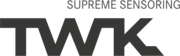
Catalog excerpts
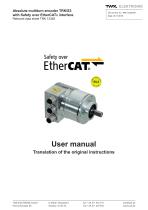
Absolute multiturn encoder TRK/S3 with Safety over EtherCAT® interface Relevant data sheet TRK 13348 User manual Translation of the original instructions TWK-ELEKTRONIK GmbH Heinrichstrasse 85 info@twk.de www.twk.de
Open the catalog to page 1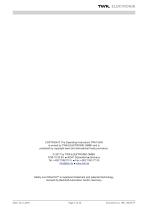
COPYRIGHT: The Operating Instructions TRK13349 is owned by TWK-ELEKTRONIK GMBH and is protected by copyright laws and international treaty provisions. © 2017 by TWK-ELEKTRONIK GMBH POB 10 50 63 ■ 40041 Dusseldorf ■ Germany Tel. +49/211/96117-0 ■ Fax +49/211/63 77 05 info@twk.de ■ www.twk.de Safety over EtherCAT® is registered trademark and patented technology, licensed by Beckhoff Automation GmbH, Germany Date: 20.11.2018 Page 2 of 30 Document no. TRK 13349 FE
Open the catalog to page 2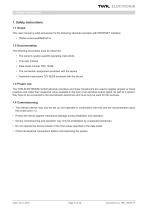
1. Safety instructions 1.1 Scope This user manual is valid exclusively for the following absolute encoders with PROFINET interface: 1.2 Documentation The following documents must be observed: • The owner's system-specific operating instructions • This user manual • Data sheet number TRK 13348 • The connection assignment enclosed with the device • Assembly instructions TZY10206 enclosed with the device 1.3 Proper use The TWK-ELEKTRONIK GmbH absolute encoders and linear transducers are used to register angular or linear positions and make their measured value available in the form of an...
Open the catalog to page 5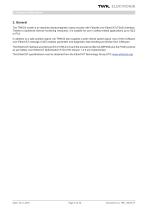
2. General The TRK/S3 model is an absolute electromagnetic rotary encoder with Failsafe over EtherCAT (FSoE) interface. Thanks to additional internal monitoring measures, it is suitable for use in safety-related applications up to SIL2 or PLd. In addition to a safe position signal, the TRK/S3 also supplies a safe vehicle speed signal. Use of the CANopen over EtherCAT message (CoE) enables parameter and diagnostic data handling as familiar from CANopen. The EtherCAT interface according to IEC 61158-2 to 6 and the encoder profile CiA DSP406 plus the FSoE protocol as per Safety over EtherCAT...
Open the catalog to page 6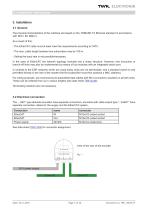
3. Installation 3.1 General The physical characteristics of the interface are based on the 100BASE-TX Ethernet standard in accordance with ISO/ I EC 8802-3. As a result of this: - The EtherCAT cable must at least meet the requirements according to CAT5. - The max. cable length between two subscribers may be 100 m. - Setting the baud rate is not possible/necessary. In the case of EtherCAT, the network topology normally has a linear structure. However, tree structures or branch-off lines may also be implemented by means of bus modules with an integrated switch port. In contrast to the EDP...
Open the catalog to page 7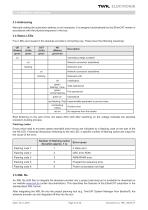
3.3 Addressing Manually setting the subscriber address is not necessary. It is assigned automatically by the EtherCAT master in accordance with the physical sequence in the bus. 3.4 Status LEDs Four LEDs are housed in the absolute encoder‘s connecting cap. These have the following meanings: 3.5 XML file An XML file (ESI file) to integrate the absolute encoder into a project planning tool is available for download on our website www.twk.de (under documentation). This describes the features of the EtherCAT subscriber in the standardised XML format. After integrating the XML file into the...
