

Catalog excerpts
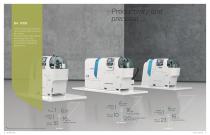
precision The BA 1008 range comprises ultra-compact, high-precision bar millers. Thanks to their multi-spindle S technology, these fast and powerful machining centres deliver impressive productivity. Number of rotating axes Linear axes Linear axes Number of rotating axes iximum diameter Number of rotating axes Linear axes iaximum diameter maximum diameter Positioning B axis: option/Continuous B axis (5 simultaneous axes): option
Open the catalog to page 2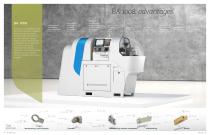
BA 1008 Based on the SwissNano, the BA 1008 is an ultra-compact, high-precision bar miller. The BA 1008 is fed with bars via the machine, using a divider system which allows workpieces up to a diameter of 16 mm to be loaded. Positioned machining operations and interpolation between the tool systems and the workpiece are easily possible. Machining area enclosed in a retractable bubble Multi-spindle machining for maximum productivity Different configurations possible depending on the workpiece requirements lj'-■ :::: Ultra-compact, footprint of just Material fed from bar or coil from...
Open the catalog to page 3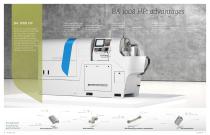
Multi-spindle technology identical to the BA 1008 with through-spindle cooling (120 bar) Based on the same design as the BA 1008, the BA 1008 HP is an ultra-compact bar miller equipped with multi-spindle technology and a high-pressure unit for through-spindle cooling. The BA 1008 HP is a flexible, compact, precise and efficient production tool. Fine filtration and transfer tray, can be replaced during operation Machining area housing for optimal recovery of precious materials Container with highpressure unit and optimal management of fluids and chips Exceptional machining performance Access...
Open the catalog to page 4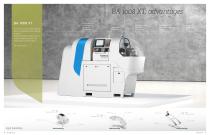
BA 1008 XT: advantages In the XT version, the BA 1008 has an integrated tool-change solution. This key asset enables increasingly complex parts to be produced in record time! rrrrrrr 316L stainless steel High feasibility Watchmaking
Open the catalog to page 5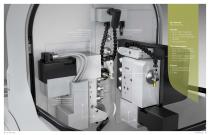
Bar diameter Max. Ø 16 mm Counter-operation spindle block Used to machine the last face Up to 2 HF spindles Divider clamping 2 clamping systems available: – F22 collet clamping – Parallel jaw clamping Pickup collet or pickup vice Front spindle block Mounted on an X, Y, Z slide Up to 4 front spindles Tilt option up to 17° Lateral spindle block Mounted on a U, V slide Up to 3 front spindles 80-mm sectioning option Spindles • Up to 4 front spindles • Up to 3 lateral spindles • Up to 2 counter-operation spindles • 1 sectioning tool Tool measurement • Tool measuring system built into the...
Open the catalog to page 6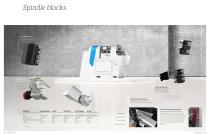
Spindle blocks Counter-operation spindle block Used to machine the last face Up to 2 HF spindles Front spindle block Mounted on an X, Y, Z slide Up to 4 front spindles Tilt option up to 17° 6-position tool changer for lateral spindle (BA 1008 XT) 10-position tool changer for front spindle (BA 1008 XT) Lateral spindle block Mounted on a U, V slide Up to 3 front spindles 80-mm sectioning option Inclined front spindle block Adjustment angle from 0° to 17° Manual, pneumatic or NC motor control Type Mechanical High frequency High frequency High frequency High frequency Speed (rpm) 12,000 28,000...
Open the catalog to page 7
Large tray with continuous thermostabilisation Mechanical design The heart of each machine The kinematic structure was designed for exemplary balance and thermal management. The axes and cast iron members are aligned symmetrically to the clamping spindle, and the thermal aspects are managed by ‘mini-loops’ that prevent heat propagation. The structure is anchored on three damped points. What about the results? Rigidity and vibration stability reach new peaks. Consequently, machining precision and quality are everything that they should be. The filter bags and their filtration fineness can be...
