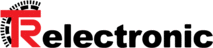
Group: TR-Gruppe
Catalog excerpts
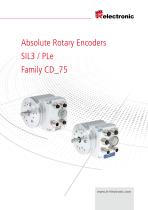
Absolute Rotary Encoders SIL3 / PLe Family CD_75
Open the catalog to page 1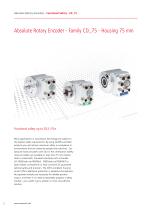
Absolute Rotary Encoders - Functional Safety - CD_75 Absolute Rotary Encoder - Family CD_75 - Housing 75 mm Functional safety up to SIL3 / PLe Many applications in automation technology are subject to the highest safety requirements. By using SIL3/PLe-certified products you will achieve maximum safety in workplaces or environments that are shared by people and machines. Our absolute rotary encoders with SIL3 or PLe certification (safety rotary encoders) are available in sizes from 75 mm (hollow shaft or solid shaft). Standard interfaces such as Double SSI, PROFIsafe via PROFIBUS, PROFIsafe...
Open the catalog to page 2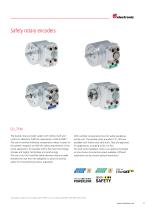
Safety rotary encoders CD_75 M The double rotary encoder system with hollow shaft and multi-turn detection fulfill the requirement of EN 615081*. The use of certified individual components makes it easier for the system integrator to fulfill the safety requirements of the entire application, for example within the event technology, storage and logistic technology and wind energy. The use of our SIL 3-certified safety absolute rotary encoder liberates the user from the obligation to prove functional safety for this positioning sensor separately. With certified components the strict safety...
Open the catalog to page 3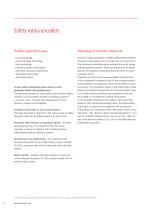
Safety rotary encoders Possible application areas Advantage of certified components _ crane technology _ event and stage technology _ drive technology _ conveying systems and logistics _ machinery and plant engineering _ automation technology _ wind energy plant The basic safety standard IEC 615082 differentiates between measures to eliminate errors and measures to control errors. The measures to eliminate errors embrace the entire design and development process. These are required for the development of individual components and they serve to avoid systematic errors. Important for error...
Open the catalog to page 4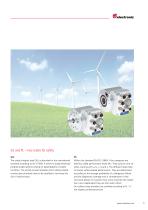
The safety integrity level (SIL) is described in the international standard according to IEC 61508. It serves to judge electrical/ programmable systems relying on dependability of safety functions. The aimed-at level indicates which safety-related construction principals have to be satisfied to minimize the risk of malfunctions. Within the standard EN ISO 13849-1 five categories are defined, called performance levels (PL). They build on one another, starting with a, b, c, d and e. The different levels help to classify safety-related performance. They are determined according to the average...
Open the catalog to page 5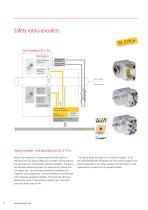
Safety rotary encoders SIL 3 / PL Safe accroding to SIL 3 / PLe Power supply Main system Magnetical detection multi turn Incremental interface or Sine / Cosine interface Optical detection single turn Power supply Position value main system Magnetical detection multi turn Position value safety system Magnetical detection single turn Safety system Cross validation determining speed safety bus-protocol Standard protocol safe (yellow) and not safe protocol part PROFIsafe / openSAFETY "gray channel" = safe data within an unsafe medium Rotary encoder, safe according to SIL 3 / PL e Within the...
