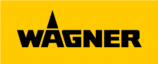

Catalog excerpts
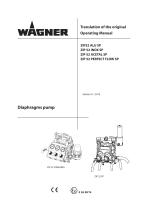
Translation of the original Operating Manual ZIP52 ALU SP ZIP 52 INOX SP ZIP 52 ACETAL SP ZIP 52 PERFECT FLOW SP Diaphragms pump
Open the catalog to page 1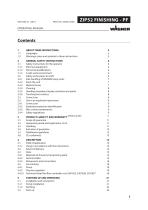
OPERATING MANUAL ABOUT THESE INSTRUCTIONS Languages Warnings, notes and symbols in these instructions GENERAL SAFETY INSTRUCTIONS Safety instructions for the operator Electrical equipment Personnel qualifications A safe work environment Safety instructions for staff Safe handling of WAGNER spray units Earth the unit Material hoses Cleaning Handling hazardous liquids, varnishes and paints Touching hot surfaces Correct use Use in an explosion hazard area Correct use Explosion protection identification Max. surface temperature Safety regulations PRODUCT LIABILITY AND WARRANTY Scope of guarantee...
Open the catalog to page 3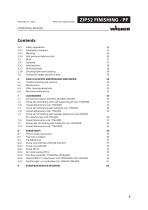
OPERATING MANUAL Safety regulations Emergency stopping Washing Unit pressure tightness test Work Spraying Painting hints Working breaks Shutting down and cleaning Storing for longer periods of time FAULT LOCATION, MAINTENANCE AND REPAIR Trouble shooting and solution Maintenance Filter cleaning operations Machine maintenance ACCESSORIES Accessories only for 2301832, 2301836, 2301837 Pump zip 52 finishing with wall supporting kit cod. T760.00M Overall dimensions cod. T760.00M Pump zip 52 finishing with stand kit cod. T760.00S Overall dimensions cod. T760.00S Pump zip 52 finishing with...
Open the catalog to page 4
OPERATING MANUAL ABOUT THESE INSTRUCTIONS WARNINGS, NOTES AND SYMBOLS IN THESE INSTRUCTIONS
Open the catalog to page 5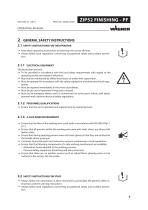
OPERATING MANUAL GENERAL SAFETY INSTRUCTIONS SAFETY INSTRUCTIONS FOR THE OPERATOR ELECTRICAL EQUIPMENT PERSONNEL QUALIFICATIONS A SAFE WORK ENVIRONMENT Ensure that the floor of the working area is anti-static in accordance with EN 50053 Part 1 §7-2. Ensure that all persons within the working area wear anti-static shoes, e.g. shoes with leather soles. Ensure that during spraying, persons wear anti-static gloves so that they are earthed via the handle of the spray gun. Customer to provide paint mist extraction systems conforming to local regulations. Ensure that the following components of a...
Open the catalog to page 6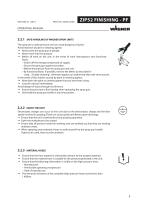
OPERATING MANUAL SAFE HANDLING OF WAGNER SPRAY UNITS The spray jet is under pressure and can cause dangerous injuries. Avoid injection of paint or cleaning agents: Never point the spray gun at people. Never reach into the spray jet. Before all work on the unit, in the event of work interruptions and functional faults: – Switch off the energy/compressed air supply – Secure the spray gun against actuation. – Relieve the pressure from the spray gun and unit. – By functional faults: If possible, remove the defect as described in chap. „Trouble shooting“, otherwise apply to an authorised...
