Catalog excerpts
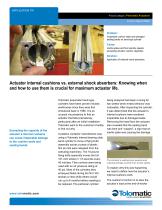
APPLICATION TIP Product category: Pneumatic Actuators Industry: Paper and Plastics Problem: Inoperable cushion seals and damaged sealing bands on band-type cylinder Cause: Inertia spikes and final velocity speeds exceeding actuator cushion capacities Solution: Application of external shock absorbers Actuator internal cushions vs. external shock absorbers: Knowing when and how to use them is crucial for maximum actuator life. Exceeding the capacity of the actuator’s internal cushions can cause irreparable damage to the cushion seals and sealing bands. Tolomatic pneumatic band-type cylinders have been proven industry workhorses since they were first introduced back in 1985. It is an unusual circumstance to find an actuator that fails prematurely, particularly after an initial installation. Tolomatic went to the customer’s facility to find out why. A plastics container manufacturer was using a Tolomatic internal bearing style band cylinder to move a flying knife assembly across a piece of plastic film as rolls were released from the extruding machinery. The 10-pound flying knife assembly moves the full 101-inch stroke in 1.5 seconds every 45 minutes. Flow controls were being used with an air pressure rating of 40 psi. Most of the cylinders they employed failed during the first 100 strokes or less while others would run up to 6 months before needing to be replaced. The particular cylinder being analyzed had been running for two weeks when erratic behavior was noticeable. After inspecting the cylinder, it was determined that the actuator’s internal cushions were rendered inoperable due to damaged seals. Removing the head from the actuator also revealed that the sealing band was bent and “cupped”, a sign that an inertia spike was causing the damage. The actuator’s sealing band experienced cupping damage caused from inertia spikes. To explain why this was happening we need to define how the actuator’s internal cushions work. The cushion’s function is to slow the actuator’s load at the end-of-stroke
Open the catalog to page 1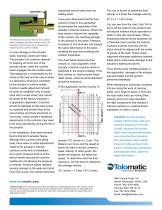
inoperable and air leaks from the sealing band. In this installation, there were several factors that led to actuator failure. Although flow controls were being used, there were no initial adjustments made to the actuator’s internal cushions at the time of installation. As a result, pressure built up at the end-of-stroke because the cushion needle was not allowing the pressure to exhaust. Pressure spikes resulted, causing damage to the seals and band. Once this occurs, the cushion becomes The chart below shows the final velocity vs. load capacities of the actuator’s internal cushions which...
Open the catalog to page 2All Tolomatic catalogs and technical brochures
-
CSWX Compact ServowWeld Actuator
12 Pages
-
FOOD & BEVERAGE SOLUTIONS
8 Pages
-
MAG COUPLED CYLINDER
20 Pages
-
TKS & TKB ACTUATORS
32 Pages
-
MXE SCREW DRIVE ACTUATORS
52 Pages
-
210 SERIES BRAKES
12 Pages
-
Engineering Resources
23 Pages
-
Electric Actuator
4 Pages
-
BCS Rodless Screw Drive Actuator
28 Pages
-
ERD Catalog
32 Pages
-
Cable Cylinder Catalog
40 Pages
-
Brake Intensifier Brochure
2 Pages
-
BC2 Pneumatic Band Cylinder
27 Pages
-
ACS Drive Controller
12 Pages
-
ERD Electric Rod-style Actuator
28 Pages
-
MXB Belt Drive Actuator Catalog
24 Pages
-
AppTip_SRG
2 Pages
-
ERD Low-cost Electric Cylinders
28 Pages
-
IMA Electric Servo Actuator
24 Pages
-
MXE Electric Rodless Actuator
56 Pages
-
ServoWeld System
20 Pages
Archived catalogs
-
Tolomatic Electric Actuators
36 Pages
-
NEW! Electric Stepper Products
16 Pages