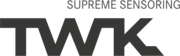
Catalog excerpts
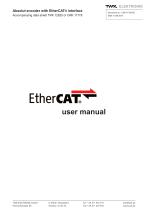
Absolut encoder with EtherCAT® interface Accompanying data sheet TRK 12825 or CRK 11778 user manual TWK-ELEKTRONIK GmbH Heinrichstrasse 85 info@twk.de www.twk.de
Open the catalog to page 1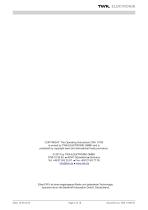
COPYRIGHT: The Operating Instructions CRK 11780 is owned by TWK-ELEKTRONIK GMBH and is protected by copyright laws and international treaty provisions. © 2013 by TWK-ELEKTRONIK GMBH POB 10 50 63 ■ 40041 Dusseldorf ■ Germany Tel. +49/211/63 20 67 ■ Fax +49/211/63 77 05 info@twk.de ■ www.twk.de EtherCAT® ist eine eingetragene Marke und patentierte Technologie, lizenziert durch die Beckhoff Automation GmbH, Deutschland. Date: 10.09.2013 Page 2 of 18 document no. CRK 11780 EE
Open the catalog to page 2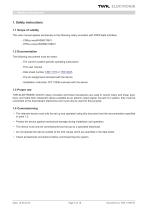
1. Safety instructions 1. Safety instructions 1.1 Scope of validity This user manual applies exclusively to the following rotary encoders with PROFIsafe interface: 1.2 Documentation The following documents must be noted: - The owner's system-specific operating instructions - This user manual - Data sheet number CRK11778 or TRK12825 - The pin assignment enclosed with the device - Installation instruction TZY 10206 enclosed with the device 1.3 Proper use TWK-ELEKTRONIK GmbH's rotary encoders and linear transducers are used to record rotary and linear positions, and make their measured values...
Open the catalog to page 5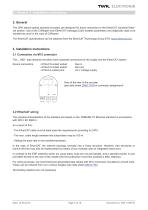
2. General 3. Installation instructions 2. General The CRK electro-optical absolute encoders are designed for direct connection to the EtherCAT industrial Ethernet system. Use of the CANopen over EtherCAT message (CoE) enables parameters and diagnostic data to be handled as usual in the case of CANopen. The EtherCAT specifications can be obtained from the EtherCAT Technology Group ETG (www.ethercat.org). 3. Installation instructions 3.1 Connection via M12 connector The „...M01“ type absolute encoders have separate connectors for the supply and the EtherCAT system. Device connectors: - M12x4...
Open the catalog to page 6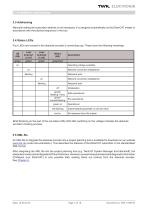
3.3 Addressing Manually setting the subscriber address is not necessary. It is assigned automatically by the EtherCAT master in accordance with the physical sequence in the bus. 3.4 Status LEDs Four LEDs are housed in the absolute encoder‘s connecting cap. These have the following meanings: Brief flickering on the part of the red status (NS) LED after switching on the voltage indicates the absolute encoder‘s booting process. 3.5 XML file An XML file to integrate the absolute encoder into a project planning tool is available for download on our website www.twk.de (under documentation). This...
Open the catalog to page 7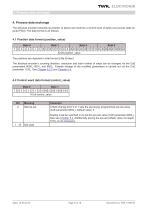
4. Process data exchange The absolute encoder transmits its position (4 bytes) and receives a control word (2 bytes) as process data objects (PDO). The data format is as follows: 4.1 Position data format (position_value) Date: 10.09.2013 Page 8 of 18 document no. CRK 11780 EE
Open the catalog to page 8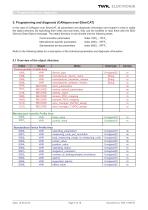
5. Programming and diagnosis (CANopen over EtherCAT) In the case of CANopen over EtherCAT, all parameters and diagnostic information are located in what is called the object directory. By specifying their index and sub-index, they can be modified or read there with the SDO (Service Data Object) message. The object directory is sub-divided into the following areas: Communication parameters Index 1000h - 1FFFh Manufacturer-specific parameters Index 2000h - 5FFFh Standardised device parameters Index 6000h - 9FFFh Refer to the following tables for a description of the individual parameters and...
