
Group: Top Seiko

Catalog excerpts
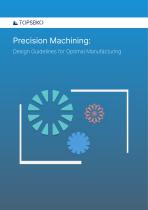
Precision Machining: Design Guidelines for Optimal Manufacturing
Open the catalog to page 1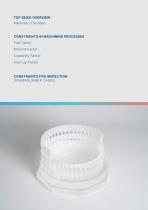
TOP SEIKO OVERVIEW Materials / Facilities Constraints in Machining Processes Tool Factor Material Factor Capability Factor Cost-Up Factor Constraints for inspection (Unmeasurable cases)
Open the catalog to page 2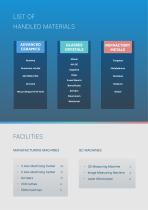
HANDLED MATERIALS ADVANCED Silicon 4H-SiC Sapphire Glass Fused Quartz Borosilicate Zerodur Clearceram Neoceram Aluminum nitride SiC/MMC/CMC Zirconia Macor/Shapal Hi M-Soft Molybdenum Tantalum Niobium Nickel FACILITIES MANUFACTURING MACHINES ・ ・ ・ ・ ・ 3 Axis Machining Center 5 Axis Machining Center Grinders CNC lathes EDM machines ・ 3D Measuring Machine 4 ・ Image Measuring Machine 3 ・ Laser
Open the catalog to page 3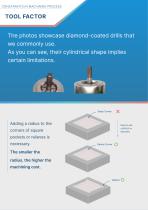
CONSTRAINTS IN MACHINING PROCESS TOOL FACTOR The photos showcase diamond-coated drills that we commonly use. As you can see, their cylindrical shape implies certain limitations. Sharp Corner Adding a radius to the corners of square pockets or relieves is necessary. Need to add a RADIUS or RELIEVES Radius Corner The smaller the radius, the higher the machining cost. Relieve
Open the catalog to page 4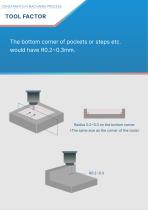
CONSTRAINTS IN MACHINING PROCESS TOOL FACTOR The bottom corner of pockets or steps etc. would have R0.2~0.3mm. Radius 0.2~0.3 on the bottom corner (The same size as the corner of the tools)
Open the catalog to page 5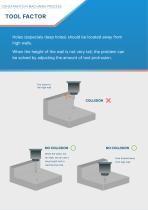
CONSTRAINTS IN MACHINING PROCESS TOOL FACTOR Holes (especialy deep holes) should be located away from high walls. When the height of the wall is not very tall, the problem can be solved by adjusting the amount of tool protrusion. Too close to the high wall NO COLLISION When the wall is not too high, we can use a long-length tool to machine the hole. NO COLLISION Hole located away from high wall
Open the catalog to page 6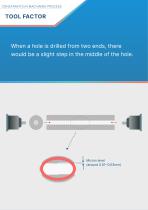
CONSTRAINTS IN MACHINING PROCESS TOOL FACTOR When a hole is drilled from two ends, there would be a slight step in the middle of the hole. Micron level
Open the catalog to page 7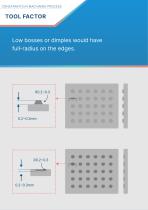
CONSTRAINTS IN MACHINING PROCESS TOOL FACTOR Low bosses or dimples would have full-radius on the edges.
Open the catalog to page 8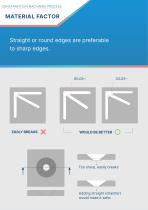
CONSTRAINTS IN MACHINING PROCESS MATERIAL FACTOR Straight or round edges are preferable to sharp edges. EASLY BREAKS Too sharp, easily breaks Adding straight (chamfer) would make it safer.
Open the catalog to page 9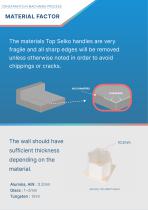
CONSTRAINTS IN MACHINING PROCESS MATERIAL FACTOR The materials Top Seiko handles are very fragile and all sharp edges will be removed unless otherwise noted in order to avoid chippings or cracks. The wall should have sufficient thickness depending on the material. Alumina, AlN : 0.2mm Alumina Thin Wall Product
Open the catalog to page 10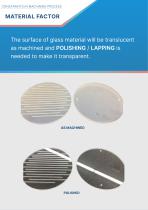
CONSTRAINTS IN MACHINING PROCESS MATERIAL FACTOR The surface of glass material will be translucent as machined and POLISHING / LAPPING is needed to make it transparent.
Open the catalog to page 11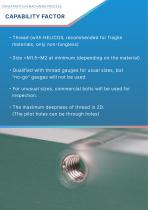
CONSTRAINTS IN MACHINING PROCESS CAPABILITY FACTOR ・Thread (with HELICOIL recommended for fragile materials, only non-tungless) ・Size =M1.5~M2 at minimum (depending on the material) ・Qualified with thread gauges for usual sizes, but "no-go" gauges will not be used ・For unusual sizes, commercial bolts will be used for inspection. ・The maximum deepness of thread is 2D. (The pilot holes can be through
Open the catalog to page 12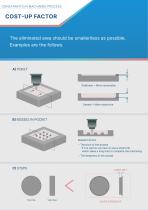
CONSTRAINTS IN MACHINING PROCESS COST-UP FACTOR The eliminated area should be smaller/less as possible. Shallower = More reasonable Deeper = More expensive Related Factors -If it is narrow, we have to use a small drill, which takes a long time to complete the machining. Side View MORE EXPENSIV
Open the catalog to page 13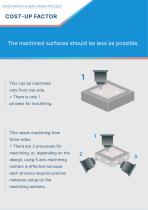
CONSTRAINTS IN MACHINING PROCESS COST-UP FACTOR The machined surfaces should be less as possible. This can be machined only from one side. = There is only 1 process for machining. This needs machining from three sides. = There are 3 processes for machining, or, depending on the design, using 5 axis machining centers is effective because each process requires precise materials setup by the machining workers.
Open the catalog to page 14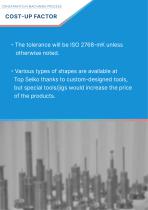
CONSTRAINTS IN MACHINING PROCESS COST-UP FACTOR ・The tolerance will be ISO 2768-mK unless otherwise noted. ・Various types of shapes are available at Top Seiko thanks to custom-designed tools, but special tools/jigs would increase the price
Open the catalog to page 15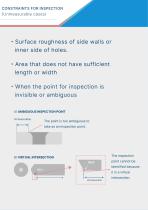
(Unmeasurable cases) ・Surface roughness of side walls or inner side of holes. ・Area that does not have sufficient length or width ・When the point for inspection is invisible or ambiguous A) AMBIGUOUS INSPECTION POINT Unmeasurable The point is too ambiguous to take as an inspection point. The inspection point cannot be identified because it is a virtual intersecti
Open the catalog to page 16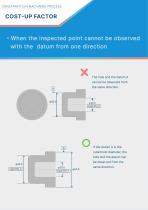
CONSTRAINTS IN MACHINING PROCESS COST-UP FACTOR ・When the inspected point cannot be observed with the datum from one direction The hole and the datum A cannot be observed from the same direction. If the datum A is the outermost diameter, the hole and the datum can be observed from the same dir
Open the catalog to page 17All Top Seiko Co. catalogs and technical brochures
-
Diffusion Bonding Examples
10 Pages
-
Price Option Sheet
1 Pages
-
Top Seiko's Company Brochure
21 Pages
-
Top Seiko's Material Guide
22 Pages
Archived catalogs
-
Product Catalog
11 Pages