angle of attack (30 to 90°), the erosive particles will deform or even chip the substrate....
Open the catalog to page 6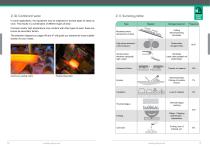
2.10. Combined wear In some applications, the equipment may be subjected to several types of stress at once. This results in a combination of different types of wear. Corrosion and/or high temperature may combine with other types of wear: these are known as secondary factors. The selection diagrams on pages 46 and 47 will guide you towards the most suitable solution for your needs. 2.11. Summary table Type Diagram Damage observed Frequency
Open the catalog to page 7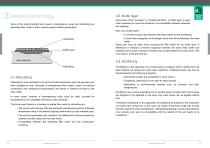
Some of the most important terms used in maintenance, repair and hardfacing are described here. Each of them requires special welding preparation. 3.2. Buffer layer Also known as the “sub-layer” or ’’metallic transition”, a “buffer layer” is used when necessary to overcome problems of incompatibility between substrate and cladding. Why use a buffer layer? • To provide a good base between the base metal and the hardfacing. • To avoid the propagation of shrinkage cracks from the hardfacing to the base metal. Great care must be taken when choosing the filler metal for the buffer layer....
Open the catalog to page 8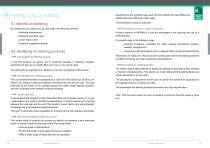
4.1. Benefits of hardfacing Depending on the protective gas used, the terms Metal Inert Gas (MIG) and Metal Active Gas (MAG) are often used. This procedure is easy to automate. By hardfacing your equipment, you will obtain the following benefits: • Reduced maintenance • Reduced operation costs • Lower repair costs • Extended equipment lifetime 4.2. Hardfacing arc welding processes ►►► Gas Tungsten Arc Welding process In the TIG process, an electric arc is produced between a refractory tungsten electrode and the part. A metallic filler wire may or may not be used. The weld pool is protected...
Open the catalog to page 9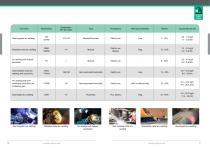
Weld pool protection Typical deposit rate Shielded metal arc welding Arc welding with tubular electrode Gas shielded metal arc welding with cored wire Arc welding with selfprotecting cored wire (no protective gas) With or without slag Flux baking Full name Shielded metal arc welding Arc welding with tubular electrodes Gas shielded metal arc welding Unshielded metal arc welding
Open the catalog to page 10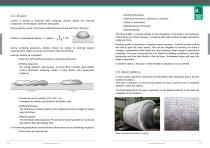
4.3. Dilution Control of dilution is essential when surfacing. Dilution affects the chemical composition of the deposit, hardness and quality. During welding, some of the base metal dissolves into the weld pool, diluting it. A B x 100 Dilution is calculated as follows: % dilution = A+B During surfacing operations, dilution should be limited to optimise deposit characteristics, whilst ensuring a good fusion with the substrate. How can dilution be controlled? l l S elect the right welding procedure, particularly heat input. W elding sequence: An overlap between weld passes, of about 50%,...
Open the catalog to page 11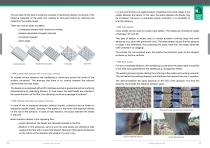
The principle of this type of surfacing consists of restricting relative movement of the abrasive materials on the parts and creating an anti-wear barrier by capturing the material in the hollow areas. There are various types of pattern: l Passes deposited at regular intervals. Cross/grid passes. Juxtaposed passes with continuous overlap. In a wet environment, an agglomeration of particles forms that lodges more readily between the beads. In this case, the space between the beads may be increased. However, to guarantee proper protection, it is advisable to limit this distance. Spot welds....
Open the catalog to page 12All Welding Alloys Group catalogs and technical brochures
-
WA Integra™
3 Pages
-
Welding Alloys Group
6 Pages
-
Joining
15 Pages
-
Hardfacing
15 Pages
-
Electrodes
9 Pages
-
Drill Guard
3 Pages