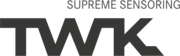
Catalog excerpts
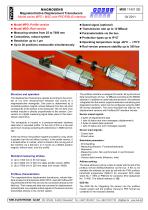
■ Model MPD: Profile version ■ Model MSD: Rod version ■ Measuring strokes from 25 to 7600 mm ■ Contactless, robust system ■ Resolution up to 1 pm ■ Up to 20 positions measurable simultaneously ■ Speed signal (optional) ■ Transmission rate up to 12 MBaud ■ Parameterisable via the bus ■ Protection types up to IP 67 ■ Operating temperature range -40°C ... +75°C ■ Rod version pressure stability up to 350 bar Structure and operation The displacement transducers operate according to the principle of run time measurement between two points of a magnetostrictive waveguide. One point is determined by a moveable position magnet, whose distance from the null point corresponds to the section to be measured. The run time of an emitted impulse is directly proportionate to this section. Conversion to a digital measuring signal takes place in the downstream electronics. The waveguide is housed in a pressure-resistant stainless steel tube or extruded profile. To the rear of this is a die-cast aluminium housing containing the electronics in SMD technology. In the rod version, the position magnet is located in a ring, which is guided over the rod without contact. In the profile version, it is located either in a slider, which is linked to the moving part of the machine via a ball joint, or it moves as a liftable position magnet, without wear, over the profile. Standard measuring strokes □ Up to 1000 mm in 50 mm steps □ Up to 5000 mm in 250 mm steps (profile version: MPD) □ Up to 7600 mm in 250 mm steps (rod version: MSD) Profibus characteristics The magnetostrictive displacement transducers, whose interface is based on the Siemens ASIC SPC3, meet all Profibus-DP requirements (EN 50170) and can be connected directly to the field bus. Their measured data are converted to displacement-proportionale, bus-capable output signals in the sensor and are transmitted directly to the control system. The profibus interface is designed for serial, bit-synchronous data transmission of max. 12 MBaud according to the RS485 standard. In addition to useful data transmission, the software integrated into the sensor supports extensive monitoring and diagnostic functions, which can be configured using the GSD file during installation. The most important key data for the displacement sensors with Profibus-DP interface include: Sensor output signals: - 3 bytes of displacement data - 1 byte of status and error messages (displacement) - 3 bytes of speed data (optional) - 1 byte of status and error messages (speed) Sensor input signals: - Control byte - Preset value Selectable parameters: - Errorhandling - Measuring direction: Forwards/backwards - Resolution - Measuring cycle: Non-synchronised or synchronised (optional) - Various data formats (Motorola, Intel) Address setting: The slave address is set by a class 2 master with the aid of the profibus service SetSlaveAddress via the bus. If this is not available the address can also be set with the TWK profibus hand-held programmer PMD-01 for connector M16 (data sheet No. 11190) or PMD-02 for connector M12 (datasheet No. 11450). The default address is 125. GSD file: The GSD file for integrating the sensor into the profibus master system and the profibus manual in PDF format are contained in the enclosed diskette. TWK-ELEKTRONIK GmbH ■ PB. 10 50 63 ■ D-40041 Dusseldorf ■ Tel.: +49/211/63 20 67 ■ Fax: +49/211/63 77 05 ■ info@twk.de ■
Open the catalog to page 1
Diagnosis The LEDs (green/red) in the sensor head are used for adjustment and additionally provide information on the sensor status. Technical data ■ Supply voltage range VS: ■ Supply current IS: ■ Resolution □ Displacement in pm: □ Speed: 24VDC (+20 / -15%) 90 mA (typical) 1, 5, 10, 20, 50, 100, 200, 500. 1000 Resolution of 5 pm: 0.64 mm/s up to 500 mm 0.43 mm/s up to 2000 mm 0.21 mm/s up to 4500 mm 0.14mm/s up to 7600 mm For a resolution of 2 mm: 2.5 times smaller Profibus-DP to EN 50 170 Differential signal as per RS485 Max. 12 MBit/s 125 ■ Protection type □ Profile: □ Rod: ■ Operating...
Open the catalog to page 2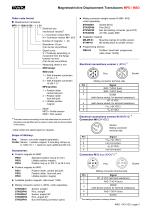
Electrical and mechanical variants* L = Connector version M16 M = Connector version M8 / M12 Number of magnets: 1 - 20 Resolution= 20 pm (Can be set via profibus) Signal curve: S = Positively ascending on movement from the flange towards rod end (Can be set via profibus) Measuring stroke in mm MSD design MSD (rod): 1 = With threaded connection M 18 x 1.5 2 = With threaded connection 16 UN F % “ MPD (profile): 1 = Position slider central ball joint 2 = Position slider front ball joint 3 = Liftable position magnet Model MPD = Profile version MSD = Rod version *The basic versions according to...
