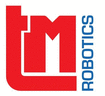
Group: SHIBAURA MACHINE
Catalog excerpts
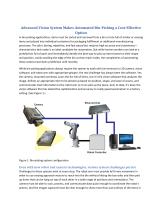
Advanced Vision System Makes Automated Bin-Picking a Cost-Effective Option In bin-picking applications, items must be sorted and removed from a bin or tote full of similar or varying items and placed into individual containers for packaging fulfillment or additional manufacturing processes. The job is boring, repetitive, and fast-paced but requires high accuracy and consistency— characteristics that make it an ideal candidate for automation. But while human workers can look at a jumbled bin full of parts and immediately identify the best way to pick up items based on their shape and position, easily avoiding the edge of the bin as they reach inside, the complexities of automating these actions have been prohibitive until recently. While bin-picking applications always require the system to work with (at minimum) a 3D camera, vision software, and robot arm with appropriate gripper, the real challenge has always been the software. Yes the camera, mounted overhead, scans the bin full of items, but it’s the vision software that analyzes the image, defines an appropriate item to be picked up based on position, shape, and ease of access, and communicates that information to the robot arm so it can pick up the piece. And, to date, it’s been the vision software that has lacked the sophistication and accuracy to really speed automation in a factory setting. (See Figure 1.) Figure 1. Bin-picking system configuration. Even with new robot and camera technologies, visions system challenges persist Challenges to these systems exist at every step. The robot arm must provide full 6-axis movement in order to use varying approach vectors to reach into the bin without hitting the box sides and then pick up items that can be lying on top of each other in a wide range of positions and orientations. The camera must be able to scan, process, and communicate data quick enough to coordinate the robot’s actions. And the images captured must be clear enough to show more than just outlines of the ite
Open the catalog to page 1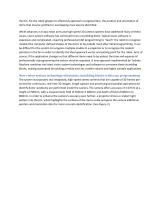
the bin. For the robot gripper to effectively approach a targeted item, the position and orientation of items that may be jumbled or overlapping must also be identified. While advances in 6-axis robot arms and high-speed 3D camera systems have addressed many of these issues, vision system software has continued to be a stumbling block. Typical vision software is expensive and complicated, requiring professional CAD programming to “teach” the robot to recognize models (the computer-defined shapes of the items to be picked). Even after initial programming, it can be difficult for the system...
Open the catalog to page 2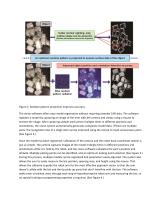
Figure 2. Random pattern projection improves accuracy. The vision software offers easy model registration without requiring complex CAD data. The software registers a model by capturing an image of the item with the camera and simply using a mouse to enclose the image. After capturing sample work pieces multiple times in different positions and orientations, the vision system automatically generates composite model data. If there are multiple parts, the recognition rate of a single item can be improved using the mouse to mask unnecessary parts. (See Figure 3.) Once the model has been...
Open the catalog to page 3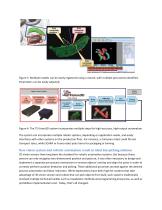
Figure 3. Multiple models can be easily registered using a mouse, with multiple pick points identified. Parameters can be easily adjusted. Figure 4. The TS Vision3D system incorporates multiple steps for high-accuracy, high-output automation. The system can incorporate multiple robotic options, depending on application needs, and easily interfaces with other systems on the production floor. For instance, a Cartesian robot could fill and transport totes, while SCARA or 6-axis robot picks items for packaging or binning. New vision system and robotic automation result in ideal bin-picking...
Open the catalog to page 4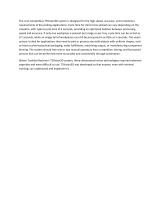
The cost-competitive TSVision3D system is designed for the high speed, accuracy, and consistency requirements of bin-picking applications. Cycle time for items to be picked can vary depending on the situation, with typical cycle time of 3 seconds, providing an optimized balance between processing speed and accuracy. If only one workpiece is present per image or per tray, cycle time can be as fast as 0.7 seconds, while an image full of workpieces can still be processed in as little as 5 seconds. The vision system is ideal for applications that need to pick or process any solid objects with...
Open the catalog to page 5All TM Robotics catalogs and technical brochures
-
THL series
32 Pages
-
TSVision3D
2 Pages
-
General Robot Lineup
8 Pages
-
TH1200A
2 Pages
-
THE400
2 Pages
-
TSVision3D software Solution
21 Pages
-
TVM Series - 6-axis Robots
2 Pages
-
BAIII Series - Cartesian Robots
230 Pages
-
TVL700
2 Pages
-
TVL500
2 Pages
-
TV1000H
2 Pages
-
TV1000
2 Pages
-
TV800
2 Pages
-
Robot Controller TS3100
3 Pages
-
TH550
2 Pages
-
TH250A
2 Pages
-
TH180
1 Pages
-
TH350A
2 Pages
-
TH850A
2 Pages
-
TH1050A
2 Pages
-
THP700
2 Pages
-
THP550
2 Pages
-
TSL3000E Controller
3 Pages
-
TH Series - SCARA Robot
14 Pages
-
THL900
2 Pages
-
THL700
2 Pages
-
THL600
2 Pages
-
THL500
2 Pages
-
THL1000
2 Pages
-
THL800
2 Pages
-
THL400
2 Pages
-
THL300
2 Pages
-
TH450A
2 Pages
-
SCARA THL RANGE
10 Pages
-
TH650A
2 Pages
-
Cartesian linear actuators
1 Pages
Archived catalogs
-
TH1200A
1 Pages
-
TH450
1 Pages
-
SCARA Robot TH Series
20 Pages
-
Product range TH/SR Series
2 Pages
-
BA II Arm Robot Catalog
247 Pages