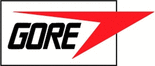

Catalog excerpts
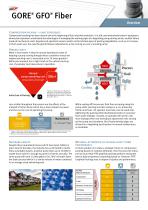
GORE® GFO® Fiber Compression packing - plant experience Compression packing has been around since the beginning of the industrial revolution. It is still used extensively today in equipment where plant operators understand the advantages of managing the warning signs of a degrading pump packing versus sudden failure mode of mechanical seals. Experienced operators know to watch out for tell-tale signs of packing degradation, such as an increase in flush water use, the need for gland follower adjustments, a hot running or even a smoking pump. Hidden costs What is less known is that the annual operational costs of keeping a pump running through these conditions versus the original packing cost is estimated to be 30 times greater!! While procurement has a tight hold on the upfront packing cost, the greater cost takes place in operation. Annual pump operating cost (impacted by Packing)* Less visible throughout the process are the effects of the material’s friction factor which has a direct impact on power and thus on the cost of operating the pump. ** Based on FSA Article “Sealing Systems Matter - Choosing Mechanical Seals to Optimize Life Cycle Cost, Safety, and Environmental” & McKinsey Quarterly March 2013 “Measuring the real cost of water”. *** Based on over 300 documented case histories. Avoidable waste Despite these operational losses which have been hidden in plain view for decades, the industry has so far failed to tackle these avoidable wastes. A typical pump loses up to 39,000 kilowatt-hours which is enough to power 10 homes annually. The same pump will send 15,000 gallons (56.78m3) of water down the drain per year which is a similar volume of water contained in an average sized swimming pool. While sealing off the process fluid from escaping along the pump shaft, packing acts like a brake in a car, producing friction and heat. An operator must take care to avoid overtightening the packing while disallowing media or excessive flush water leakage. Usually, an operator will opt for a bit more leakage when one more gland adjustment risks seizing up the pump and shutdown. But if early warning signs are missed on a degrading packing then increased maintenance is inevitable. Material attributes of packing affect pump performance A smart solution is to make a strategic choice in compression packing based on material attributes. Over the years the industry has found that PTFE graphite packings perform among the best at balancing these competing dynamics. However, PTFE Graphite Packings vary in degree of quality and performance. Thermal Conductivity
Open the catalog to page 1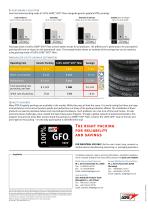
A SUSTAiNABLE SOLUTiON Gore has tested packing made of 100% GORE® GFO® Fiber alongside generic graphite/PTFE packings. Sealability Up to 11x more ”tight‘ Creep resistance Up to 7x more creep resistant Packings made of 100% GORE® GFO® Fiber achieve better results for all attributes. The differences in performance for each generic packing will have an impact on the operational costs. The example below shows an estimate of the savings that can be made by using packing made of 100% GORE® GFO® Fiber. Based on calculations for a 100 psi (6.9 bar) pump, 2 inch (50 mm) shaft; Drip rate 25,000...
Open the catalog to page 2All W. L. Gore & Associates catalogs and technical brochures
-
GORETM Magnet Wires
4 Pages
-
GORE ® Turbine Filters
4 Pages
-
ePTFE Fiber
2 Pages
-
Tubular Back-Pulse Filters
4 Pages
-
GORE PTFE Fiber Solutions
2 Pages
-
Gore STA-PURE Pump Tubing
2 Pages
-
high speed data cables
42 Pages
-
MEDICAL OEM PRODUCTS
4 Pages
-
Automotive Vents
8 Pages
-
GORE™ Ethernet High Flex
1 Pages
Archived catalogs
-
GORE™High Voltage Wire
4 Pages