Open the catalog to page 8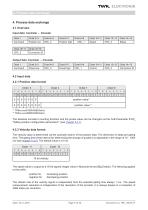
4.1 Overview Input data: Controler ^ Encoder The speed value is output as a 16-bit signed integer value in Motorola format (Big Endian). The following applies to the prefix: positive for increasing position negative for decreasing position The refresh rate of the velocity signal is independent from the selected gating time always 1 ms.. The speed measurement resolution is independent of the resolution of the encoder. It is always based on a resolution of 4096 steps per revolution. Date: 20.11.2018 Page 9 of 30 Document no. TRK 13349 FE
Open the catalog to page 9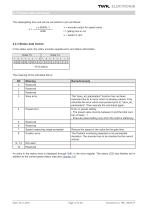
The steps/gating time unit can be converted to rpm as follows: v = encoder output for speed value t = gating time in ms u = speed in rpm 4.2.3 Status data format In the status word, the rotary encoder supplies error and status information. An entry in the status word is displayed through 0x81 in the error register. The status LED also flashes red in addition to the current green status (see also chapter 3.4). Date: 20.11.2018 Page 10 of 30 Document no. TRK 13349 FE
Open the catalog to page 10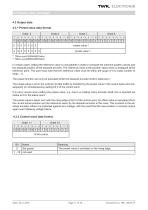
4.3 Output data 4.3.1 Preset value data format Date: 20.11.2018 Page 11 of 30 Document no. TRK 13349 FE
Open the catalog to page 11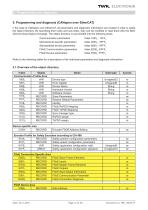
5. Programming and diagnosis (CANopen over EtherCAT) n the case of CANopen over EtherCAT, all parameters and diagnostic information are located in what is called the object directory. By specifying their index and sub-index, they can be modified or read there with the SDO (Service Data Object) message. The object directory is sub-divided into the following areas: Communication parameters Index 1000h - 1FFFh Manufacturer-specific parameters Index 2000h - 5FFFh Standardised device parameters Index 6000h - 9FFFh FSoE Communication parameters Index E000h- EFFFh FSoE Device parameters Index...
Open the catalog to page 12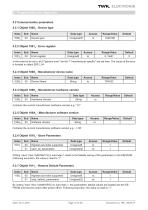
5.2 Communication parameters 5.2.1 Objekt 1000h - Device type By writing “load” (hex: 0x64616F6C) in sub-index 1, the parameters’ default values are loaded into the EEPROM and become active after power off/on. Following execution, the value is reset to “1”. Date: 20.11.2018 Page 13 of 30 Document no. TRK 13349 FE
Open the catalog to page 13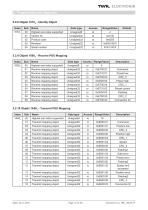
5.2.8 Objekt 1018h - Identity Object Date: 20.11.2018 Page 14 of 30 Document no. TRK 13349 FE
Open the catalog to page 14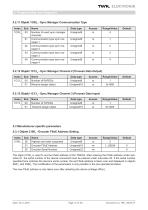
5.2.11 Objekt 1C00h - Sync Manager Communication Type The object 2100h is used to set the FSoE address of the TRK/S3. After entering the FSoE address under subindex 01, the serial number of the device concerned must be entered under sub-index 02. If the serial number specified here matches the device's serial number, the set FSoE address is taken over and displayed in objects E901h and F980h. The modification of the parameters is only possible in the pre-operiational status. The new FSoE address is only taken over after restarting the device (voltage off/on). Date: 20.11.2018 Page 15 of 30...
