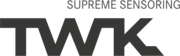
Catalog excerpts
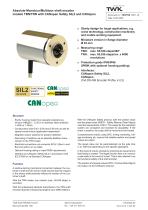
7WK Document no.: TBN/TRN 14271 JE Date: 25.03.2020 Absolute Monotour/Multitour shaft encoder models TBN/TRN with CANopen Safety SIL2 and CANopen ■ Sturdy design for tough applications, e.g. crane technology, construction machinery and mobile working equipment ■ Miniature version in flange diameter 0 42 mm ■ Measuring range TBN: max. 65,536 steps/360° TRN: max. 65,536 steps/rev. x 4096 revolutions ■ Mrotection grade IP65/IP66 (IP69K with optional housing potting) ■ Interfaces: CANopen Safety SIL2, CANopen (CiA DS 406 Encoder Profile, 4.0.2) SIL2I EC 61508 FUNCTIONAL SAFETY SENSOR easy to use CflNopGQ Structure - Sturdy housing made from seawater-resistant aluminium (AlMgSil - 3.2315) or stainless steel (material: 1.4305 or 1.4404) - Constructions with 0 42, 0 50 and 0 58 mm as well as special constructions (application-dependent) - Magnetic sensor systems for position detection - Recording of rotations via an absolute Multitour transmission in the TRN model - Electrical connections via connector M12x1 (Bus In and Bus Out option) or via cable - Optional housing potting to meet IP69K requirements - Interface as CANopen Safety SIL2 in accordance with IEC 61508 or as Standard CANopen Function A positive-locking mechanical connection between the customer's shaft and the sensor shaft ensures that the magnet in the sensor shaft precisely reflects the rotation of the customer's shaft. With the TBN model, one rotation (max. 65,536 steps) is recorded. With the subsequent absolute transmission, the TRN shaft encoder reaches a measuring range of up to 4096 rotations. With the CANopen Safety protocol, both the position value and the speed value (SRDO - Safety Relevant Data Object) meet the requirements of SIL2. The values for the redundant system are compared and checked for plausibility. If the check is positive, the output will be normal and bit-inverted. Comprehensive checks using CRC, timing monitoring, voltage monitoring etc. ensure that reliable position and speed values are output. The speed value can be parameterised via the gate time (1 to 1000 ms) depending on the specific application. In the event of a fault, emergency protocols are issued and a fault listing is created. The target function here is to move to a safe state in the event of a fault. This is also referred to as the functional safety of the shaft encoder. The position and speed values (PDO - Process Data Object) are output via the CANopen protocol. TWK-ELEKTRONIK GmbH BismarckstraBe 108 info@twk.de visit us at | twk.de
Open the catalog to page 1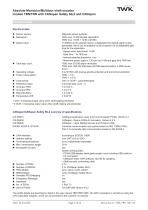
SUPREME SENSORING Technical data Electrical data ■ Sensor system: ■ Resolution: ■ Speed value: ■ Total step count: ■ Operating voltage: ■ Power consumption ■ Code sense: ■ Reference value: ■ Accuracy TBN: ■ AccuracyTRN: ■ Reproducibility: ■ Temperature drift: Magnetic sensor systems TBN: max. 16 Bit (65,536 steps/360°) TRN: max. 16 Bit + 12 Bit (=28 Bit) In addition to the position signal, a digits/gate time speed signal is also generated, which can be adapted by the customer via an adjustable gate time for the application. - Speed value data format: 16 Bit - Gate time: 1 to 1000 ms -...
Open the catalog to page 2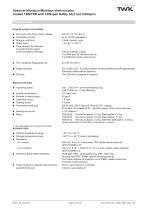
SUPREME SENSORING Technical data Overall system and safety ■ Duty cycle (rise time) supply voltage: ■ Information density: ■ Storage cycle time: ■ Setup Time: ■ Time between the detection of a fault and the output of the emergency message: 500 ms (10 % to 90 %) up to 10 000 messages/s 3 s per memory cycle ~ 2 s @ T > +20 °C ■ TUV Certificate Registration No.: ■ Safety standard: ■ EDS file: 100 ms (voltage supply) 5 s (RAM test, all individual bits ok) 2 s (ROM test (within setup time)) 44 799 13172915 IEC 61508: 2017: Functional Safety of Electrical/Electronic/Programmable Electronic...