Open the catalog to page 8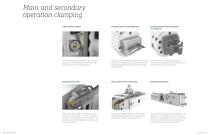
Main and secondary operation clamping Collet clamping system Used to machine profiled bars (saves on material); Ideal for machining precious materials; Better bar positioning; Allows several bars to be machined simultaneously. Tornos draws on its expertise to develop customised solutions to suit your requirements for machining more complex parts. Standard pickup collet Pickup collet for thin workpieces Reinforced pickup vice The pickup collet clamps the workpiece for sec tioning, and can be used to move the work iece p to the counter-operation spindles and eject it. It is possible to...
Open the catalog to page 9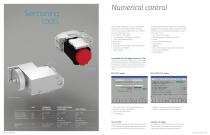
Numerical control Sectioning tools The BA 1008 machining centre is equipped as standard with the Fanuc 0iMD numerical control, renowned worldwide for its reliability, precision and ease of use. • 10.4” colour LCD screen • 512 kB memory (scalable up to 8 MB) • Up to 4 simultaneous axes • Data server • Ethernet • Al control contour mode (up to 200 blocks) • Electronic handwheel • Rigid tapping The BA 1008 machining centre can be optionally equipped with the Fanuc 0iMF numerical control allowing dual-channel programming for impro ved productivity. • 10.4” colour LCD screen • 512 kB memory...
Open the catalog to page 10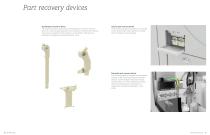
Part recovery devices Standard part recovery device Vacuum part recovery device The counter-operation collet places the finished part in the part recovery device. It is then conveyed by gravity into a basket on the side of the machine that can be accessed when the machine is in production. This system is designed for workpieces measuring less than 4 mm. With the Vacuum option, the parts are extracted via the Venturi effect and collected in a basket with an oil bath to avoid marking. Pneumatic part recovery device This recovery system is mounted on a pneumatic cylinder. At the end of...
Open the catalog to page 11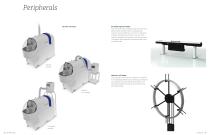
Peripherals Oil mist extractor BA 1008 material Feeder The bar feeder has a loading capacity of 650 mm, which allows the BA 1008 to automatically machine around fifty bars of 12 mm in diameter. It allows the production tool to run 24/7, with the least possible intervention from the operator. This option fully optimises the production costs of the BA 1008. Central suction Material coil Feeder The material is fed into the machine in coil form. A coil weighing between 30 and 80 kg is unwound by a dispenser on the side of the machine. The material is pulled through the machine by the wire feed...
Open the catalog to page 12All TORNOS catalogs and technical brochures
-
BA 1008 HP
17 Pages
-
TISIS
16 Pages
-
Swiss GT
24 Pages
-
EvoDECO
15 Pages
-
SwissDECO
4 Pages
-
SwissNano
20 Pages
-
MultiSwiss
28 Pages
-
Swiss DT Range
13 Pages
Archived catalogs
-
CU 2007 / CU 3007
20 Pages
-
EvoDECO 20-32
12 Pages
-
EvoDECO 10-16
16 Pages
-
Swiss ST 26
16 Pages
-
CT 20
9 Pages
-
Robobar SBF
8 Pages
-
SAS 16.6
16 Pages
-
Brochure MultiSwiss 6x14
12 Pages
-
Brochure MultiSigma
16 Pages
-
Brochure Delta 38
4 Pages
-
Gamma 20
6 Pages
-
EvoDECO 20 / EvoDECo 32
12 Pages
-
MICRO 8/4 - MICRO 8/5
12 Pages
-
MICRO 7
8 Pages
-
SIGMA 20 / SIGMA 32
16 Pages
-
DECO 26a
16 Pages
-
DECO 20a
16 Pages
-
EvoDECO 10 / EvoDECo 16
20 Pages
-
TORNOS SOLUTIONS
20 Pages
-
bar feeder ROBOBAR MSF-832/6
8 Pages
-
Multi Spindle MULTIDECO 20/8b
20 Pages
-
Single SpindleDECO 7/10a
12 Pages
-
Product range
14 Pages