

Catalog excerpts
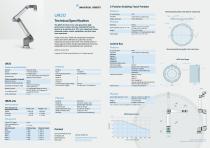
3-Position Enabling Teach Pendant Features Technical Specification Display resolution The UR20, the first of our next-generation high performance cobots, has been redesigned from the ground up to provide up to 30% more speed and torque, advanced motion control capabilities, and first-class user experience. Materials Teach pendant size (W x H x D) Weight Cable length Operating temperature range Safety functions In compliance with Joint architecture 750 W 300 W Ambient temperature: 0-50˚C (32-122˚F) 17 configurable safety functions EN ISO 13849-1 (PLd Category 3) and EN ISO 10218-1 2-1-3 Digital Out Analog In Tool I/O power supply voltage Tool I/O power supply Hardware interfaces Power Source Performance Force sensing, tool flange/torque sensor Range Precision Accuracy Physical Control Box Size (W x H x D) Power consumption (average) Maximum power Moderate operating settings 16 16 2 2 4 24V, 2A Modbus TCP (Client/Server) Ethernet/IP Adapter PROFINET device/PROFIsafe ROS/ROS2 Ethernet 1 Gb/s USB 2.0 USB 3.0 Mini DisplayPort Injection Moulding Machine Interface (SPI AN-146 & Euromap-67) 115/230 VAC, 60/50 Hz IP rating Noise Arm mounting direction I/O Ports Digital In Recommended hole pattern for robot base IP classification Humidity I/O Ports Digital In Digital Out Analog In Analog Out Quadrature digital inputs I/O Power Supply Industrial protocols Copyright © 2024 by Universal Robots A/S. All rights reserved. 20 kg (44,1 lbs) 1750 mm (68,9 in) 6 rotating joints 12 inch touchscreen with PolyScope graphical user interface Plastic 300 mm x 231 mm x 50 mm (11,8 in x 9,1 in x 1,97 in) 1,8 kg (3.961 lbs) including 1 m of teach pendant cable 4,5 m (177,17 in/14,77 ft) Payload Reach Degrees of freedom Today, more than 75,000 UR collaborative industrial robots have been delivered to customers across industries and around the world. The newest series of heavy payload cobots brings unparalleled performance, adaptability and an unparalleled user experience. General specification Mounting hole pattern with pins for robot base Footprint Materials Tool flange Connector type Cable length (robot arm) Weight including cable Humidity Weight Materials Ø 245 mm Aluminum, plastic, steel EN ISO-9409-1-80-6-M8 M8 8-pin female 6 m (236 in/19.68 ft) 64 kg (141,1 lbs) ≤ 90% RH (non-condensing) 460 mm x 449 mm x 254 mm (18,2 in x 17,6 in x 10 in) 12 kg (26,5 lbs) Powder coated steel The control box is also available in an OEM version Contact Universal Robots A/S Energivej 25 5260 Odense Denmark Typical TCP speed Pose repeatability per ISO 9283 Axis movement Base Shoulder Elbow Wrist 1 Wrist 2 Wrist 3 Center of gravity offset (mm) 800 UNLESS OTHERWISE SPECIFIED: Dimensions are
Open the catalog to page 1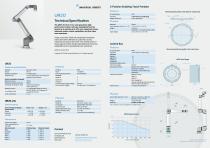
3-Position Enabling Teach Pendant Features In comliance with Joint architecture Power Source Physical Control Box Size (W x H x D) UR20 arm Force sensing tool flange/ torque sensor Range Precision Accuracy Digital Out Analog In Tool I/O power supply voltage Tool I/O power supply Hardware interfaces Safety functions 750 W 300 W Ambient temperature: 0-50˚C (32-122˚F) 17 configurable safety functions EN ISO 13849-1 (PLd Category 3) and EN ISO 10218-1 2-1-3 16 16 2 2 4 24V, 2A Modbus TCP (Client/Server) Ethernet/IP Adapter PROFINET device/PROFIsafe ROS/ROS2 Ethernet 1 Gb/s USB 2.0 USB 3.0 Mini...
Open the catalog to page 2All Universal Robots A/S catalogs and technical brochures
-
Universal Robots User Manual
373 Pages
-
UR3e
1 Pages
-
UR5e
1 Pages
-
UR30
1 Pages