Open the catalog to page 3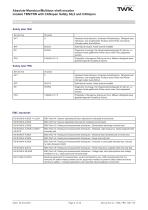
Absolute Monotour/Multitour shaft encoder models TBN/TRN with CANopen Safety SIL2 and CANopenTechnical data Safety data TBN Date: 25.03.2020 Page 4 of 22 Document no.: TBN/TRN 14271 JE
Open the catalog to page 4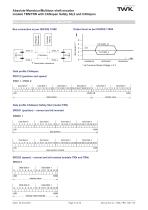
Absolute Monotour/Multitour shaft encoder models TBN/TRN with CANopen Safety SIL2 and CANopenBus connection, output level and data profile Bus connection as per ISO/DIS 11898 Output level as per ISO/DIS 11898 Data profile CANopen PDO1/2 (position and speed) PDO 1 / PDO 2 SRDO2 (speed) - normal and bit-inverted (models TRN and TBN) SRDO 2 velocity value Data Byte 0 Data Byte 1 velocity value inverted Date: 25.03.2020 Page 5 of 22 Document no.: TBN/TRN 14271 JE
Open the catalog to page 5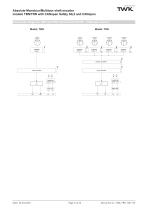
Absolute Monotour/Multitour shaft encoder models TBN/TRN with CANopen Safety SIL2 and CANopen Schematic diagrams TBN and TRN (construction Ø 58 – CANopen shown) Model: TBN magnet singleturn magnet singleturn magnetic sensor position controller main controller switching power unit TWK-SENSORIK GmbH Flerrenwiete 28 Tel. 04103/9323-0 D-22880 Wedel Fax 04103/9323-21 info@twk-sensorik.de switching power unit TWK-SENSORIK GmbH Maßstab: Material: Gepr. Dieses Dokument genießt Urheberrecht und damit den gesetzlich dafür bestehenden Schutz. This document is owned by TWK-Elektronik GmbH and is...
Open the catalog to page 6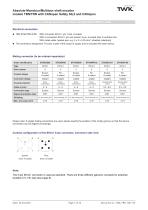
Absolute Monotour/Multitour shaft encoder models TBN/TRN with CANopen Safety SIL2 and CANopenElectrical connection, mating connector, contact configuration M12x1, noteElectrical connection ■ TBN 0 58/TRN 0 58: With connector M12x1, pin, 5-pin, A-coded With 2 connectors M12x1, pin and socket, 5-pin, A-coded, Bus In and Bus Out With radial cable, twisted pair, e.g. 2 x 2 x 0.25 mm2, shielded (standard) ■ The connection assignment TYxxxxx is part of the scope of supply and is included with each device. Please note: If angled mating connectors are used, please specify the position of the coding...
Open the catalog to page 7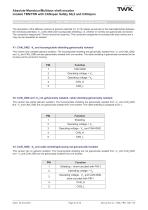
Absolute Monotour/Multitour shaft encoder models TBN/TRN with CANopen Safety SIL2 and CANopenGalvanic potential isolation: -VS, CAN_GND and housing/cable shielding The description of the different versions of galvanic potential (V1 to V3) relates exclusively to the interrelationships between the individual potentials (-VS, CAN_GND and housing/cable shielding), i.e. whether or not they are galvanically connected. The connection assignment (TYxxxx) should be observed. This connection assignment is included with each device and a copy can be requested as needed. V1: CAN_GND, -VS and...
