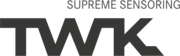
Catalog excerpts
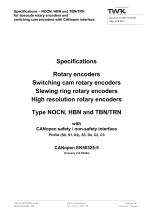
SUPREME SENSORING TWK Document no: NOC 13100 UE Date: 12.06.2019 Specifications - NOCN, HBN and TBN/TRN for absolute rotary encoders and switching cam encoders with CANopen interface Specifications Rotary encoders Switching cam rotary encoders Slewing ring rotary encoders High resolution rotary encoders Type NOCN, HBN and TBN/TRN with CANopen safety / non-safety interface Profile (S0, S1, S2), S3, S4, C2, C3 CANopen EN50325-5 (Formerly CiA DS304) TWK-ELEKTRONIK GmbH BismarckstraBe 108 info@twk.de visit us at | twk.de
Open the catalog to page 1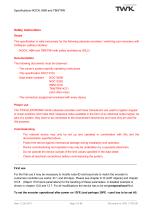
Specifications NOCN, HBN and TBN/TRN Safety instructions Scope This specification is valid exclusively for the following absolute encoders / switching cam encoders with CANopen (safety) interface: - NOCN, HBN and TBN/TRN with safety architecture (SIL2) Documentation The following documents must be observed: - The owner's system-specific operating instructions - This specification NOC13100 - Data sheet numbers NOC13099 NOC13292 HBN13218 TBN/TRN14271 (and other ones) - The connection assignment enclosed with every device Proper use The TWK-ELEKTRONIK GmbH absolute encoders and linear...
Open the catalog to page 2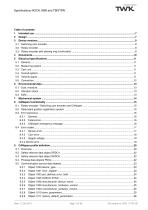
Specifications NOCN, HBN and TBN/TRN Date: 12.06.2019 Page 3 of 86 Document no. NOC 13100 UE
Open the catalog to page 3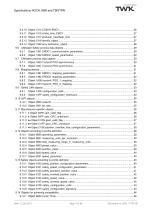
Specifications NOCN, HBN and TBN/TRN Date: 12.06.2019 Page 4 of 86 Document no. NOC 13100 UE
Open the catalog to page 4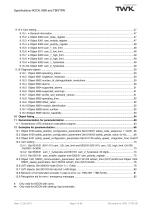
Specifications NOCN, HBN and TBN/TRN Only valid for NOCN with cams. Only valid for NOCN with slewing ring functionality
Open the catalog to page 5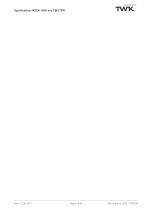
Date: 12.06.2019 Page 6 of 86 Document no. NOC 13100 UE
Open the catalog to page 6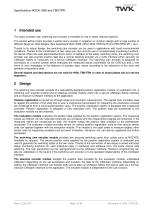
Specifications NOCN, HBN and TBN/TRN 1 Intended use The rotary encoder resp. switching cam encoder is intended for use in safety-relevant systems. The version without cams provides a safety rotary encoder in singleturn or multiturn design with a huge number of different flange an shaft designs (See datasheets NOC13099, NOC13292, HBN13218 and TBN/TRN14271, etc.). Thanks to its robust design, the switching cam encoder can be used in applications with harsh environmental conditions. Thanks to the combination of two relays per cam and the use of corresponding monitoring functions, the device...
Open the catalog to page 7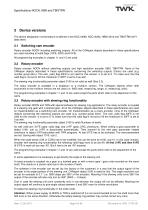
Specifications NOCN, HBN and TBN/TRN 3 Device versions The device designation nomenclature is defined in the NOC13099, NOC13292, HBN13218 and TBN/TRN14271 data sheet. Rotary encoder NOCN including switching outputs. All of the CANopen objects described in these specifications are used including all valid flags (13FE, 30FE and 61FE). All programming examples in chapter 11 and 12 are used. Rotary encoder Rotary encoder NOCN without switching outputs and high resolution encoder HBN, TBN/TRN. None of the CANopen objects described in these specifications concerning the switching outputs (Cams)...
Open the catalog to page 8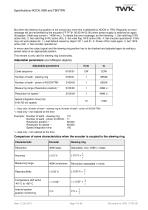
Specifications NOCN, HBN and TBN/TRN But when the slewing ring position is not correct any more this is detected by NOCN or TRN. Regularily an error message will be transmitted by the encoder (FF FF 81 00 80 04 02 00) when power supply is switched on again (Exception: Shaft was turned n * 4096 rev.). To delete this error message, do the following: 1. Set valid flag 31FE active (A5). 2. Set valid flag 61FE active (A5). 3. Set valid flag 13FE active (A5). 4. Set encoder operational. If this may not work please do: 1. Load default values by object 1011, sub 01.2. Power off/on reset again. 3....