Open the catalog to page 9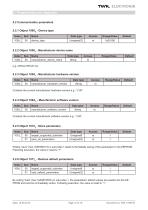
5.2 Communication parameters 5.2.1 Object 1000h - Device type By writing “load” (hex: 0x64616F6C) in sub-index 1, the parameters’ default values are loaded into the EEPROM and become immediately active. Following execution, the value is reset to “1”. Date: 10.09.2013 Page 10 of 18 document no. CRK 11780 EE
Open the catalog to page 10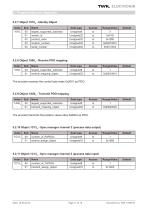
5.2.7 Object 1018h - Identity Object Date: 10.09.2013 Page 11 of 18 document no. CRK 11780 EE
Open the catalog to page 11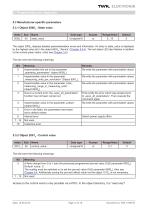
5.3 Manufacturer-specific parameters 5.3.1 Object 2000h - State value Access to the control word is only possible via a PDO. In the object directory, it is “read only”! Date: 10.09.2013 Page 12 of 18 document no. CRK 117
Open the catalog to page 12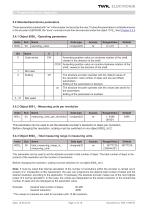
5.4 Standardised device parameters Those parameters marked with “rw” in this chapter can be set by the user. To store the parameters in a failsafe manner in the encoder’s EEPROM, the “save” command must then be executed under the object 1010h. See Chapter 5.2.5 5.4.1 Object 6000h - Operating parameters This parameter can be used to set the absolute encoder’s total number of steps. The total number of steps is the product of the resolution and the number of revolutions. Before changing the resolution, scaling must be switched on via object 6000h bit 2. Note: It must be noted that internal...
Open the catalog to page 13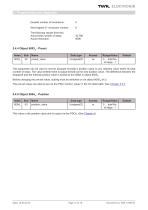
Desired number of revolutions: 5 Next highest 2n revolution number: 8 The following results from this: Actual total number of steps: 32,768 This value is the position value and is output via the PDOs. (See Chapter 4) Date: 10.09.2013 Page 14 of 18 document no. CRK 11780 EE
Open the catalog to page 14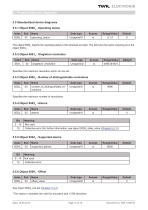
5.5 Standardised device diagnosis 5.5.1 Object 6500h - Operating status See object 6003h pre-set (Chapter 5.4.4) *The values in brackets are valid for encoders with 13 Bit resolution Date: 10.09.2013 Page 15 of 18 document no. CRK 11780 EE
Open the catalog to page 15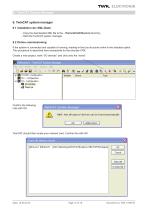
6. TwinCAT system manager 6.1 Installation der XML-Datei - Copy the downloaded XML file to the ..\Twincat\Io\Ethercat directory - Start the TwinCAT system manager 6.2 Online commissioning If the system is connected and capable of running, reading-in the bus structure online is the simplest option. This procedure is described here examplarily for the encoder CRK. Create a new project, mark “I/O devices” and click onto the “wand”. Confirm the following note with OK. TwinCAT should then locate your network card. Confirm this with OK. Date: 10.09.2013 Page 16 of 18 document no. CRK 11780 EE
Open the catalog to page 16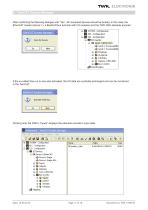
After confirming the following dialogue with “Yes”, all connected devices should be located. In this case, the EtherCAT master (device 1), a Beckhoff bus terminal with I/O modules and the TWK CRK absolute encoder. +I'"5M SYSTEM - Konfiguration m SPS - Konfiguration - E/A - Konfiguration - Jjj} E/A Gerate S' ^ Gerat 1 (EtherCAT) Gerat 1-Prozessabbild Gerat 1-Prozessabbild-+ Eingange ± Ausgange + $ InfoData + jj Klermrme 1 (EK1100) + ^ Box 6 (CRK) a§ Zuordnungen If the so-called free run is now also activated, the I/O data are cyclically exchanged and can be monitored in the TwinCAT. Clicking...
