
Catalog excerpts
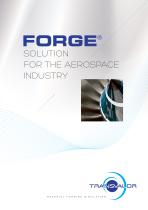
SOLUTION FOR THE AEROSPACE INDUSTRY
Open the catalog to page 1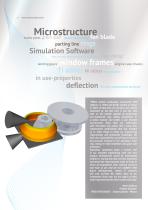
Microstructure blade grain size fan screw press counter blow hammer parting line Simulation Software feed control mandrel and main roll piloting landing gears ring rolling window frames engine case chassis deflection thermo-mechanical analysis “FRISA started evaluating commercial FEA software in 2004 and finally landed on Forge in 2005. At that time our decision was mainly motivated by the fact that it was the only code on the market capable of performing non-isothermal ring rolling simulations in a stable manner and within a user friendly environment. Since then our interaction with...
Open the catalog to page 2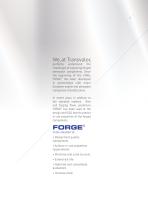
We, at Transvalor, perfectly understand the challenges of supplying forged aerospace components. Since the beginning of the 1980s, FORGE® has been developed in partnerships with major European engine and aerospace component manufacturers. In recent years, in addition to the standard material flow and forging flaws prediction, FORGE® has been used at the design and R&D level to predict in-use properties of the forged components. is the solution to: • Design best quality components • Achieve in-use properties requirements • Minimize real scale try-outs • Extend die life • Optimize and...
Open the catalog to page 3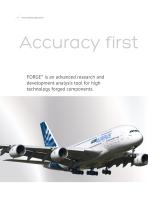
FORGE® is an advanced research and development analysis tool for high technology forged components.
Open the catalog to page 4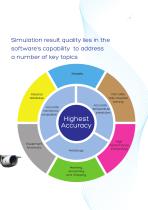
Material database Accurate mechanical computation Part-dies fully coupled solving Accurate temperature prediction Highest Accuracy Equipment kinematic High Performance Computing Meshing, remeshing and mapping
Open the catalog to page 5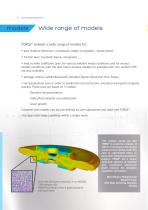
Wide range of models FORGE® embeds a wide range of models for: • part material behaviour: viscoplastic, elasto-viscoplastic, elasto-plastic • friction laws: Coulomb, Tresca, viscoplastic, … • heat transfer coefficient laws: for various ambient media conditions and for various contact conditions with the dies. More complex models, for example with non-uniform HTC, are also available. • damage criteria: Latham&Cockroft, Lemaître, Oyane, Shark skin, Rice Tracey… • recrystallization laws in order to predict the microstructure evolution during the complete process. These laws are based on 3...
Open the catalog to page 6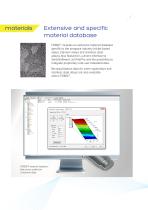
Extensive and specific material database FORGE® includes an extensive material database specific to the aeropace industry (nickel based alloys, titanium alloys and stainless steel alloys). Also featured is a direct interface to SenteSoftware Ltd JMatPro and the possibility to integrate proprietary end-user tabulated data. Recrystallization data for some superalloys and stainless steel alloys are also available within FORGE®. FORGE® material database: flow stress surface for a titanium alloy
Open the catalog to page 7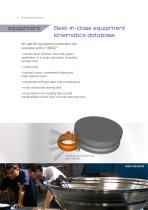
Best-in-class equipment kinematics database All specific equipment kinematics are available within FORGE®: • counter blow hammer with multi blows capabilities in a single simulation including waiting time • screw press • hydraulic press: isothermal forging and multi-speed presses • equipment stiffness taken into consideration • multi-directional moving dies • ring rolling mill including feed control mandrel/feed control main roll and centering rolls. Simulation of a profiled ring with FORGE® FRI
Open the catalog to page 8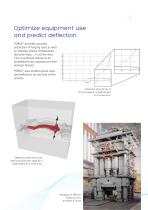
Optimize equipment use and predict deflection FORGE® provides accurate prediction of forging load, as well as stresses, strains, temperature, abrasive wear, … in all the dies. This is achieved thanks to an embedded fully coupled part-dies analysis feature. FORGE® also predicts press load and deflection at any time of the process. Prediction of xyz forces of finisher stage for a blade forged on a screw press Deflection prediction at the beginning of finisher stage for a blade forged on a screw press Interforge 65 000 ton hydraulic press © Aubert & Duv
Open the catalog to page 9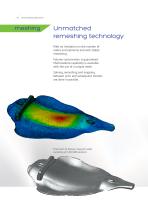
Unmatched remeshing technology With no limitation on the number of nodes and elements and with stable remeshing. Volume conservation is guaranteed. Multimaterial capability is available with the use of a unique mesh. Solving, remeshing and mapping between prior and subsequent meshes are done in parallel. Final mesh of Titanium alloy fan blade consisting of 1 030 000 elements
Open the catalog to page 10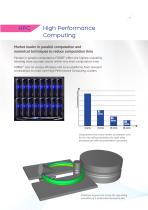
High Performance Computing Market leader in parallel computation and numerical techniques to reduce computation time Pioneer in parallel computation, FORGE® offers the highest scalability allowing more accurate results within very short computation time. Computation time FORGE® runs on various Windows and Linux platforms, from standard workstations to multi-core High Performance Computing clusters. Computation time versus number of computer cores for the ring rolling simulation of a super alloy aerospace part with recrystallization calculation. Prediction of grain size during the ring...
Open the catalog to page 11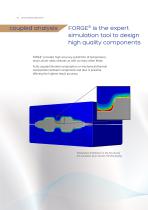
coupled analysis FORGE® is the expert simulation tool to design high quality components FORGE® provides high accuracy prediction of temperature, strain, strain rates, stresses as well as many other fields. Fully coupled thermal computation or mechanical/thermal computation between component and dies is possible offering the highest result accuracy. Temperature distribution in the dies during the simulation of an Inconel 718 disk forging
Open the catalog to page 12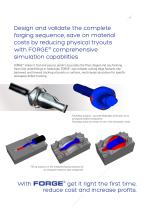
Design and validate the complete forging sequence, save on material costs by reducing physical tryouts with FORGE® comprehensive simulation capabilities FORGE® makes it fast and easy to predict accurately the final shaped and any forming flaws like underfillings or folds/laps. FORGE® also embeds cutting edge features like backward and forward tracking of points or surfaces, multi-body calculation for specific aerospace defect tracking. Folds/laps analysis : accurate folds/laps prediction on an aerospace preform component Folds/laps areas are shown in red in the simulation result. Fill-up...
Open the catalog to page 13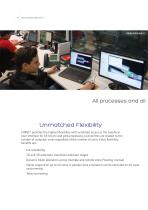
FRISA FORJADOS Unmatched Flexibility FORGE® provides the highest flexibility with unlimited access to the Graphical User Interface for 64-bit pre and post processing. License fees are related to the number of computer cores regardless of the number of users. Extra flexibility benefits are: Job scheduling 2D and 3D automatic transitions between stages Dynamic token allocation across multiple and remote sites (Floating License) Solver support for up to 64 cores in parallel (one simulation can be executed on 64 cores concurrently) Token borrowing
Open the catalog to page 14All TRANSVALOR S.A. catalogs and technical brochures
-
TRANSWELD 1.0
2 Pages
-
DIGIMU 3.0
2 Pages
-
FORGE
16 Pages
-
REM3D
8 Pages
-
COLDFORM®
8 Pages
-
CADdoctor
2 Pages
-
medical
1 Pages
-
FORGE-Auto
12 Pages