Open the catalog to page 6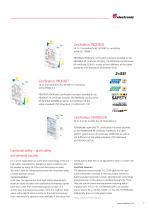
Certification, PROFIBUS SIL CL 3 according to IEC 61508 PL e according to EN ISO 13849-1 PROFIBUS / PROFIsafe: certification has been awarded to the PROFIBUS (PI certificate Z01522), the PROFIsafe conformance (PI certificate Z20031) as well as the fulfillment of the safety standards (TÜV Rheinland, 01/205/5015/10). 2×SSI Certification, PROFINET SIL CL 3 according to IEC 61508 PL e according to EN 61800-5-2 PROFINET / PROFIsafe: certification has been awarded to the PROFINET (PI certificate Z10472), the PROFIsafe conformance (PI-Zertifikat Z20068) as well as the fulfillment of the safety...
Open the catalog to page 7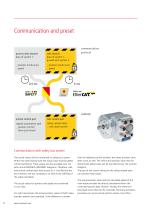
process data channel data of system 1: position (multi-turn) speed © v^ 0.5 ms open i ■i SAFETY safe channel data of system 1, proved with system 2 _ position (multi-turn) _ speed communication protocol Safety over controls normal control part regular automation task: _ position control (few cycle times) safe control part safety-related tasks: _ safe data transfer Communication with safety bus system The actual values will be transferred via safety bus system. Within the safe protocol part the actual value and the speed will be transferred. These values are also available over not safe...
Open the catalog to page 8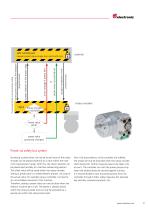
Controller safe control part preset process preset value successfully set error message if preset fails accepts takeover of the preset value requests preset writes preset value into the telegram *Functional Safety Communication Profile newest preset value single-turn and multi-turn Rotary rotary encoder encoder *FSCP Rotary encoder in standstill? Preset value value? preset value sucessfully changed Preset via safety bus system By setting a preset value, the actual issued value of the rotary encoder can be placed arbitrarily at a value within the maximum measurement range. With this, the...
Open the catalog to page 9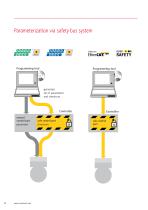
Programming tool normal control part parameter safe control part checksum
Open the catalog to page 10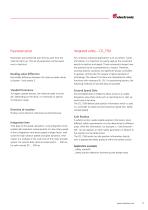
Parameters are transferred over the bus each time the machine starts up. This set of parameters will be saved over a checksum: For numerous industrial applications such as presses, cranes and robots, it is important to exactly capture the movement exactly in position and speed. These movements always have the potential to be accompanied by a hazard. Therefore, working stations, positions and speed are always controlled. In general, controls like this require a higher standard of technology. The relevant functions are interpreted as safety functions with necessary SIL / PL. For positioning...
Open the catalog to page 11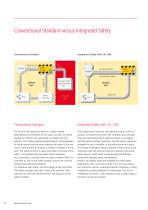
Conventional Standard versus Integrated Safety Conventional Standard Integrated Safety with CD_75M Safety Safety module module I/O I/O fieldbus fieldbus encoder encoder safe bus protocol safe bus protocol Safety Safety control control drive drive safety safety interface interface programmable programmable logic controller logic controller (PLC) (PLC) unchecked unchecked area area shaft shaft checked checked area area shaft shaft safe position // speed safe position speed checked checked area area digital I/O digital drive drive Conventional Standard The tests of the signals are done in a...
Open the catalog to page 12All TR-Electronic GmbH catalogs and technical brochures
-
USB PC-Adapter HID V5
2 Pages
-
BQS 224 Sensor
2 Pages
-
BQS–Drill Quality Assurance
6 Pages
-
Absolute-Encoder CMV22 - A,
4 Pages
-
Sensor Highlights 2018
12 Pages
-
Wire Actuated Encoders Overview
48 Pages
-
Product Information BQS
12 Pages
-
Flyer Automation/Retrofit
12 Pages
-
Laser distance measurement
24 Pages
-
The catalog
562 Pages
-
Overview Linear Encoders
48 Pages
-
Intelligent drive technology
44 Pages
Archived catalogs
-
TRgroup
12 Pages
-
Industrial Ethernet
16 Pages
-
Profinet
4 Pages