Catalog excerpts
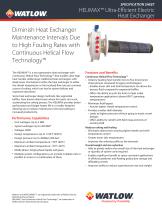
SPECIFICATION SHEET HELIMAX™ Ultra-Efficient Electric Heat Exchanger Diminish Heat Exchanger Maintenance Intervals Due to High Fouling Rates with Continuous Helical Flow Technology™ The HELIMAX™ is a next generation heat exchanger with Continuous Helical Flow Technology™ that enables ultra-high heat transfer unlike large, traditional heat exchangers with dead zones. Fluctuations within the heat exchanger to either the sheath temperature or the localized flow rate are common causes of coking, which can lead to system failures and expensive downtime. Some heat exchanger design methods, like segmental baffles, have known dead zones where hot spots can occur, accelerating the coking process. The HELIMAX provides better performance and longer heater life in a smaller footprint allowing you to reduce maintenance intervals leading to increased productivity. Performance Capabilities • Unit wattages: Up to 5 MW • • • • • • • * System wattages: Up to 200 MW* Voltages: 690V Design temperatures: Up to 1742°F (950°C) Design pressure: Up to 3000psi (206 bar) Maximum ambient temperature: 176°F (80°C) Maximum ambient temperature: -76°F (-60°C) Media phase: Single-phase liquids and gases Multiple system configurations can include multiple units in parallel, in series or a combination of these Watlow® and WATCONNECT® are registered trademarks of Watlow Electric Manufacturing Company HELIMAX™ and Continuous Helical Flow Technology™ are trademarks of Watlow Electric Manufacturing Company. Features and Benefits Continuous Helical Flow Technology™ • Industry-leading heat transfer (two to five times factor improvement compared to legacy technologies) • Enables lower skin and shell temperature rise above the process fluid compared to segmental baffles • Offers the ability to push the limit on high outlet temperature applications (above 600°C operating temperatures) • Minimizes fluid bypass • Assures tighter sheath temperature control • Provides smaller shell diameter • Leads to higher pressures without going to exotic vessel designs • Offers ability for retrofit with field measurements of existing shell Reduces coking and fouling • Eliminates dead zones assuring tighter sheath and shell temperature control • Creates lower skin temperatures • Improves the velocity profile on the elements Overall weight and size reduction • Able to greatly reduce the overall size of the heat exchanger or quantity of system units required • Enables significant benefit to space constraint applications in offshore platforms and floating production storage and offloading vesse
Open the catalog to page 1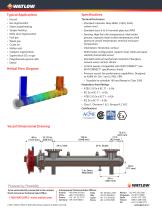
Typical Applications Terminal Enclosures Hot oil Gas regeneration Steam superheating Syngas heating Mole sieve regeneration Fuel gas Waste gas Crude oil Molten salt Catalytic regeneration Supercritical CO2 or gas Polypheonols-generic add Diesel • Standard materials: Alloy 800H, 316SS, 304H, carbon steel • Standard sizes: 8 to 24 nominal pipe size (NPS) • Sensing: High limit skin temperature, inlet/outlet process, exposed metal surface temperature, shell (pressure vessel) temperature, terminal enclosure temperature • Orientation: Horizontal, vertical • Multi-heater configuration support:...
Open the catalog to page 2All Watlow Electric Manufacturing Company catalogs and technical brochures
-
Flexible Heaters
12 Pages
-
FIREROD® Cartridge Heaters
12 Pages
-
OPTIMAX
3 Pages
-
POWERSAFE
2 Pages
-
2704
8 Pages
-
2704MP
4 Pages
-
2704CP
4 Pages
-
6100A & 6180A
8 Pages
-
6000 Series graphic recorder
4 Pages
-
Eurotherm® EPower™
22 Pages
-
w OPTIMAX® Heat Exchanger
2 Pages
-
SEMICONDUCTOR
18 Pages
-
Operator Interfaces
12 Pages
-
Indicators
6 Pages
-
Power Switching Devices
40 Pages
-
Data Loggers
16 Pages
-
Control Panels
6 Pages
-
Immersion Heaters
154 Pages
-
Tubular Heaters
52 Pages
-
Specialty Heaters
22 Pages
-
Radiant Heaters
10 Pages
-
High-Temperature Heaters
34 Pages
-
Nozzle Heaters
4 Pages
-
Fluid Delivery Heaters
8 Pages
-
Circulation Heaters
70 Pages
-
Flexible Heaters
36 Pages
-
Thermostats and Accessories
12 Pages
-
Air Heaters
34 Pages
-
DATA LOGGER with
8 Pages
-
PROCESS CONTROLLER
8 Pages
-
ASPYRE
8 Pages
-
FIREROD ® Cartridge Heaters
418 Pages
-
Heaters from Watlow
576 Pages
-
Energy Process
9 Pages
-
Sensor and Controller
418 Pages
-
serv-rite wire
8 Pages
-
SEMICONDUCTOR PROCESSING
34 Pages
-
SCR power controllers
6 Pages
-
multicell heaters
8 Pages
-
flexible heater
12 Pages
-
fiberbar flat tubular heater
8 Pages
-
thermal solutions
8 Pages
-
engine heater and systems
4 Pages
-
dinamite power controllers
20 Pages
Archived catalogs
-
Piccolo™ P304i
4 Pages
-
Thermocouple Designs
2 Pages
-
Heat Solutions Resource
24 Pages
-
Application Guide
411 Pages
-
Application Guide catalog
216 Pages
-
Plastics catalog
411 Pages