Open the catalog to page 7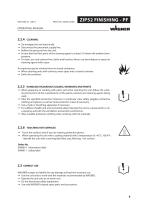
OPERATING MANUAL HANDLING HAZARDOUS LIQUIDS, VARNISHES AND PAINTS
Open the catalog to page 8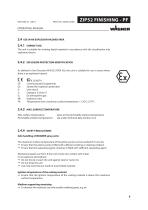
OPERATING MANUAL USE IN AN EXPLOSION HAZARD AREA EXPLOSION PROTECTION IDENTIFICATION As defined in the Directive 94/9/CE (ATEX 95), the unit is suitable for use in areas where there is an explosion hazard. II 2G IIB T4 Communautés Européennes Symbol for explosion protection Unit class II Category 2 (Zone 1) Ex-atmosphere gas Explosion class Temperature class: maximum surface temperature < 135°C; 275°F. Max. surface temperature: Permissible ambient temperature: same as the permissible material temperature see under Technical data, Section 4.3.2 SAFETY REGULATIONS
Open the catalog to page 9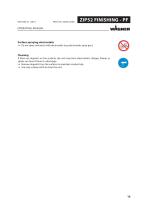
OPERATING MANUAL
Open the catalog to page 10
OPERATING MANUAL PRODUCT LIABILITY AND WARRANTY (STATUS 01.02.2009) All Wagner professional colour application devices (hereafter referred to as products) are carefully inspected, tested and are subject to strict checks under Wagner quality assurance. Wagner exclusively issues extended guarantees to commercial or professional users (hereafter referred to as “customer”) who have purchased the product in an authorised specialist shop, and which relate to the products listed for that customer on the Internet under www.wagner-group.com/profi-guarantee. The buyer’s claim for liability for defects...
Open the catalog to page 11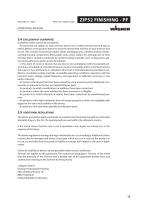
OPERATING MANUAL 3.4 EXCLUSION OF GUARANTEE Guarantee claims cannot be considered - for parts that are subject to wear and tear due to use or other natural wear and tear, as well as defects in the product that are a result of natural wear and tear, or wear and tear due to use. This includes in particular cables, valves, packaging, jets, cylinders, pistons, meanscarrying housing components, filters, pipes, seals, rotors, stators, etc. Damage due to wear and tear that is caused in particular by sanded coating materials, such as dispersions, plaster, putty, adhesives, glazes, quartz foundation....
Open the catalog to page 12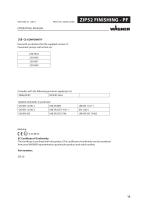
OPERATING MANUAL Herewith we declare that the supplied version of: Pneumatic pumps with article no. 2301832 2301836 2301837 2301838 Complies with the following provisons applying to it: 2006/42/EC Applied standards, in particular: UNI EN 12100-1
Open the catalog to page 13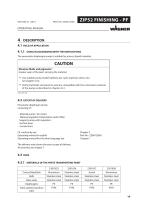
OPERATING MANUAL USING IN ACCORDANCE WITH THE INSTRUCTIONS The pneumatic diaphragm pump is suitable for process liquid materials. CAUTION Abrasive fluids and pigments ! Greater wear of the parts carrying the material. Use suitable pump model (delivery per cycle, material, valves, etc.) see chapter 4.3.2. Verify that fluids and solvents used are compatible with the constrution material of the pump as described in chapter 4.3.1. SIHC_0067_GB Pneumatic diaphragm pump consisting of: - Material pump / Air motor Material regulator/Antipulsator and/or filter Support pump with regulators Suction...
Open the catalog to page 14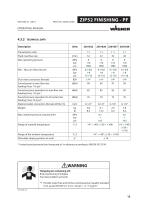
OPERATING MANUAL TECHNICAL DATA Transmission ratio Ø air inlet connection (female) Sound power at max. flow rate feeding 8 bar; 116 psi *. Sound pressure equivalent to max.flow rate feeding 8 bar; 116 psi *. Sound pressure equivalent to 50 cycles/min feeding 5 bar; 72,5 psi*. Material outlet connection (female) (M16x1,5) Weight Max. material pressure at pump inlet Range of material temperature Range of the ambient temperature Allowable sloping position at work * A rated sound pressure level measured at 1m distan
Open the catalog to page 15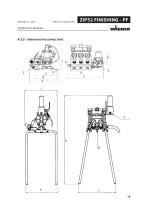
OPERATING MANUAL
Open the catalog to page 16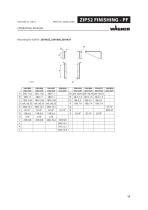
OPERATING MANUAL
Open the catalog to page 17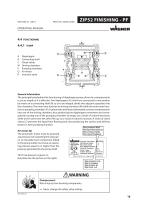
OPERATING MANUAL Diaphragms Connecting shaft Check valves Driving chambers Pumping chambers Air motor Inversion valve General information The principle lying behind the functioning of diaphragm pumps driven by compressed air is just as simple as it is effective. Two diaphragms (A), which are connected to one another by means of a connecting shaft (B) so as to be integral, divide two adjacent capacities into four chambers. The inner ones function as driving chambers (M) while the outer ones function as pumping, chambers (P). A pneumatic distributor alternately conveys compressed air into one...
