Catalog excerpts
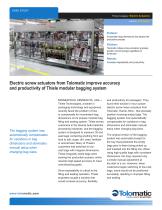
CASE STUDY Product category: Electric Actuators Industry: Packaging Problem: Inconsistent bag dimensions that slowed the production process Solution: Tolomatic rodless screw actuators precisely position incoming bags regardless of dimension Results: Increased repeatability and productivity Electric screw actuators from Tolomatic improve accuracy and productivity of Thiele modular bagging system The bagging system now automatically compensates for variations in bag dimensions and eliminates manual setup when changing bag sizes. MINNEAPOLIS, MINNESOTA, USA— Thiele Technologies, a leader in packaging technology and equipment, recently faced the problem of how to compensate for inconsistent bag dimensions on its popular modular bag filling and sealing system. Thiele serves customers in the diverse bulk-materials processing industries, and the bagging system is designed to measure, fill and seal bags containing anything from pet food to salt, sugar, dirt, seed, fertilizer or animal feed. Many of Thiele’s customers had switched to lowcost bags with irregular dimensions. These irregularly sized bags were slowing the production process, which requires high-speed accuracy to meet manufacturing goals. Since repeatability is critical to the filling and sealing operation, Thiele engineers sought a solution that would increase accuracy, flexibility and productivity for packagers. They found their solution in four custom electric screw linear actuators from Tolomatic, Hamel, Minn., that precisely position incoming empty bags. The bagging system now automatically compensates for variations in bag dimensions and eliminates manual setup when changing bag sizes. The original version of the bagging system was automated except for the tray that positioned the empty bags prior to them being picked up and inserted into the filling line. When using high-quality bags with consistent dimensions, the trays required only a simple manual adjustment at the start of a run. However, when customers began switching to low-cost bags, some would not be positioned accurately, resulting in improper filling and sealing.
Open the catalog to page 1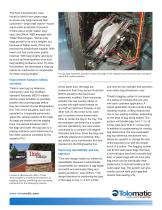
“Pet food manufacturers were forced to switch from paper bags to woven poly bags because their customers—large retail chains—would reject entire truckloads of product if there was a single ‘leaker’ bag,” says Jon Gifford, R&D manager with Thiele Technologies. “Woven poly bags proved to be much tougher, but because of higher costs, China has become the predominant supplier. With lower cost has come lower quality, however. With bag lengths varying by as much as three-quarters of an inch, bag handling problems occur. To solve this problem, we developed a ‘bag top reference’ mechanism to...
Open the catalog to page 2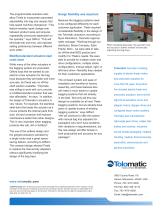
The programmable actuators also allow Thiele to incorporate automated adjustability into bag size recipes that help speed machine changeover. “This feature enables rapid change-over between product sizes and ensures repeatability previously dependant on the operator,” says Gifford. “This will eliminate trial and error, and operator setting preferences between different work shifts.” Modified-standard actuators kept costs down While many of the other actuators in the bagging system are pneumatic, Gifford says that he wanted to use electric screw actuators for the bag trays because they are...
Open the catalog to page 3All Tolomatic catalogs and technical brochures
-
CSWX Compact ServowWeld Actuator
12 Pages
-
FOOD & BEVERAGE SOLUTIONS
8 Pages
-
MAG COUPLED CYLINDER
20 Pages
-
TKS & TKB ACTUATORS
32 Pages
-
MXE SCREW DRIVE ACTUATORS
52 Pages
-
210 SERIES BRAKES
12 Pages
-
Engineering Resources
23 Pages
-
Electric Actuator
4 Pages
-
BCS Rodless Screw Drive Actuator
28 Pages
-
ERD Catalog
32 Pages
-
Cable Cylinder Catalog
40 Pages
-
Brake Intensifier Brochure
2 Pages
-
BC2 Pneumatic Band Cylinder
27 Pages
-
ACS Drive Controller
12 Pages
-
ERD Electric Rod-style Actuator
28 Pages
-
MXB Belt Drive Actuator Catalog
24 Pages
-
AppTip_SRG
2 Pages
-
AppTip_Shocks
2 Pages
-
ERD Low-cost Electric Cylinders
28 Pages
-
IMA Electric Servo Actuator
24 Pages
-
MXE Electric Rodless Actuator
56 Pages
-
ServoWeld System
20 Pages
Archived catalogs
-
Tolomatic Electric Actuators
36 Pages
-
NEW! Electric Stepper Products
16 Pages