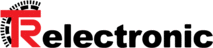
Group: TR-Gruppe
Catalog excerpts
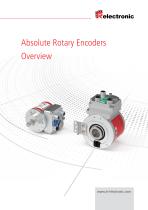
Absolute Rotary Encoders Overview
Open the catalog to page 1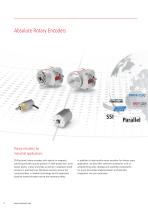
Absolute Rotary Encoders Rotary encoders for industrial applications TR-Electronic rotary encoders with optical or magnetic scanning precisely acquire position in steel production, wind power plants, cranes and ships as well as in explosion-proof versions in painting lines. Miniature versions ensure the correct position in medical technology and SIL-approved absolute rotary encoders ensure the necessary safety. In addition to high-quality rotary encoders for almost every application, we also offer extensive accessories such as programming tools, displays and assembly components for quick...
Open the catalog to page 2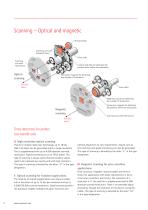
Scanning unit with Hall sensors ' Optical scanning Position value Scanning unit with optoelectronics ' Central code disk for detecting the - position from within the revolutions Permanent magnets for detecting the number of revolutions Drive shaft Magnetic sources for detecting the number of revolutions '':;g --i \ \ optimal adjustment to new requirements. Signals such as limit switches and speed monitoring can also be generated. This type of scanning is denoted by the letter "E" in the type designation. M Magnetic scanning for price-sensitive applications Price-conscious, magnetic rotary...
Open the catalog to page 4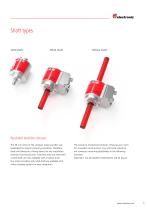
Shaft types Solid shaft Blind shaft Hollow shaft Persistent machine concept The 58 mm series of the compact rotary encoder was developed for diverse mounting variations. Therefore, there will always be a fitting device for any installation situation that should arise. Functions that you need with a solid shaft, are also available with a hollow shaft. Our rotary encoders with solid shaft are available with many coupling options for easy integration. The variety of mechanical solutions enhances your room for innovative constructions. You will find a sample of the numerous mounting...
Open the catalog to page 5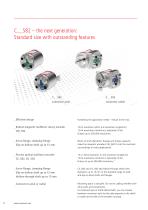
C__582 – the next generation: Standard size with outstanding features connector axial connector radial _ Efficient design _ Robust magnetic multiturn rotary encoder CM_582 13 bit resolution within one revolution (singleturn) 12 bit revolutions (multiturn), optionally 16 bit. Output up to 256,000 revolutions. _ Servo flange, clamping flange Slip-on hollow shaft up to 15 mm Plenty of shaft diameters, flanges and torque supports make the magnetic encoders CM_582 fit into the mechanic surroundings of many applications. _ Precise optical multiturn encoder CE_582, CO_582 15 or 18 bit resolution...
Open the catalog to page 6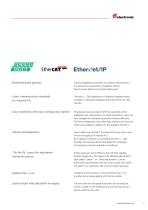
_ Parameterizable gearbox Fractional gearbox parameters (numerator / denominator) for almost any reproduction of gearbox factors. Also for exact detection of closed rotary axes. _ Latest communication standards for Industry 4.0 The new C_ _582 generation of industrial standard rotary encoders is rigorously equipped with state-of-the-art chip families. _ Easy installation with open configuration options TR absolute rotary encoders fulfill the standards of the respective user organizations for parameterization. Users can thus navigate the standard parameters without difficulty. The free...
Open the catalog to page 7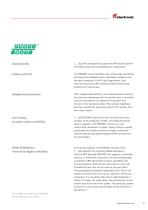
C_ _582 EPN consequently supports the EPN-Encoder profile of Profibus International standardisation organisation. The PROFINET variant therefore uses cutting-edge technology with long-term availability and is absolutely compliant with the latest standards of the PI User Organization. Realtime synchronization (IRT) enables precisely synchronized positioning of several axes. _ Neighborhood detection With neighborhood detecion, you exchange devices without the use of an engineering tool. An encoder that is connected newly to the network can determine his position and function in the network by...
Open the catalog to page 9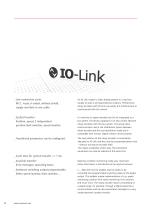
_ Low connection costs: M12, 4-pin, A-coded, without shield, supply and data in one cable. An IO-Link master is often already present in a machine, usually to read in and parameterize initiators. TR-Electronic rotary encoders with IO-Link use exactly this infrastructure to communicate with the control. _ Cyclical transfer: Position, speed, 2 independent position limit switches, speed monitor. If a machine or system already has IO-Link integrated as a bus system, the obvious approach is to also control absolute rotary encoders with this bus system. The actual value communication uses a star...
Open the catalog to page 10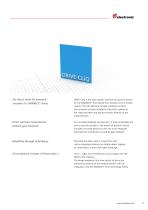
_ The direct route for mounted encoders to SINAMICS© drives. DRIVE-CLiQ is the open system interface for position sensors for the SINAMICS© drive family from Siemens AG for motion control. This fast absolute encoder interface connects the converter centrally installed in the switch cabinet to the rotary encoders and position sensors directly on the respective axes. _ Direct position measurement without gear backlash For increased reliability and precision, it may be desirable not only to use the encoder in the motor for position control. Encoders mounted directly on the axis to be measured...
Open the catalog to page 11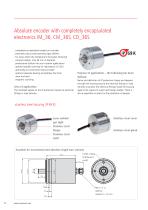
Absolute encoder with completely encapsulated electronics IM_36, CM_36S, CD_36S _ completely encapsulated single-turn encoder _ extremely robust and extremely tight (IP 69 K) _ for areas where the temperature fluctuates (thawing) _ compact design, only 36 mm in diameter _ professional solution for your outdoor applications _ optional double scanning for redundancy (2 × SSI) _ optionally as incremental rotary encoder _ optional separate bearing (completely free from wear and tear) _ magnetic scanning Area of application This standard applies to the IP protection classes for electrical...
Open the catalog to page 12
Safety rotary encoders Possible application areas Advantage of certified components _ crane technology _ event and stage technology _ drive technology _ conveying systems and logistics _ machinery and plant engineering _ automation technology _ wind energy plant The basic safety standard IEC 615082 differentiates between measures to eliminate errors and measures to control errors. The measures to eliminate errors embrace the entire design and development process. These are required for the development of individual components and they serve to avoid systematic errors. Important for error...
Open the catalog to page 13All TR-Electronic GmbH catalogs and technical brochures
-
USB PC-Adapter HID V5
2 Pages
-
BQS 224 Sensor
2 Pages
-
BQS–Drill Quality Assurance
6 Pages
-
Absolute-Encoder CMV22 - A,
4 Pages
-
Sensor Highlights 2018
12 Pages
-
Wire Actuated Encoders Overview
48 Pages
-
Product Information BQS
12 Pages
-
Flyer Automation/Retrofit
12 Pages
-
Laser distance measurement
24 Pages
-
The catalog
562 Pages
-
Overview Linear Encoders
48 Pages
-
Intelligent drive technology
44 Pages
Archived catalogs
-
TRgroup
12 Pages
-
Industrial Ethernet
16 Pages
-
Profinet
4 Pages