
Catalog excerpts
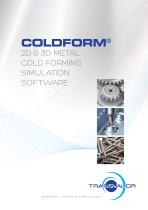
COLDFORM® 2D & 3D METAL COLD FORMING SIMULATION SOFTWARE
Open the catalog to page 1
A very broad application scope COLDFORM® meets the needs of industrialists in many fields: • design and manufacture of parts formed from sheets ranging in thickness from moderate to high (clockmaking, precision mechanics, etc.); • design and manufacture of assemblies: screws, nuts, bolts, washers, etc.; • design and manufacture of motor parts: shafts, gears, rings produced by ring rolling, cold-formed parts. Significant cost and productivity gains The benefits of COLDFORM® can be observed at all steps in your activity During the R&D phase, for the development of innovative or complex...
Open the catalog to page 3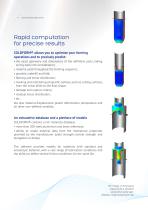
Rapid computation for precise results COLDFORM® allows you to optimize your forming operations and to precisely predict: • the exact geometry and dimensions of the definitive parts, taking spring-back into consideration; • material yield throughout the forming sequence; • possible underfill and fold; • fibering and stress distribution; • marking and monitoring of specific surfaces, such as cutting surfaces, from the initial billet to the final shape; • damage and rupture criteria; • residual stress distribution; • etc. but also material displacement, plastic deformation, temperature and all...
Open the catalog to page 4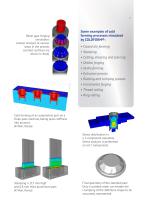
Bevel gear forging simulation: contact analysis at various steps in the process (contact surfaces are shown in blue). Cold forming of an automotive part on a three-pass machine, taking press stiffness into account. (K-Won, Korea) / 5 / Some examples of cold forming processes simulated by COLDFORM®: • Closed die forming • Stamping • Cutting, shearing and piercing • Orbital forging • Hydro forming • Extrusion process • Riveting and crimping process • Incremental forging • Thread rolling • Ring rolling Stress distribution in a 7-component assembly. Stress analysis is performed on all 7...
Open the catalog to page 5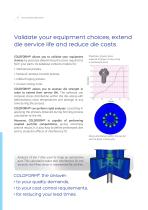
Validate your equipment choices, extend die service life and reduce die costs COLDFORM® allows you to validate your equipment choices by precisely determining the press required to form your parts. Its database contains models for: Prediction of press force required to forge a screw using a mechanical press • mechanical presses, • hydraulic presses, knuckle presses, • orbital forging presses, • circular rolling mills. COLDFORM® allows you to analyze die strength in order to extend their service life. The software can compute stress distribution within the die, along with deformations, wear,...
Open the catalog to page 6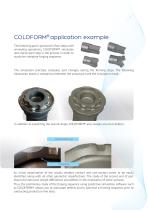
COLDFORM® application example The following part is produced in four steps, with annealing operations. COLDFORM® simulates and chains each step in the process in order to study the complete forging sequence. The simulation precisely computes part changes during the forming steps. The following illustration shows a comparison between the actual part and the simulation result. In addition to predicting the overall shape, COLDFORM® also reveals any local defects. Elliptical contact area S-shaped line An initial examination of the results enables contact and non-contact zones to be easily...
Open the catalog to page 7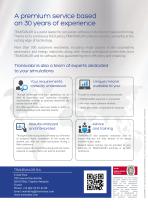
A premium service based on 30 years of experience TRANSVALOR is a world leader for simulation software in the field of material forming. Thanks to its continuous R&D policy, TRANSVALOR software remains constantly at the cutting edge of technology. More than 500 customers worldwide, including major players in the automotive, aeronautics and energy industries, along with several prestigious universities, trust TRANSVALOR and its software, thus guaranteeing their efficiency and reliability. Transvalor is also a team of experts dedicated to your simulations Through exchanges with your...
Open the catalog to page 8All TRANSVALOR S.A. catalogs and technical brochures
-
TRANSWELD 1.0
2 Pages
-
DIGIMU 3.0
2 Pages
-
FORGE
16 Pages
-
REM3D
8 Pages
-
CADdoctor
2 Pages
-
medical
1 Pages
-
FORGE_Aero
16 Pages
-
FORGE-Auto
12 Pages