Open the catalog to page 3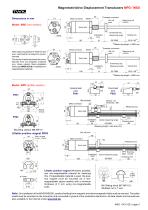
Magnetostrictive Displacement Transducers MPD / MSD Metal connector Threaded connection Model: MSD (rod version) Sensor head Positioning ring Measuring range Installation zone Damping zone Metal connector With measuring strokes of 1000 mm and over, mechanical rod support is recommended. The sensor’s fastening should be manufactured from non-magnetic materials (e.g.: brass, plastic). Note installation instruction MWA10318 on installation in magnetisable materials. Threaded connection Sensor head Positioning ring Measuring range Installation zone Damping zone Front ball joint PS02 Set null...
Open the catalog to page 4All TWK-ELEKTRONIK GmbH catalogs and technical brochures
-
Rotary encoder TBN58/C3 manual
50 Pages
-
Rotary encoder TBN58/C3
22 Pages
-
Rotary encoder TBD Manual
26 Pages
-
Rotary encoder TBD
12 Pages
-
Rotary encoder TBE58
16 Pages
-
Rotary encoder KRP - Manual
19 Pages
-
Rotary encoder KRP
7 Pages
-
Rotary encoder TBN58/S4 SIL2
22 Pages
-
Rotary encoder TBN50/C3 manual
20 Pages
-
Rotary encoder TBN50/C3
22 Pages
-
Rotary encoder HBN/S3 SIL2
16 Pages
-
Product range 2022
64 Pages
-
Image brochure TWK
28 Pages
-
Inclinometer NBA51
6 Pages
-
Incremental encoder FOI
7 Pages
-
Rotary encoder TBA42
16 Pages
-
Rotary encoder TRA42
16 Pages
-
Rotary encoder TRN58/S4 SIL2
22 Pages
-
Rotary encoder TRN58/C3 manual
50 Pages
-
Rotary encoder TRN58/C3
22 Pages
-
Rotary encoder TRN42/S4 SIL2
22 Pages
-
Manual TRN50/C3
86 Pages
-
Rotary encoder TRN50/C3
22 Pages
-
Rotary encoder TRN42/C3 manual
86 Pages
-
Rotary encoder TRN42/C3
22 Pages
-
Rotary encoder TBN42/S4 SIL2
22 Pages
-
Rotary encoder TBN42/C3 manual
86 Pages
-
Rotary encoder TBN42/C3
22 Pages
-
Rotary encoder TRE58
16 Pages
-
Rotary encoder TRT manual
40 Pages
-
Rotary encoder TRT
14 Pages
-
Switching cam encoder NOCE
14 Pages
-
Switching cam encoder NOCA
17 Pages
-
Vibration sensor NVT/S3 PLd
12 Pages
-
Vibration sensor NVA
12 Pages
-
Inclinometer NBN
17 Pages
-
Incremental encoder TBI42
6 Pages
-
Vibration sensor NVA/S3 PLd
15 Pages
-
Rotary transducer PMR411
1 Pages
-
Rotary encoder TRT/S3 SIL2
13 Pages
-
Rotary transducer VP12
1 Pages
-
Switching cam encoder NOCN
22 Pages
-
Inclination sensor NBT manual
21 Pages
-
Inclination sensor NBT
10 Pages
-
Inclinometer NBA
17 Pages
-
Inclinometer NBT/S3 SIL2/PLd
12 Pages
-
Inclinometer NBN/S3 SIL2
13 Pages
-
Rotary encoder TBE50
16 Pages
-
Rotary encoder HBE
14 Pages
-
Rotary encoder TRK manual
18 Pages
-
Rotary encoder TRK
11 Pages
-
Rotary encoder TMN50 manual
22 Pages
-
Rotary encoder TMN50
6 Pages
-
Rotary encoder TRK/S3 SIL2
14 Pages
-
Rotary encoder TRE42
6 Pages
-
Rotary encoder TRE50
6 Pages
-
Rotary encoder TRA50
6 Pages
-
Rotary encoder TBE42
6 Pages
-
Rotary encoder TME42
6 Pages
-
Rotary encoder TRD manual
26 Pages
-
Rotary encoder TRD
12 Pages
-
Rotary encoder TME50
6 Pages
-
Rotary encoder TBN36
6 Pages
-
Rotary encoder TMA50
6 Pages
-
Rotary encoder TMN42 manual
22 Pages
-
Rotary encoder TMN42
6 Pages
-
Rotary encoder TMA42
6 Pages
-
Rotary encoder TBA50
16 Pages
-
Rotary encoder TBE36 manual
22 Pages
-
Rotary encoder TBE36
6 Pages
-
Rotary encoder TBN42
6 Pages
-
Rotary encoder TBN37
8 Pages
-
Rotary encoder TBA37
7 Pages
-
Rotary encoder TBB50
16 Pages
-
Rotary encoder PBA12
2 Pages
-
Rotary encoder TBA36
6 Pages
-
Rotary encoder TKA60
2 Pages
-
Rotary encoder TKN46 manual
22 Pages
-
Rotary encoder TKN46
7 Pages