Open the catalog to page 8All TWK-ELEKTRONIK GmbH catalogs and technical brochures
-
Rotary encoder TBN58/C3 manual
50 Pages
-
Rotary encoder TBD Manual
26 Pages
-
Rotary encoder TBD
12 Pages
-
Rotary encoder TBE58
16 Pages
-
Rotary encoder KRP - Manual
19 Pages
-
Rotary encoder KRP
7 Pages
-
Rotary encoder TBN58/S4 SIL2
22 Pages
-
Rotary encoder TBN50/C3 manual
20 Pages
-
Rotary encoder TBN50/C3
22 Pages
-
Rotary encoder HBN/S3 SIL2
16 Pages
-
Product range 2022
64 Pages
-
Image brochure TWK
28 Pages
-
Inclinometer NBA51
6 Pages
-
Incremental encoder FOI
7 Pages
-
Rotary encoder TBA42
16 Pages
-
Rotary encoder TRA42
16 Pages
-
Rotary encoder TRN58/S4 SIL2
22 Pages
-
Rotary encoder TRN58/C3 manual
50 Pages
-
Rotary encoder TRN58/C3
22 Pages
-
Rotary encoder TRN42/S4 SIL2
22 Pages
-
Manual TRN50/C3
86 Pages
-
Rotary encoder TRN50/C3
22 Pages
-
Rotary encoder TRN42/C3 manual
86 Pages
-
Rotary encoder TRN42/C3
22 Pages
-
Rotary encoder TBN42/S4 SIL2
22 Pages
-
Rotary encoder TBN42/C3 manual
86 Pages
-
Rotary encoder TBN42/C3
22 Pages
-
Rotary encoder TRE58
16 Pages
-
Rotary encoder TRT manual
40 Pages
-
Rotary encoder TRT
14 Pages
-
Switching cam encoder NOCE
14 Pages
-
Switching cam encoder NOCA
17 Pages
-
Vibration sensor NVT/S3 PLd
12 Pages
-
Vibration sensor NVA
12 Pages
-
Inclinometer NBN
17 Pages
-
Incremental encoder TBI42
6 Pages
-
Vibration sensor NVA/S3 PLd
15 Pages
-
Rotary transducer PMR411
1 Pages
-
Rotary encoder TRT/S3 SIL2
13 Pages
-
Rotary transducer VP12
1 Pages
-
Switching cam encoder NOCN
22 Pages
-
Inclination sensor NBT manual
21 Pages
-
Inclination sensor NBT
10 Pages
-
Inclinometer NBA
17 Pages
-
Inclinometer NBT/S3 SIL2/PLd
12 Pages
-
Inclinometer NBN/S3 SIL2
13 Pages
-
Rotary encoder TBE50
16 Pages
-
Rotary encoder HBE
14 Pages
-
Rotary encoder TRK manual
18 Pages
-
Rotary encoder TRK
11 Pages
-
Rotary encoder TMN50 manual
22 Pages
-
Rotary encoder TMN50
6 Pages
-
Rotary encoder TRK/S3 SIL2
14 Pages
-
Rotary encoder TRE42
6 Pages
-
Rotary encoder TRE50
6 Pages
-
Rotary encoder TRA50
6 Pages
-
Rotary encoder TBE42
6 Pages
-
Rotary encoder TME42
6 Pages
-
Rotary encoder TRD manual
26 Pages
-
Rotary encoder TRD
12 Pages
-
Rotary encoder TME50
6 Pages
-
Rotary encoder TBN36
6 Pages
-
Rotary encoder TMA50
6 Pages
-
Rotary encoder TMN42 manual
22 Pages
-
Rotary encoder TMN42
6 Pages
-
Rotary encoder TMA42
6 Pages
-
Rotary encoder TBA50
16 Pages
-
Rotary encoder TBE36 manual
22 Pages
-
Rotary encoder TBE36
6 Pages
-
Rotary encoder TBN42
6 Pages
-
Rotary encoder TBN37
8 Pages
-
Rotary encoder TBA37
7 Pages
-
Rotary encoder TBB50
16 Pages
-
Rotary encoder PBA12
2 Pages
-
Rotary encoder TBA36
6 Pages
-
Rotary encoder TKA60
2 Pages
-
Rotary encoder TKN46 manual
22 Pages
-
Rotary encoder TKN46
7 Pages