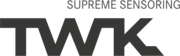
Catalog excerpts
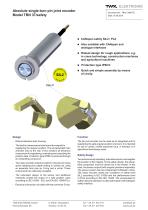
■ CANopen safety SIL2 / PLd ■ Also available with CANopen and analogue interfaces ■ Robust design for rough applications, e.g. in crane technology, construction machines and agricultural machines ■ Protection type IP69 K ■ Quick and simple assembly by means of circlip Design - Robust stainless steel housing. - The shaft or measurement axis bears the magnet for registering the angular position. The encapsulated main chamber area to the rear of this contains all electronic components for registering, evaluating and outputting the position data. Protection type IP69K is achieved through an embedding compound. - The rotary encoder is fixed in position in the pin joint using spiral clamping pins (depth setting is carried out using an assembly tool) plus an O-ring and a circlip. These components are optionally available. - The redundant design of the sensor and additional measures enable the output of a safe position value according to IEC 61508 - SIL2 and EN ISO 13849-PLd. - Electrical connection via cable with test connector D-sub. Function The pin joint encoder can be used as an integrated unit for registering the safe angular position of a boom. It is intended for use in cranes, mobile equipment (e.g. in forestry) or in agricultural technology areas. Safety design Two autonomously operating, redundant sensor units register the position of the magnet. In this safety design, the plausibility comparison must be carried out in the master. In this case, the sensor outputs both angular positions separately. The sensor system has two independent CANopen nodes. The rotary encoder meets the conditions of safety level SIL2 according to IEC 61508 and the performance level d (PLd) according to EN ISO 13849. The prerequisite for safety-relevant operation is a fail-safe master with CANopen safety interface. TWK-ELEKTRONIK GmbH Heinrichstrasse 85 info@twk.de www.twk.de
Open the catalog to page 1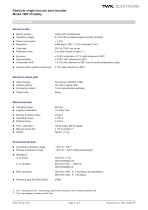
Date: 07.06.2016 Page 2 of 8 Document no. TBN 13080 FE CW = ascending (CCW = descending) signal viewed looking at the clockwise-rotating shaft.
Open the catalog to page 2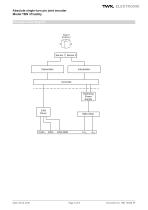
Absolute single-turn pin joint encoder Model TBN 37/safety Principle circuit diagram Switching Power Supply
Open the catalog to page 3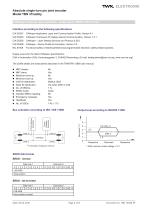
CANopen Application Layer and Communication Profile, Version 4.1 CANopen Framework for Safety-relevant Communication, Version 1.0.1 CANopen - Layer Setting Services and Protocol (LSS) CANopen - Device Profile for Encoders, Version 3.0 Functional safety of electrical/electronic/programmable electronic safety-related systems. Supply source for the listed CANopen specifications: CAN in Automation (CiA), Kontumazgarten 3, D-90429 Nuremberg, (E-mail: headquarters@can-cia.org, www.can-cia.org) The profile details are exhaustively described in the TBN/TRN 12889 user manual. No Yes No Yes Default,...
Open the catalog to page 4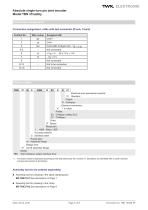
Connection assignment, cable with test connector (D-sub, 15-pin) TBN 37 - M S 4096 R S3 K N 01 Electrical and mechanical variants* 01 Standard Output: N CANopen Electrical connection: K 1 m cable Profile: S3 CANopen safety SIL2 C2 CANopen Code: R Binary Resolution: 1 ... 4096 Steps / 360° Housing material: S Stainless steel Flange type: M Assembly flange Design form: 37 mm 0 assembly flange Model: TBN With CANopen safety interface SIL2 *) The basic versions (standard) according to the data sheet bear the number 01. Deviations are identified with a variant number and are documented in the...
Open the catalog to page 5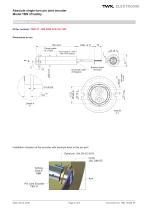
Absolute single-turn pin joint encoder Model TBN 37/safety Installation drawing Order number: TBN 37 - MS 4096 R S3 K1 N01 Dimensions in mm Tube made of 1.4301 (with PUR-potting) Grommet made of Neopren Braided shield removed with bevel 2.2x45° Installation situation of the encoder with example lever in the pin joint Spiral pin DIN EN ISO 8750 Circlip Seeger-Ring O-Ring 25x2,5 NBR Arm Pin Joint Encoder TBX 37
Open the catalog to page 6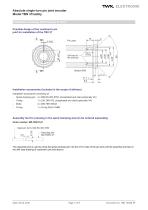
Installation accessories (included in the scope of delivery) Installation accessories consisting of: - Spiral clamping pin: 2 x DIN EN ISO 8750, phosphated and oiled (optionally VA) - Circlip: 1 x J38, DIN 472, phosphated and oiled (optionally VA) The assembly tool is used to press the spiral clamping pin into the 3 H12 hole of the pin joint until the assembly tool lies on the 040 (see drawing of customer's pin joint above). Date: 07.06.2016 Page 7 of 8 Document no. TBN 13080 FE
Open the catalog to page 7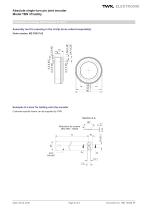
Absolute single-turn pin joint encoder Model TBN 37/safety Installation drawing (dimensions in mm) Assembly tool for pressing in the circlip (to be ordered separately) Example of a lever for bolting onto the encoder Customer-specific levers can be supplied by TWK.