Open the catalog to page 18All WAGNER catalogs and technical brochures
-
Brochure PEM-X1 CG
4 Pages
-
Brochure Manual application
3 Pages
-
Corona and Tribo Guns
10 Pages
-
Brochure Cobra
4 Pages
-
Press release IceBreaker
3 Pages
-
STATIONARY Wood- & Metalworking
11 Pages
-
Manual powder coating
3 Pages
-
PXS Powder Centers
2 Pages
-
TOPFINISH DD10
2 Pages
-
FENCE & DECKING SPRAYER
36 Pages
-
C-Line
6 Pages
-
WOOD- & METALWORKING
12 Pages
-
Unica AME
4 Pages
-
Flyer EvoMotion-Revers AME
2 Pages
-
WAG Datenblatt DD10 GER
2 Pages
-
BROSCHÜRE COBRA AME
8 Pages
-
DD10
2 Pages
-
Control Pro 350 R
144 Pages
-
Control Pro 350 M
144 Pages
-
Control Pro 250 M
140 Pages
-
W 990 FLEXiO
122 Pages
-
W 950 FLEXiO
130 Pages
-
FineCoat 9900
6 Pages
-
FineCoat 9900 PowerCart
52 Pages
-
FinishControl 5000
132 Pages
-
FinishControl 3500
132 Pages
-
Basic Booth Systems
2 Pages
-
SuperCube
4 Pages
-
Prima Cube
4 Pages
-
ID-Booth System LV
4 Pages
-
Profi Tech M
8 Pages
-
Profi Tech S
6 Pages
-
Prima Tech CCM
4 Pages
-
Facades and interior walls
12 Pages
-
SuperFinish
5 Pages
-
Finish Control 5000
2 Pages
-
PROTEC GM
2 Pages
-
WOOD & METAL APPLICATIONS
7 Pages
-
BO AIRSPRAY-MANUAL AME
8 Pages
-
BO GM 4000AC AME WEB
8 Pages
-
BO AIRSPRAY-AUTOMATIC AME
2 Pages
-
SuperFinish SF 27
8 Pages
-
Finish 270
6 Pages
-
EPG_SL_5
2 Pages
-
TempSpray
6 Pages
-
PS 3.21 Spraypack
8 Pages
-
Finish 230 Lacquer Spraypack
2 Pages
-
PrimaTechCCM
4 Pages
-
profitech S
6 Pages
-
PrimaCube automatic system
4 Pages
-
BO Modular Painting System
4 Pages
-
SuperTech
4 Pages
-
ProfiTech
2 Pages
-
VertiCube
1 Pages
-
C4 HiCoat
4 Pages
-
PrimaTech Control Technology
4 Pages
-
Wagner Comfort Powder Centre
1 Pages
-
The C4 generation of guns
6 Pages
-
Inline pump IP5000
2 Pages
-
EPG-DP 5 Multi Control
2 Pages
-
DigiTech
2 Pages
-
Wagner 3D Pro Coating
1 Pages
-
Unica 4-270
4 Pages
-
TwinControl
8 Pages
-
SupraCoat
4 Pages
-
RoboCoat
2 Pages
-
IceBreaker®
8 Pages
-
WAGNER Thermo-technology
2 Pages
-
The WAGNER Thermo-System
2 Pages
-
GA 3000 AC
4 Pages
-
Evobell
4 Pages
-
Electrostatic guns
8 Pages
-
AirCoat guns
4 Pages
Archived catalogs
-
Cobra® 40-10
8 Pages
-
SuperCube_en
4 Pages
-
C4_brochure
4 Pages