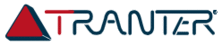

Catalog excerpts
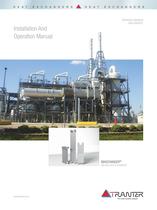
HEAT EXCHANGERS A HEAT EXCHANGERS Technical Literature The heat transfer people
Open the catalog to page 1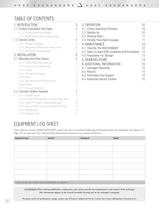
1.1. Product Description And Types 3 1.2.2. Maximum Differential Temperatures 4 1.2.3. Flow Rate Considerations 4 2.1. Mounting And Flow Control 5 2.2. Common System Hookups 7 2.2.2. Process Fluid Heating-Constant Flow Rate 2.2.3. Steam Or Vapor Condensing/Liquid 8 2.2.4. Process Fluid Heating-Variable Flow Rate 8 3.1. Critical Operating Principles 10 3.4. Periodic Flow Rate Increases 11 4.2. Clean-in-place (CIP) Guidelines And Procedures 12 6.4. Authorized Service Centers 15 Upon delivery of your MAXCHANGER® unit(s), be sure to record the following information from the nameplate (see...
Open the catalog to page 2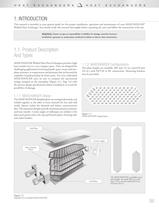
HEAT EXCHANGERS ¿\ HEAT EXCHANGERS This manual is intended as your general guide for the proper installation, operation and maintenance of your MAXCHANGER5 Welded Heat Exchanger. You should study this manual thoroughly before operating the unit and follow the instructions with care. WARNING: Tranter accepts no responsibility or liability for damage caused by incorrect installation, operation or maintenance attributed to failure to observe these instructions. MAXCHANGER Welded Plate Heat Exchangers provide a high heat transfer rate in a very compact space. They are designed for challenging...
Open the catalog to page 3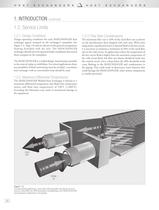
HEAT EXCHANGERS ¿\ HEAT EXCHANGERS Design operating conditions for each MAXCHANGER heat exchanger appear stamped on the exchangers nameplate (see Figure 5.2., Page 14) and are shown on the general arrangement drawing furnished with the unit. The MAXCHANGER exchanger should never be operated under conditions that exceed those stamped on the nameplate. The MAXCHANGER is a welded design. Intermixing is possible in the event of a plate or weld failure. For critical applications where any possibility of fluid intermixing must be avoided, a secondary heat exchanger with an intermediate loop...
Open the catalog to page 4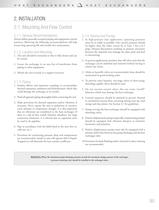
HEAT EXCHANGERS ¿\ HEAT EXCHANGERS 2.1. Mounting And Flow Control Always follow generally accepted piping and equipment control practices. Observing the following recommendations will help ensure long operating life and trouble-free maintenance. 1. The unit should be mounted so that it fully drains and can 2. Locate the exchanger in an area free of interference from piping or other equipment. 3. Mount the unit securely to a support structure. 1. Employ elbows and expansion couplings to accommodate thermal expansion, pulsation and hydrodynamic shock that could damage the exchanger or its...
Open the catalog to page 5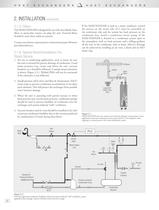
The MAXCHANGER is designed for use with clean fluids; thus, fibers or particulate matter can plug the unit. External filters should be used when solids are present. Contact your factory representative to determine proper filtration Steam Service 1. For use in condensing applications, such as steam, be sure the unit is oriented for gravity drainage of condensate. Good steam practices (e.g., steam trap below the unit, vacuum breakers, etc.) should be followed. A sample steam schematic is shown (Figure 2.2.). Welded PHEs will not be warranted 2. Install pressure relief valves and float &...
