

Catalog excerpts
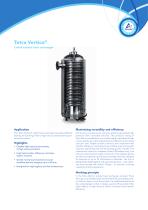
Tetra Vertico® Coiled tubular heat exchanger Maximizing versatility and efficiency The Tetra Vertico coiled heat exchanger provides efficient heating and cooling of low to high viscous and smooth to particulate products. ® Highlights • Enables high capacity processing of high viscous products • High heat transfer efficiency minimizes system volumes • Gentle mechanical treatment ensures excellent particle integrity up to ø 25 mm • Designed for high hygiene and low maintenance Continuous processing of viscous products generates high pressure with increased velocity. The pressure rating of Tetra Vertico enables you to process higher capacities of high viscous products, improving production efficiency and cutting cost per litre. Higher product velocity also improves heat transfer efficiency, minimizing heat surface area and system volumes, optimizing CIP and minimizing product losses. The coiled mono-tube unit – between 30 and 100 meters long – has only one inlet and one outlet connection. This enables gentle mechanical treatment and ensures excellent particle integrity for particles of up to 25 millimetres in diameter. The unit is designed for high hygiene and easy maintenance – with a floating end through the bottom flange – to prevent cracking caused by thermal expansion. Working principle In the Tetra Vertico tubular heat exchanger, product flows through a coil-shaped tube and media flows around the product tube to heat or cool the product. An additional feature of the coiled design is that it creates a second flow pattern (the Dean effect) at high velocity, which increases heat transfer efficiency.
Open the catalog to page 1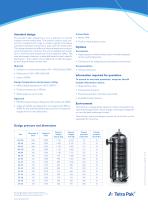
Standard design The product tube, shaped as a coil, is placed in a vertical chamber where media flows. The bottom product tube connection is sealed by O-rings to create a system that allows movement between the product tube and the media shell. This design absorbs the effects of thermal expansion and prevents the tube from cracking. The unit is supplied with insulation to minimize heat losses and ensure operator safety. The heat exchanger dimension is selected based on each specific application – the number of units depends on desired capacity and required heat transfer area. • Surfaces in...
Open the catalog to page 2All Tetra Pak catalogs and technical brochures
-
Brining system S
2 Pages
-
Mould Handling system
2 Pages
-
Ice Cream Filler A3
6 Pages
-
Ice Cream Mix unit A3
3 Pages
-
Ice Cream Mix unit A2
3 Pages
-
Powder Valve
2 Pages
-
Powder hopper
2 Pages
-
Tetra Pak® High Shear Mixer
2 Pages
-
Tetra Pak® Heat Exchangers
8 Pages
-
Tetra-laval-2017-2018
60 Pages
-
Tetralaval
60 Pages
-
Tetra Pak® Aseptic Tank VC
2 Pages
-
Tetra Pak® Aseptic Tank VD
2 Pages
-
Tetra Pak® In-line Blender D
2 Pages
-
Tetra Alblend™
5 Pages
-
Tetra Alblend 5SP
4 Pages
-
Tetra Alblend® carboblender
3 Pages
-
Tetra Alfast®B4
2 Pages
-
Mixing technology
28 Pages
-
Tetra Pak® Mixer RJCI
4 Pages
-
Tetra Alwin® Soy
2 Pages
-
The value of adding value
12 Pages
-
Tetra Magna Evaporator ? TVR
2 Pages
-
Tetra Magna Evaporator ? MVR
2 Pages
-
Tetra Alsafe® Aseptic tank
2 Pages
-
Moving Food Forward. Together?
24 Pages
-
Tetra Alex® 2
2 Pages
-
HighHygieneTank
2 Pages
-
Tetra Therm® Aseptic Drink 1
3 Pages
-
Tetra Hoyer DeepBlue?SM
4 Pages