
Catalog excerpts
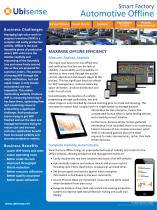
Automotive Offline Virtual Station Operations Centre Smart Device Process Improvement Business Challenges Managing high‐value work‐in‐ progress inventory (WIP) is a complex and costly production activity. Offline is the post‐ Assembly phase of production where WIP units leave the relative captivity and sequencing of the Assembly Line and move freely around site as they are prepared for customer orders. The process of moving WIP through the major verification, test and repair stages is only loosely constrained and non‐ sequential. This makes maintaining visibility of where WIP is, measuring how long it has been there, optimising flow and maximising resource productivity a significant challenge. Both production teams trying to get WIP finished and out the door and management teams trying to reduce cost and increase customer satisfaction benefit from increased visibility and accurate production metrics. MAXIMISE OFFLINE EFFICIENCY Measure, Analyse, Improve The major cost factors for any Offline test and verification function are the lack of visibility, measurability and traceability of vehicles as they move through the quality control, adjustment and rework stages of the process. This has significant knock‐on effects for WIP management, resource balancing, space utilisation, product distribution and order‐to‐cash cycle. Conventionally, the location of a vehicle progressing through verification, test and repair stages is only recorded by manual scanning prior to a task commencing. This very sparse location data, coupled with no single system to manage location information for the enterprise, means that considerable human effort is spent finding vehicles and recording current location. Furthermore, because all the human‐gathered information is not recorded, there is no continuous historic measure of any complex processes, which leads to educated guesses about the steps required to make improvements, rather than data‐ driven decisions. Business Benefits Lower WIP levels and costs Smart Factory Offline brings an unprecedented level of visibility and control to the Offline process, allowing production and management teams to: Lower operating costs Better order‐to‐cash Improved throughput Waste reduction Better resource utilisation Better quality assurance Better space utilisation including cycle times, dwell times, occupancies and lead times Set process goals and metrics against which exception information is distributed to the user community Ensure Process Steps are monitored, measured and alerts raised when deviations from plan occur Integrate location‐driven WIP status back into existing production systems to improve operational decision making and audit trail fidelity
Open the catalog to page 1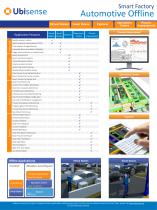
Smart Factory Automotive Offline Application Features Identify vehicle in station Signal to external system/device TCP/IP Track location of tagged devices Automatic device to product verification | Trigger external devices on spatial events Search by Vehicle property Vehicle Movement History Vehicle Location Certainty Optimal Placement Filtering Standard Representation Library Show Process Areas (Active/Inactive) Search Product by Process Function Search Product by Named Area Dwell Time Monitoring Vehicle Time in Offline Monitoring Area Over-occupancy Monitoring Prohibited Zone Monitoring...
Open the catalog to page 2All Ubisense catalogs and technical brochures
-
Series 7000 Industrial Tag
2 Pages
-
myWorld inside - telecoms
2 Pages
-
myWorld - telecoms
2 Pages
-
IT Requirements
1 Pages
-
Virtual Station
1 Pages
-
Operations Centre
2 Pages
-
Process Improvement
2 Pages
-
Explorer
1 Pages
-
Korean?certified IP Sensors
2 Pages
-
RTLS Hardware
2 Pages
-
Research Package
2 Pages