Open the catalog to page 6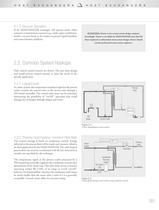
HEAT EXCHANGERS ¿\ HEAT EXCHANGERS If the MAXCHANGER exchanger will operate under either constant or intermittent vacuum (e.g., under upset conditions), install a vacuum break at the outlets to prevent liquid backflow and water hammer problems. ATTENTION: Tranter is not a steam system design company. Accordingly, Tranter is not liable for MAXCHANGER units that fail when employed in substandard steam system designs. Buyers should consult professional steam system engineers. 2.2. Common System Hookups Only typical control systems are shown. The user must design and install process control...
Open the catalog to page 7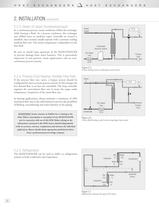
2.2.3. Steam Or Vapor Condensing/Liquid In a continuous process, steam condenses within the exchanger while heating a fluid. As a process condenser, the exchanger uses chilled water to condense vapor. Generally no control is installed, since systems usually operate with a constant cooling medium flow rate. The return temperature is dependent on the heat load. Be sure to install traps upstream of the MAXCHANGER to prevent damage from water hammer. This is particularly important in low-pressure steam applications and on non- continuous process systems. Recovery System A basic heating (steam...
Open the catalog to page 8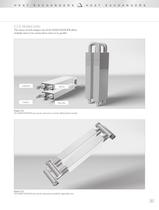
HEAT EXCHANGERS ¿\ HEAT EXCHANGERS The nature of and compact size of the MAXCHANGER allows multiple units to be connected in series or in parallel. Two MAXCHANGER units may be connected in series for additional heat transfer Two MAXCHANGER units may be connected in parallel for higher fiow rates.
Open the catalog to page 9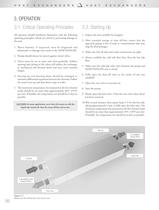
3.1. Critical Operating Principles 3.2. Starting Up All operators should familiarize themselves with the following operating principles, which are critical in preventing damage to 1. Water hammer, if suspected, must be diagnosed and eliminated, or damage may result to the MAXCHANGER. 2. Pumps should always be started against closed valves. 3. Valves must be set to open and close gradually. Sudden opening and closing of the valves will subject the exchanger to mechanical and thermal shock and may cause material 4. Starting up and shutting down should be managed to minimize differential...
Open the catalog to page 10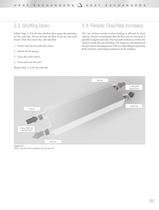
HEAT EXCHANGERS ¿\ HEAT EXCHANGERS 3.4. Periodic Flow Rate Increases Follow Steps 1—4 for the hot side first, then repeat the procedure for the cold side. Always decrease the flow to the hot side until closed. Then shut down the cold side flow. 1. Slowly close the hot side inlet valves. 3. Close the outlet valves. 4. Drain and vent the unit. Repeat Steps 1—4 for the cold side. The rate of heat transfer surface fouling is affected by fluid velocity. Tranter recommends that the flow rate be increased if possible at regular intervals. The increased turbulence within the channel retards the...
Open the catalog to page 11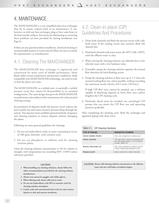
HEAT EXCHANGERS The MAXCHANGER is a very simplified plate heat exchanger that, by its nature, requires little or no maintenance. It can, however, as with any heat exchanger, plug or have scale form on the heat transfer surfaces. Provisions for eliminating or correcting these problems are best provided for during installation (see If there are any questions about installation, chemical cleaning or recommended strainer or screen sizes for filters, be sure to consult HEAT EXCHANGERS 1. Drain both channels and flush the process circuit with cold, fresh water. If the cooling circuit uses...
Open the catalog to page 12All Tranter catalogs and technical brochures
Archived catalogs
-
Shell-and-Plate
3 Pages
-
SUPERCHANGER®
28 Pages
-
Thermofit
4 Pages
-
Parts & Service Brochure
6 Pages
-
Company Brochure English
8 Pages
-
Oil & Gas brochure English
8 Pages
-
Service English
8 Pages
-
Gasketed PHE English
8 Pages
-
Product Brochure English
8 Pages
-
Prime Surface Heat Exchangers
10 Pages