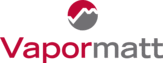
Catalog excerpts

Phosmatt - Phosphating Process The Phosmatt Process will apply the phosphate coating to previously dirty, greasy, scaled and corroded surfaces, removing the contaminants and starting the phosphate layer, all in one process. Even painted surfaces can be stripped and re-phosphated without added complications. The Phosmatt process time required, including all surface preparation is half that necessary for the conventional phosphate stage alone in a normal dip method. (Excluding up to five extra pre-phosphating stages for de-rusting, de-greasing and rinsing, which are necessary with conventional methods).
Open the catalog to page 1
The Phosmatt Process is simple in principle. It uses a normal closed-circuit wet blast technique, as perfected by Vapormatt Engineers over many years, to simultaneously etch, de-grease, de-rust and de-scale the surface - leaving a very clean, chemically active surface which is totally unprotected from its surroundings. The Phosmatt Process uses a heated phosphate solution as the carrier for the blast media: chemical action immediately starts with the phosphate when the virgin, unprotected metal surface is exposed. Small, fast growing crystals result. To continue the crystal growth, without...
Open the catalog to page 2
The Phosmatt Process produces many close packed crystals which adhere directly onto the metal substrate. This gives a far more corrosion and shock resistant coating than the larger, less well adhered crystals which are formed using traditional processes. Typical Applications Of The Phosmatt Process 1. Removal of old paint and substrates from ordnance and engineering components, then re-phosphating. 4. Cleaning and phosphating of transmission components and sliding engineering parts, to provide or assist lubrication. 2. De-scaling of metal billets, wire, rod, tube then phosphating prior to...
Open the catalog to page 3
VAPORMATT REPORT - An Alternative Phosphating System The Phosphating of steel surfaces has long been recognised as an excellent pre-treatment for painting, coating, or bonding. The chemical interchanges are fully understood and the materials available are sophisticated, easy to use, and their sales are backed-up by high standards of expertise and technical support. However, the methods of applying the chemicals have changed little over the last 50 years, so that for most companies, this still means that a long series of immersion or spray operations are necessary to clean, degrease, etch,...
Open the catalog to page 4
Coatings are applied very quickly - often in seconds. The rapid build-up and violent agitation produces a fine-textured, very dense coating, giving excellent bond strength and highly effective "creep" protection. LIMITATIONS No process caters for every possibility and although Phosmatt is adaptable and versatile, it has its' weaknesses. Difficulty can be experienced if complex components are involved, since abrasive grits can be trapped in fine holes - particularly threads or blind holes. Finally, when heavy primary scale is present, the system may prove to be too slow and the build-up of...
Open the catalog to page 5
Filtration is an important feature of Phosmatt equipment and use is made of a wide range of techniques. A free-standing filtration tank is used to provide the control and management of the chemical balance. Slurry from the blast / phosphate station passes through a centrifugal separator which removes the blast media (grit). The liquids pass on to the filter tank where re-heating takes place and where sensors detect and indicate the need for fresh chemicals. These are injected by a metering system so that the correct balance is always maintained. Phosmatt filtration and chemical re-heating...
Open the catalog to page 6All Vapormatt catalogs and technical brochures
-
Decomatt
4 Pages
-
Sabre
2 Pages
-
Cougar Radial
2 Pages
-
Manual Wet Blast Machines
8 Pages