Open the catalog to page 8All TWK-ELEKTRONIK GmbH catalogs and technical brochures
-
Rotary encoder TBN58/C3 manual
50 Pages
-
Rotary encoder TBN58/C3
22 Pages
-
Rotary encoder TBD Manual
26 Pages
-
Rotary encoder TBD
12 Pages
-
Rotary encoder TBE58
16 Pages
-
Rotary encoder KRP - Manual
19 Pages
-
Rotary encoder KRP
7 Pages
-
Rotary encoder TBN58/S4 SIL2
22 Pages
-
Rotary encoder TBN50/C3 manual
20 Pages
-
Rotary encoder TBN50/C3
22 Pages
-
Rotary encoder HBN/S3 SIL2
16 Pages
-
Product range 2022
64 Pages
-
Image brochure TWK
28 Pages
-
Inclinometer NBA51
6 Pages
-
Incremental encoder FOI
7 Pages
-
Rotary encoder TBA42
16 Pages
-
Rotary encoder TRA42
16 Pages
-
Rotary encoder TRN58/S4 SIL2
22 Pages
-
Rotary encoder TRN58/C3 manual
50 Pages
-
Rotary encoder TRN58/C3
22 Pages
-
Rotary encoder TRN42/S4 SIL2
22 Pages
-
Manual TRN50/C3
86 Pages
-
Rotary encoder TRN50/C3
22 Pages
-
Rotary encoder TRN42/C3 manual
86 Pages
-
Rotary encoder TRN42/C3
22 Pages
-
Rotary encoder TBN42/S4 SIL2
22 Pages
-
Rotary encoder TBN42/C3 manual
86 Pages
-
Rotary encoder TBN42/C3
22 Pages
-
Rotary encoder TRE58
16 Pages
-
Rotary encoder TRT manual
40 Pages
-
Rotary encoder TRT
14 Pages
-
Switching cam encoder NOCE
14 Pages
-
Switching cam encoder NOCA
17 Pages
-
Vibration sensor NVT/S3 PLd
12 Pages
-
Vibration sensor NVA
12 Pages
-
Inclinometer NBN
17 Pages
-
Incremental encoder TBI42
6 Pages
-
Vibration sensor NVA/S3 PLd
15 Pages
-
Rotary transducer PMR411
1 Pages
-
Rotary encoder TRT/S3 SIL2
13 Pages
-
Rotary transducer VP12
1 Pages
-
Switching cam encoder NOCN
22 Pages
-
Inclination sensor NBT manual
21 Pages
-
Inclination sensor NBT
10 Pages
-
Inclinometer NBA
17 Pages
-
Inclinometer NBT/S3 SIL2/PLd
12 Pages
-
Inclinometer NBN/S3 SIL2
13 Pages
-
Rotary encoder TBE50
16 Pages
-
Rotary encoder HBE
14 Pages
-
Rotary encoder TRK manual
18 Pages
-
Rotary encoder TRK
11 Pages
-
Rotary encoder TMN50 manual
22 Pages
-
Rotary encoder TMN50
6 Pages
-
Rotary encoder TRK/S3 SIL2
14 Pages
-
Rotary encoder TRE42
6 Pages
-
Rotary encoder TRE50
6 Pages
-
Rotary encoder TRA50
6 Pages
-
Rotary encoder TBE42
6 Pages
-
Rotary encoder TME42
6 Pages
-
Rotary encoder TRD manual
26 Pages
-
Rotary encoder TRD
12 Pages
-
Rotary encoder TME50
6 Pages
-
Rotary encoder TBN36
6 Pages
-
Rotary encoder TMA50
6 Pages
-
Rotary encoder TMN42 manual
22 Pages
-
Rotary encoder TMN42
6 Pages
-
Rotary encoder TMA42
6 Pages
-
Rotary encoder TBA50
16 Pages
-
Rotary encoder TBE36 manual
22 Pages
-
Rotary encoder TBE36
6 Pages
-
Rotary encoder TBN42
6 Pages
-
Rotary encoder TBA37
7 Pages
-
Rotary encoder TBB50
16 Pages
-
Rotary encoder PBA12
2 Pages
-
Rotary encoder TBA36
6 Pages
-
Rotary encoder TKA60
2 Pages
-
Rotary encoder TKN46 manual
22 Pages
-
Rotary encoder TKN46
7 Pages