Open the catalog to page 15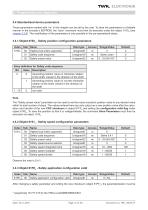
5.4 Standardised device parameters Those parameters marked with “rw” in this chapter can be set by the user. To store the parameters in a failsafe manner in the encoder’s EEPROM, the “save” command must then be executed under the object 1010h (see chapter 5.2.6) .The modification of the parameters is only possible in the pre-operiational status. 5.4.1 Objekt 6100h - Safety position configuration parameters After changing a safety parameter and writing the new checksum (object 61FFh), the parameterisation must be Date: 20.11.2018 Page 16 of 30 Document no. TRK 13349 FE
Open the catalog to page 16All TWK-ELEKTRONIK GmbH catalogs and technical brochures
-
Rotary encoder TBN58/C3 manual
50 Pages
-
Rotary encoder TBN58/C3
22 Pages
-
Rotary encoder TBD Manual
26 Pages
-
Rotary encoder TBD
12 Pages
-
Rotary encoder TBE58
16 Pages
-
Rotary encoder KRP - Manual
19 Pages
-
Rotary encoder KRP
7 Pages
-
Rotary encoder TBN58/S4 SIL2
22 Pages
-
Rotary encoder TBN50/C3 manual
20 Pages
-
Rotary encoder TBN50/C3
22 Pages
-
Rotary encoder HBN/S3 SIL2
16 Pages
-
Product range 2022
64 Pages
-
Image brochure TWK
28 Pages
-
Inclinometer NBA51
6 Pages
-
Incremental encoder FOI
7 Pages
-
Rotary encoder TBA42
16 Pages
-
Rotary encoder TRA42
16 Pages
-
Rotary encoder TRN58/S4 SIL2
22 Pages
-
Rotary encoder TRN58/C3 manual
50 Pages
-
Rotary encoder TRN58/C3
22 Pages
-
Rotary encoder TRN42/S4 SIL2
22 Pages
-
Manual TRN50/C3
86 Pages
-
Rotary encoder TRN50/C3
22 Pages
-
Rotary encoder TRN42/C3 manual
86 Pages
-
Rotary encoder TRN42/C3
22 Pages
-
Rotary encoder TBN42/S4 SIL2
22 Pages
-
Rotary encoder TBN42/C3 manual
86 Pages
-
Rotary encoder TBN42/C3
22 Pages
-
Rotary encoder TRE58
16 Pages
-
Rotary encoder TRT manual
40 Pages
-
Rotary encoder TRT
14 Pages
-
Switching cam encoder NOCE
14 Pages
-
Switching cam encoder NOCA
17 Pages
-
Vibration sensor NVT/S3 PLd
12 Pages
-
Vibration sensor NVA
12 Pages
-
Inclinometer NBN
17 Pages
-
Incremental encoder TBI42
6 Pages
-
Vibration sensor NVA/S3 PLd
15 Pages
-
Rotary transducer PMR411
1 Pages
-
Rotary encoder TRT/S3 SIL2
13 Pages
-
Rotary transducer VP12
1 Pages
-
Switching cam encoder NOCN
22 Pages
-
Inclination sensor NBT manual
21 Pages
-
Inclination sensor NBT
10 Pages
-
Inclinometer NBA
17 Pages
-
Inclinometer NBT/S3 SIL2/PLd
12 Pages
-
Inclinometer NBN/S3 SIL2
13 Pages
-
Rotary encoder TBE50
16 Pages
-
Rotary encoder HBE
14 Pages
-
Rotary encoder TRK manual
18 Pages
-
Rotary encoder TRK
11 Pages
-
Rotary encoder TMN50 manual
22 Pages
-
Rotary encoder TMN50
6 Pages
-
Rotary encoder TRK/S3 SIL2
14 Pages
-
Rotary encoder TRE42
6 Pages
-
Rotary encoder TRE50
6 Pages
-
Rotary encoder TRA50
6 Pages
-
Rotary encoder TBE42
6 Pages
-
Rotary encoder TME42
6 Pages
-
Rotary encoder TRD manual
26 Pages
-
Rotary encoder TRD
12 Pages
-
Rotary encoder TME50
6 Pages
-
Rotary encoder TBN36
6 Pages
-
Rotary encoder TMA50
6 Pages
-
Rotary encoder TMN42 manual
22 Pages
-
Rotary encoder TMN42
6 Pages
-
Rotary encoder TMA42
6 Pages
-
Rotary encoder TBA50
16 Pages
-
Rotary encoder TBE36 manual
22 Pages
-
Rotary encoder TBE36
6 Pages
-
Rotary encoder TBN42
6 Pages
-
Rotary encoder TBN37
8 Pages
-
Rotary encoder TBA37
7 Pages
-
Rotary encoder TBB50
16 Pages
-
Rotary encoder PBA12
2 Pages
-
Rotary encoder TBA36
6 Pages
-
Rotary encoder TKA60
2 Pages
-
Rotary encoder TKN46 manual
22 Pages
-
Rotary encoder TKN46
7 Pages