Open the catalog to page 9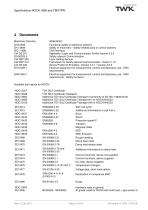
Specifications NOCN, HBN and TBN/TRN SUPREME SENSORING 4 Documents Machinery Directive 2006/42/EC Functional safety of electronic systems Safety of machinery - Safety-related parts of control systems CAN Interface. Application Layer and Communication Profile Version 4.2.0 Safety-relevant Communication. Layer Setting Service. Framework for Safety-relevant Communication Version 1.01. Device Profile for Encoders, Version 4.0.1 / Version 4.0.2 Electrical equipment for measurement, control and laboratory use - EMC requirements Electrical equipment for measurement, control and laboratory use -...
Open the catalog to page 10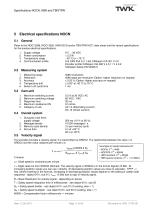
Specifications NOCN, HBN and TBN/TRN SUPREME SENSORING 5 Electrical specifications NOCN 5.1 General Refer to the NOC13099, NOC13292, HBN13218 and/or TBN/TRN14271 data sheet and the variant specifications for the precise electrical specifications. 1. Supply voltage 2. Power consumption 3. Temperature range 4. Communication profile 5.2 Measuring system 1. Measuring range 2. Resolution 3. Accuracy 4. Temperature drift 5. Sensor unit cycle time 9 V ... 36 VDC < 2.5 W - 40° C to + 70° C Full CAN Part A (11-bit) CANopen CiA 301 V 4.2 Encoder profile CANopen CiA 406 V 4.0.1 / V 4.0.2 CANopen...
Open the catalog to page 11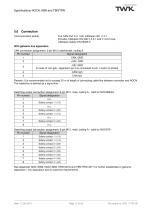
Specifications NOCN, HBN and TBN/TRN Communication profile Full CAN Part A (11-bit) CANopen 301 V 4.1 Encoder CANopen DS 406 V 4.0.1 and V 4.0.2 resp. CANopen Safety EN 50325-5 With galvanic bus separation CAN connection assignment: 5-pin M12 male/female, coding A See datasheet NOC13099, NOC13292, HBN13218 and TBN/TRN14271 for further possibilities of galvanic separation / non separation due to customer requirements. Date: 12.06.2019 Page 12 of 86 Document no. NOC 13100 UE
Open the catalog to page 12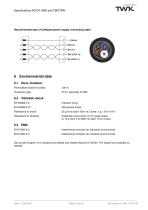
Specifications NOCN, HBN and TBN/TRN SUPREME SENSORING Recommended type of CANopen/power supply connecting cable: 6 Environmental data 6.1 Dust, moisture Permissible relative humidity Protection type: 6.2 Vibration shock EN 60068-2-6 EN 60068-2-27 Resistance to shock Resistance to vibration 6.3 EMC EN 61000-6-2 EN 61000-6-4 Vibration sinus Mechanical shock 25 g 6 ms each 100x on 3 axes (1 g = 9.81 m/s2) Amplitude of excursion 5 mm (peak value) or 10 g from 5 to 2000 Hz each 1 h on 3 axes Interference immunity for industrial environments Interference emission for industrial environments See...
Open the catalog to page 13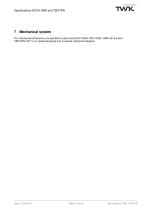
Specifications NOCN, HBN and TBN/TRN 7 Mechanical system The mechanical dimensions are specified in data sheet NOC13099, NOC13292, HBN13218 and/or TBN/TRN14271 or in related drawings due to special mechanical designs. Date: 12.06.2019 Page 14 of 86 Document no. NOC 13100 UE
Open the catalog to page 14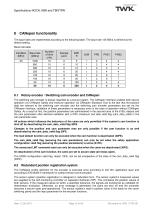
Specifications NOCN, HBN and TBN/TRN 8 CANopen functionality The baud rates are implemented according to the following table. The baud rate 125 kBit/s is defined as the default setting. Baud rate table 8.1 Rotary encoder / Switching cam encoder and CANopen The switching cam encoder is always regarded as a secure system. The CANopen interface enables both secure operation via CANopen Safety and insecure operation via CANopen Standard. Due to the fact that the position data are relevant to the switching cam encoder and the switching cam encoder parameters are set via the CANopen interface,...
