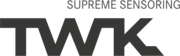
Catalog excerpts
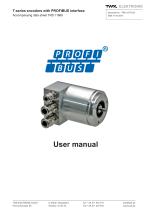
T-series encoders with PROFIBUS interface Accompanying data sheet TRD 11868 User manual TWK-ELEKTRONIK GmbH Heinrichstrasse 85 info@twk.de www.twk.de
Open the catalog to page 1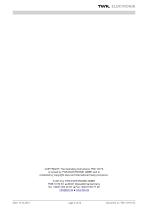
COPYRIGHT: The Operating Instructions TRD 12770 is owned by TWK-ELEKTRONIK GMBH and is protected by copyright laws and international treaty provisions. © 2013 by TWK-ELEKTRONIK GMBH POB 10 50 63 ■ 40041 Dusseldorf ■ Germany Tel. +49/211/63 20 67 ■ Fax +49/211/63 77 05 info@twk.de ■ www.twk.de Date: 19.12.2013 page 2 of 26 document no. TRD 12770 CE
Open the catalog to page 2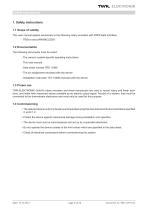
Safety instructions 1. Safety instructions 1.1 Scope of validity This user manual applies exclusively to the following rotary encoders with PROFIsafe interface: 1.2 Documentation The following documents must be noted: - The owner's system-specific operating instructions - This user manual - Data sheet number TRD 11868 - The pin assignment enclosed with the device - Installation instruction TZY 10206 enclosed with the device 1.3 Proper use TWK-ELEKTRONIK GmbH's rotary encoders and linear transducers are used to record rotary and linear positions, and make their measured values available as...
Open the catalog to page 5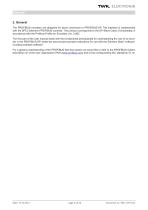
General 2. General The PROFIBUS encoders are designed for direct connection to PROFIBUS-DP. The interface is implemented with the SPC3 Siemens PROFIBUS controler. The protocol corresponds to the DP-Slave Class 2 functionality in accordance with the Profibus-Profile for Encoders, No. 3.062. The first part of the user manual deals with the fundamental prerequisites for understanding the use of an encoder in the PROFIBUS DP, whilst the second part provides instructions for use with the Siemens Step7 software, including example software. For a general understanding of the PROFIBUS field bus...
Open the catalog to page 6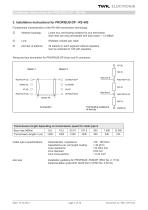
Fundamental characteristics of the RS-485 transmission technology: Linear bus, terminating resistors for bus termination Stub lines are only permissible with baud rates < 1.5 MBit/s Shielded, twisted pair cable 32 stations in each segment without repeaters Can be extended to 126 with repeaters. Wiring and bus termination for PROFIBUS-DP (9-pin sub-D connector): RxD/TxD-P (3) 220 n RxD/TxD-N (8) 390 n DGND (5) Transmission length depending on transmission speed for cable type A Cable type A specifications: Characteristic impedance: Capacitance per unit length coating: Loop resistance: Core...
Open the catalog to page 7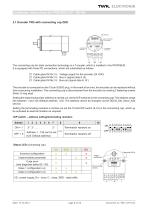
3.1 Encoder TRD with connecting cap ZKD The connecting cap for triple connection technology is a T-coupler, which is installed in the PROFIBUS. It is equipped with three PG connections, which are subdivided as follows: □ Cable gland M12x1.5 □ Cable gland M16x1.5 □ Cable gland M16x1.5 Voltage supply for the encoder (24 VDC) Bus in (signal data A, B) Bus out (signal data A‘, B‘) The encoder is connected via the 15-pin SUB-D plug. In the event of an error, the encoder can be replaced without time-consuming installation. The connecting cap is disconnected from the encoder by undoing 2 fastening...