Open the catalog to page 17All TWK-ELEKTRONIK GmbH catalogs and technical brochures
-
Rotary encoder TBN58/C3 manual
50 Pages
-
Rotary encoder TBN58/C3
22 Pages
-
Rotary encoder TBD Manual
26 Pages
-
Rotary encoder TBD
12 Pages
-
Rotary encoder TBE58
16 Pages
-
Rotary encoder KRP - Manual
19 Pages
-
Rotary encoder KRP
7 Pages
-
Rotary encoder TBN58/S4 SIL2
22 Pages
-
Rotary encoder TBN50/C3 manual
20 Pages
-
Rotary encoder TBN50/C3
22 Pages
-
Rotary encoder HBN/S3 SIL2
16 Pages
-
Product range 2022
64 Pages
-
Image brochure TWK
28 Pages
-
Inclinometer NBA51
6 Pages
-
Incremental encoder FOI
7 Pages
-
Rotary encoder TBA42
16 Pages
-
Rotary encoder TRA42
16 Pages
-
Rotary encoder TRN58/S4 SIL2
22 Pages
-
Rotary encoder TRN58/C3 manual
50 Pages
-
Rotary encoder TRN58/C3
22 Pages
-
Rotary encoder TRN42/S4 SIL2
22 Pages
-
Manual TRN50/C3
86 Pages
-
Rotary encoder TRN50/C3
22 Pages
-
Rotary encoder TRN42/C3 manual
86 Pages
-
Rotary encoder TRN42/C3
22 Pages
-
Rotary encoder TBN42/S4 SIL2
22 Pages
-
Rotary encoder TBN42/C3 manual
86 Pages
-
Rotary encoder TBN42/C3
22 Pages
-
Rotary encoder TRE58
16 Pages
-
Rotary encoder TRT manual
40 Pages
-
Rotary encoder TRT
14 Pages
-
Switching cam encoder NOCE
14 Pages
-
Switching cam encoder NOCA
17 Pages
-
Vibration sensor NVT/S3 PLd
12 Pages
-
Vibration sensor NVA
12 Pages
-
Inclinometer NBN
17 Pages
-
Incremental encoder TBI42
6 Pages
-
Vibration sensor NVA/S3 PLd
15 Pages
-
Rotary transducer PMR411
1 Pages
-
Rotary encoder TRT/S3 SIL2
13 Pages
-
Rotary transducer VP12
1 Pages
-
Switching cam encoder NOCN
22 Pages
-
Inclination sensor NBT manual
21 Pages
-
Inclination sensor NBT
10 Pages
-
Inclinometer NBA
17 Pages
-
Inclinometer NBT/S3 SIL2/PLd
12 Pages
-
Inclinometer NBN/S3 SIL2
13 Pages
-
Rotary encoder TBE50
16 Pages
-
Rotary encoder HBE
14 Pages
-
Rotary encoder TRK
11 Pages
-
Rotary encoder TMN50 manual
22 Pages
-
Rotary encoder TMN50
6 Pages
-
Rotary encoder TRK/S3 SIL2
14 Pages
-
Rotary encoder TRE42
6 Pages
-
Rotary encoder TRE50
6 Pages
-
Rotary encoder TRA50
6 Pages
-
Rotary encoder TBE42
6 Pages
-
Rotary encoder TME42
6 Pages
-
Rotary encoder TRD manual
26 Pages
-
Rotary encoder TRD
12 Pages
-
Rotary encoder TME50
6 Pages
-
Rotary encoder TBN36
6 Pages
-
Rotary encoder TMA50
6 Pages
-
Rotary encoder TMN42 manual
22 Pages
-
Rotary encoder TMN42
6 Pages
-
Rotary encoder TMA42
6 Pages
-
Rotary encoder TBA50
16 Pages
-
Rotary encoder TBE36 manual
22 Pages
-
Rotary encoder TBE36
6 Pages
-
Rotary encoder TBN42
6 Pages
-
Rotary encoder TBN37
8 Pages
-
Rotary encoder TBA37
7 Pages
-
Rotary encoder TBB50
16 Pages
-
Rotary encoder PBA12
2 Pages
-
Rotary encoder TBA36
6 Pages
-
Rotary encoder TKA60
2 Pages
-
Rotary encoder TKN46 manual
22 Pages
-
Rotary encoder TKN46
7 Pages