Open the catalog to page 15All TWK-ELEKTRONIK GmbH catalogs and technical brochures
-
Rotary encoder TBN58/C3 manual
50 Pages
-
Rotary encoder TBN58/C3
22 Pages
-
Rotary encoder TBD Manual
26 Pages
-
Rotary encoder TBD
12 Pages
-
Rotary encoder TBE58
16 Pages
-
Rotary encoder KRP - Manual
19 Pages
-
Rotary encoder KRP
7 Pages
-
Rotary encoder TBN58/S4 SIL2
22 Pages
-
Rotary encoder TBN50/C3 manual
20 Pages
-
Rotary encoder TBN50/C3
22 Pages
-
Rotary encoder HBN/S3 SIL2
16 Pages
-
Product range 2022
64 Pages
-
Image brochure TWK
28 Pages
-
Inclinometer NBA51
6 Pages
-
Incremental encoder FOI
7 Pages
-
Rotary encoder TBA42
16 Pages
-
Rotary encoder TRA42
16 Pages
-
Rotary encoder TRN58/S4 SIL2
22 Pages
-
Rotary encoder TRN58/C3 manual
50 Pages
-
Rotary encoder TRN58/C3
22 Pages
-
Rotary encoder TRN42/S4 SIL2
22 Pages
-
Manual TRN50/C3
86 Pages
-
Rotary encoder TRN50/C3
22 Pages
-
Rotary encoder TRN42/C3 manual
86 Pages
-
Rotary encoder TRN42/C3
22 Pages
-
Rotary encoder TBN42/S4 SIL2
22 Pages
-
Rotary encoder TBN42/C3 manual
86 Pages
-
Rotary encoder TBN42/C3
22 Pages
-
Rotary encoder TRE58
16 Pages
-
Rotary encoder TRT manual
40 Pages
-
Rotary encoder TRT
14 Pages
-
Switching cam encoder NOCE
14 Pages
-
Switching cam encoder NOCA
17 Pages
-
Vibration sensor NVT/S3 PLd
12 Pages
-
Vibration sensor NVA
12 Pages
-
Inclinometer NBN
17 Pages
-
Incremental encoder TBI42
6 Pages
-
Vibration sensor NVA/S3 PLd
15 Pages
-
Rotary transducer PMR411
1 Pages
-
Rotary encoder TRT/S3 SIL2
13 Pages
-
Rotary transducer VP12
1 Pages
-
Switching cam encoder NOCN
22 Pages
-
Inclination sensor NBT manual
21 Pages
-
Inclination sensor NBT
10 Pages
-
Inclinometer NBA
17 Pages
-
Inclinometer NBT/S3 SIL2/PLd
12 Pages
-
Inclinometer NBN/S3 SIL2
13 Pages
-
Rotary encoder TBE50
16 Pages
-
Rotary encoder HBE
14 Pages
-
Rotary encoder TRK manual
18 Pages
-
Rotary encoder TRK
11 Pages
-
Rotary encoder TMN50 manual
22 Pages
-
Rotary encoder TMN50
6 Pages
-
Rotary encoder TRK/S3 SIL2
14 Pages
-
Rotary encoder TRE42
6 Pages
-
Rotary encoder TRE50
6 Pages
-
Rotary encoder TRA50
6 Pages
-
Rotary encoder TBE42
6 Pages
-
Rotary encoder TME42
6 Pages
-
Rotary encoder TRD manual
26 Pages
-
Rotary encoder TRD
12 Pages
-
Rotary encoder TME50
6 Pages
-
Rotary encoder TBN36
6 Pages
-
Rotary encoder TMA50
6 Pages
-
Rotary encoder TMN42 manual
22 Pages
-
Rotary encoder TMN42
6 Pages
-
Rotary encoder TMA42
6 Pages
-
Rotary encoder TBA50
16 Pages
-
Rotary encoder TBE36 manual
22 Pages
-
Rotary encoder TBE36
6 Pages
-
Rotary encoder TBN42
6 Pages
-
Rotary encoder TBN37
8 Pages
-
Rotary encoder TBA37
7 Pages
-
Rotary encoder TBB50
16 Pages
-
Rotary encoder PBA12
2 Pages
-
Rotary encoder TBA36
6 Pages
-
Rotary encoder TKA60
2 Pages
-
Rotary encoder TKN46 manual
22 Pages
-
Rotary encoder TKN46
7 Pages