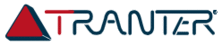

Catalog excerpts
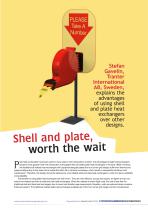
Stefan Gavelin, Tranter International AB, Sweden, explains the advantages of using shell and plate heat exchangers over other designs. Shell and plate, worth the wait P late heat exchangers have been used for many years in the hydrocarbon industry. The advantages of plate heat exchangers became more apparent with the introduction of the gasket free all welded plate heat exchangers in the early 1990s. However, the traditional all welded heat exchangers with square/rectangular plates (the four corner grid design) suffer from thermal and pressure fatigue due to the weak corner welds that often fail in dynamic processes, which results in unexpected shutdown and maintenance. Therefore, this design should be replaced by more reliable shell and plate heat exchangers in order to improve reliability and availability. The benefits of using plate heat exchangers are well known. They are more efficient, occupy less space, are lighter and do not need to be cleaned as often as shell and tube heat exchangers. When the material is exotic (high cost), the cost is less than for traditional shell and tube heat exchangers due to lower heat transfer area requirements; therefore, costs are reduced where corrosive fluids are present. The traditional welded plate heat exchangers available are of the four corner grid design and are manufactured Reprinted from September2009 HydrocarbonEngineering
Open the catalog to page 1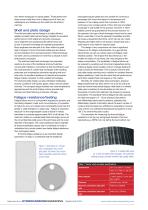
from either rectangular or square plates. These plates have sharp corner welds that, from a fatigue point of view, are catastrophic and insidious as the welds can fail without warning. Shell and plate design The shell and plate heat exchanger is a highly efficient, reliable compact plate heat exchanger. Despite the excellent performance in both stable and dynamic processes, many engineers are questioning the performance due to lack of product knowledge and operating experience. Many engineers are reluctant to try them without a great deal of support in terms of process references and actual...
Open the catalog to page 2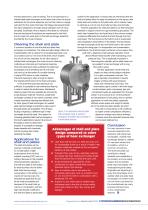
the test specimen to use for testing. This is not practical for a welded plate heat exchanger as the tests must show the actual resistance for the whole assembly and not the metal or a single weld joint for the metal. Normally, the fatigue test experimental test rig is designed to simulate actual operation (one of many samples). Essentially what is tested is the ability to withstand thermal mechanical fluctuations as experienced in the field, and to locate the weak point in the heat exchanger assembly and identify the mode of failure. suited for the application. It should also be mentioned...
Open the catalog to page 3All Tranter catalogs and technical brochures
Archived catalogs
-
SUPERCHANGER®
28 Pages
-
Thermofit
4 Pages
-
Parts & Service Brochure
6 Pages
-
Company Brochure English
8 Pages
-
Oil & Gas brochure English
8 Pages
-
Service English
8 Pages
-
Gasketed PHE English
8 Pages
-
Product Brochure English
8 Pages
-
Prime Surface Heat Exchangers
10 Pages