
Catalog excerpts
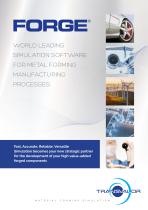
FORGE WORLD LEADING SIMULATION SOFTWARE FOR METAL FORMING MANUFACTURING PROCESSES Fast, Accurate, Reliable, Versatile Simulation becomes your new strategic partner for the development of your high value-added forged components
Open the catalog to page 1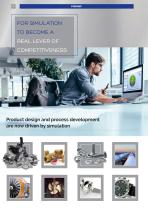
FOR SIMULATION TO BECOME A REAL LEVER OF COMPETITIVENESS Product design and process development are now driven by simulation
Open the catalog to page 2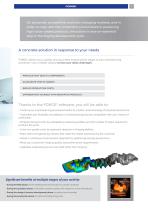
On extremely competitive and ever-changing markets, and in order to cope with the constraints encountered in producing high value-added products, simulation is now an essential step in the forging development cycle. A concrete solution in response to your needs FORGE® allows you to quickly and accurately analyze all the stages of your manufacturing processes. Use a reliable solution to face your daily challenges: PRODUCE HIGH-QUALITY COMPONENTS, ACCELERATE TIME TO MARKET, REDUCE PRODUCTION COSTS, DIFFERENTIATE YOURSELF WITH INNOVATIVE PRODUCTS Thanks to the FORGE® software, you will be able...
Open the catalog to page 3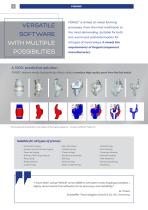
FORGE® is aimed at metal forming VERSATILE SOFTWARE WITH MULTIPLE POSSIBILITIES processes, from the most traditional to the most demanding. Suitable for both hot, warm and cold deformation for all types of metal alloys, it meets the requirements of forged component manufacturers. A 100% predictive solution FORGE® delivers results that perfectly reflect reality to produce high-quality parts from the first batch! Precise geometry prediction at all stages of the forging sequence - Courtesy of Bharat Forge Ltd Suitable for all types of process • Closed die forging • Ferrous and non-ferrous...
Open the catalog to page 4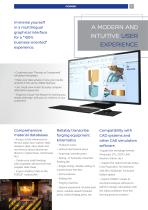
Immerse yourself in a multilingual graphical interface for a “100% business-oriented” experience. A MODERN AND INTUITIVE USER EXPERIENCE • Customize your “Process or Component” simulation templates • Make your data setups or view your results anytime in the same unified interface • Use “multi-view mode” to easily compare alternative sequences • “Export to Cloud”: the feature for sharing your results internally, with your co-workers or your customers Comprehensive material databases • Access +1000 references for ferrous alloys (low-carbon steel, stainless steel, alloy steel) and non-ferrous...
Open the catalog to page 5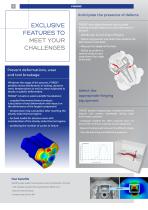
Anticipate the presence of defects EXCLUSIVE FEATURES TO MEET YOUR CHALLENGES FORGE® has unique features such as point tracking to easily detect any cold-shut areas in the part. • Identify laps at each stage of forging • Follow progression and determine whether the fold moves to the flash • Measure the depth of the fold • Ability to perform a reverse analysis and understand the origin of the fold Prevent deformations, wear and tool breakage Whatever the stage of the process, FORGE® predicts stress distributions in tooling, abrasive wear, temperatures as well as areas subjected to elastic or...
Open the catalog to page 6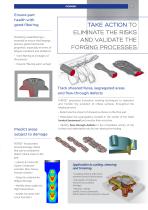
Predicting metal fibering is essential to ensure that forgings possess good mechanical properties, especially in terms of fatigue resistance and resilience. • View fibering at all stages of the process • Prevent “fibering exits” as flash Predict areas subject to damage FORGE® incorporates several damage criteria that can be enabled to detect critical areas on the part. • Latham & Cockcroft, Oyane, Chaboche-Lemaitre, Rice-Tracey fracture criterion • Dang Van criterion for fatigue damage • Identify areas subject to high triaxial stress • Isolate risk areas with crack formation ELIMI AN FORGI...