Open the catalog to page 8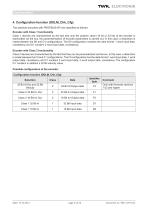
4. Configuration function (DDLM_Chk_Cfg) The absolute encoders with PROFIBUS-DP are classified as follows: Encoder with Class 1 functionality Class 1 devices are characterised by the fact that only the position value (16 bit or 32 bit) of the encoder is transmitted via the bus. No parameterisation of encoder parameters is carried out. In this case, a distinction is made between the D0 and D1 configurations. The D0 configuration contains the data format: 1 word input data, consistency and D1 contains 2 word input data, consistency. Encoder with Class 2 functionality Class 2 devices are...
Open the catalog to page 9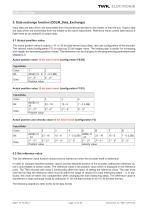
5. Data exchange function (DDLM_Data_Exchange) Input data are data which are transmitted from the peripheral devices to the master or into the bus. Output data are data which are transmitted from the master to the slave subscribers. Reference value control (see below) is listed here as an example of output data. 5.1 Actual position value The actual position value is output in 16- or 32-bit data format (input data), also see configuration of the encoder. The velocity value (configuration F3) is output as 32 bit integer value. The leading sign is positiv for increasing and negativ for...
Open the catalog to page 10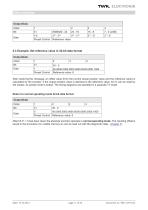
After bit 31 = 0 has been reset, the absolute encoder operates in normal operating mode. The resulting offset is saved in the encoders non volatile memory an can be read out with the diagnoctic data., (chapter 7). Date: 19.12.2013 page 11 of 26 document no. TRD 12770 CE
Open the catalog to page 11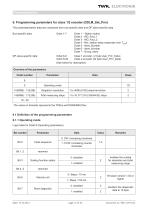
The parameterisation data are comprised from bus-specific data and DP slave-specific data. Bus-specific data: Octet 1-7 Octet 1 - Station status Octet 2 - WD_Fact_1 Octet 3 - WD_Fact_2 Octet 4 - Min. station delay responder (min TSDR) Octet 5 - Ident_Number Octet 6 - Ident_Number Octet 7 - Group_Ident Octet 8-9 Class 1 encoder ( 2 byte User_Prm_Data) Octet 8-29 Class 2 encoder (22 byte User_Prm_Data) Date: 19.12.2013 page 12 of 26 document no. TRD 12770 CE
Open the catalog to page 12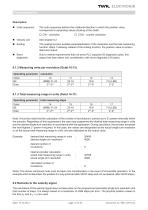
■ Code sequence: The code sequence defines the rotational direction in which the position value corresponds to ascending values (looking at the shaft). □ CW - clockwise □ CCW - counter clockwise The scaling function enables parameterisation of the resolution and the total measuring function: steps. Following release of the scaling function, the position value is recalcu lated and output. Due to market requirements that not every PLC supports 63 diagnostic bytes, this aspect has been taken into consideration with short diagnostic (16 bytes). 6.1.2 Measuring units per revolution (Octet 10-13)...
Open the catalog to page 13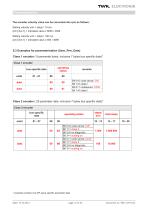
The encoder velocity value can be converted into rpm as follows: Setting velocity unit = steps / 10 ms: rpm [min-1] = indicated value x 6000 / 4096 Setting velocity unit = steps / 100 ms: rpm [min-1] = indicated value x 600 / 4096 6.3 Examples for parameterisation (User_Prm_Data) Class 1 encoder ( 9 parameter bytes, inclusive 7 bytes bus specific data)1 Date: 19.12.2013 page 14 of 26 document no. TRD 12770 CE example contains only DP-slave specific parameter data