Open the catalog to page 7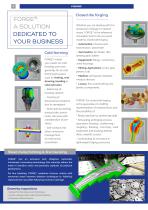
Closed die forging Cold forming FORGE® meets your needs for cold heading and more generally for all cold forming processes such as riveting, wire drawing, heading or cold extrusion. • Balancing of heading stations • Tracking of dimensional variations due to springback • Multi-domain tooling analysis (die, punch, insert, die case) with consideration of prestress • Self-contact and stress resistance management of mechanical assemblies Whether you are dealing with the production of large or medium series, FORGE® is the reference simulation tool for all your parts made by closed die forging. •...
Open the catalog to page 8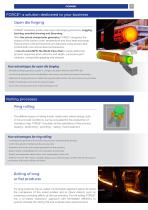
FORGE®: a solution dedicated to your business Open die forging FORGE® simulates all the main open die forging processes: cogging, becking, mandrel drawing and blooming. With the actual manipulator geometry, FORGE® integrates the impact of the contact zone, temperature and local heat exchange. Passes below critical thresholds are detected using sensors that control both core and surface temperatures. A one of a kind MPFx file (Multi-Pass-File) to easily define the process sequence (pass advance and depth, successive part rotations, manipulator gripping and release). Your advantages for open...
Open the catalog to page 9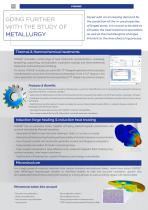
Faced with an increasing demand for the prediction of the in-use properties of forged parts, it is crucial to be able to simulate the heat treatment operations as well as the metallurgical changes inherent to the manufacturing process. FORGE® simulates a wide range of heat treatments (austenitization, annealing, tempering, quenching, normalization, controlled cooling) and thermochemical treatments (carburizing and nitriding). For steels, FORGE® includes an automatic TTT diagram generator that calculates transformation curves from the chemical composition. From a CCT diagram, this same...
Open the catalog to page 10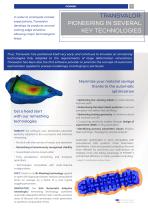
TRANSVALOR: PIONEERING IN SEVERAL KEY TECHNOLOGIES In order to anticipate market expectations, Transvalor develops its products around cutting-edge solutions allowing major technological leaps. Thus, Transvalor has positioned itself very early and continues to innovate on remeshing technologies fully adapted to the requirements of large deformation simulations. Transvalor has been also the first software provider to promote the concept of automatic optimization applied to process modellings, and forging in particular. Maximize your material savings thanks to the automatic optimization •...
Open the catalog to page 11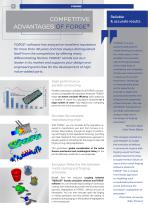
Computation Time COMPETITIVE ADVANTAGES OF FORGE FORGE® software has enjoyed an excellent reputation for more than 30 years and has always distinguished itself from the competition by offering many differentiating factors. FORGE® stands out as a leader in its market and supports your design and engineering activities for the development of high value-added parts. High performance parallel computing Reliable & accurate results ParaLLeLcomputing is avaiLabLe for aLL FORGE® process-esand is compatible withaLLoptions. Moreover, FORGE® keeps an almost constant efficiency (ratio speed-up vs...
Open the catalog to page 12All TRANSVALOR S.A. catalogs and technical brochures
-
TRANSWELD 1.0
2 Pages
-
DIGIMU 3.0
2 Pages
-
REM3D
8 Pages
-
COLDFORM®
8 Pages
-
CADdoctor
2 Pages
-
medical
1 Pages
-
FORGE_Aero
16 Pages
-
FORGE-Auto
12 Pages