Open the catalog to page 14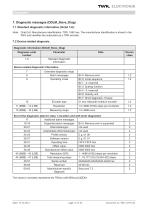
7. Diagnostic messages (DDLM_Slave_Diag) 7.1 Standard diagnostic information (Octet 1-6): Note: Octet 5,6: Manufacturer identification: TRD: 1962 hex. The manufacturer identification is stored in the PNO and identifies the subscriber as a TWK encoder. The values in brackets represents the TRDxx-xx8192RxxxxC2ZD01. Date: 19.12.2013 page 15 of 26 document no. TRD 12770 CE
Open the catalog to page 15All TWK-ELEKTRONIK GmbH catalogs and technical brochures
-
Rotary encoder TBN58/C3 manual
50 Pages
-
Rotary encoder TBN58/C3
22 Pages
-
Rotary encoder TBD Manual
26 Pages
-
Rotary encoder TBD
12 Pages
-
Rotary encoder TBE58
16 Pages
-
Rotary encoder KRP - Manual
19 Pages
-
Rotary encoder KRP
7 Pages
-
Rotary encoder TBN58/S4 SIL2
22 Pages
-
Rotary encoder TBN50/C3 manual
20 Pages
-
Rotary encoder TBN50/C3
22 Pages
-
Rotary encoder HBN/S3 SIL2
16 Pages
-
Product range 2022
64 Pages
-
Image brochure TWK
28 Pages
-
Inclinometer NBA51
6 Pages
-
Incremental encoder FOI
7 Pages
-
Rotary encoder TBA42
16 Pages
-
Rotary encoder TRA42
16 Pages
-
Rotary encoder TRN58/S4 SIL2
22 Pages
-
Rotary encoder TRN58/C3 manual
50 Pages
-
Rotary encoder TRN58/C3
22 Pages
-
Rotary encoder TRN42/S4 SIL2
22 Pages
-
Manual TRN50/C3
86 Pages
-
Rotary encoder TRN50/C3
22 Pages
-
Rotary encoder TRN42/C3 manual
86 Pages
-
Rotary encoder TRN42/C3
22 Pages
-
Rotary encoder TBN42/S4 SIL2
22 Pages
-
Rotary encoder TBN42/C3 manual
86 Pages
-
Rotary encoder TBN42/C3
22 Pages
-
Rotary encoder TRE58
16 Pages
-
Rotary encoder TRT manual
40 Pages
-
Rotary encoder TRT
14 Pages
-
Switching cam encoder NOCE
14 Pages
-
Switching cam encoder NOCA
17 Pages
-
Vibration sensor NVT/S3 PLd
12 Pages
-
Vibration sensor NVA
12 Pages
-
Inclinometer NBN
17 Pages
-
Incremental encoder TBI42
6 Pages
-
Vibration sensor NVA/S3 PLd
15 Pages
-
Rotary transducer PMR411
1 Pages
-
Rotary encoder TRT/S3 SIL2
13 Pages
-
Rotary transducer VP12
1 Pages
-
Switching cam encoder NOCN
22 Pages
-
Inclination sensor NBT manual
21 Pages
-
Inclination sensor NBT
10 Pages
-
Inclinometer NBA
17 Pages
-
Inclinometer NBT/S3 SIL2/PLd
12 Pages
-
Inclinometer NBN/S3 SIL2
13 Pages
-
Rotary encoder TBE50
16 Pages
-
Rotary encoder HBE
14 Pages
-
Rotary encoder TRK manual
18 Pages
-
Rotary encoder TRK
11 Pages
-
Rotary encoder TMN50 manual
22 Pages
-
Rotary encoder TMN50
6 Pages
-
Rotary encoder TRK/S3 SIL2
14 Pages
-
Rotary encoder TRE42
6 Pages
-
Rotary encoder TRE50
6 Pages
-
Rotary encoder TRA50
6 Pages
-
Rotary encoder TBE42
6 Pages
-
Rotary encoder TME42
6 Pages
-
Rotary encoder TRD
12 Pages
-
Rotary encoder TME50
6 Pages
-
Rotary encoder TBN36
6 Pages
-
Rotary encoder TMA50
6 Pages
-
Rotary encoder TMN42 manual
22 Pages
-
Rotary encoder TMN42
6 Pages
-
Rotary encoder TMA42
6 Pages
-
Rotary encoder TBA50
16 Pages
-
Rotary encoder TBE36 manual
22 Pages
-
Rotary encoder TBE36
6 Pages
-
Rotary encoder TBN42
6 Pages
-
Rotary encoder TBN37
8 Pages
-
Rotary encoder TBA37
7 Pages
-
Rotary encoder TBB50
16 Pages
-
Rotary encoder PBA12
2 Pages
-
Rotary encoder TBA36
6 Pages
-
Rotary encoder TKA60
2 Pages
-
Rotary encoder TKN46 manual
22 Pages
-
Rotary encoder TKN46
7 Pages