

Catalog excerpts
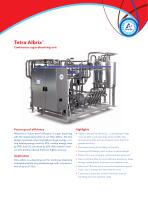
Tetra Albrix Continuous sugar-dissolving unit Future-proof efficiency Welcome to future-proof efficiency in sugar dissolving with the newest generation of our Tetra Albrix. The new design maximizes output and delivers huge savings – cutting heating energy costs by 42%, cooling energy costs by 55%, and CO2 emissions by 62%. Raw material costs are also greatly reduced thanks to higher accuracy. • Higher operational efficiency – cuts heating energy • Perfect fit in our complete customized line solutions Tetra Albrix is a dissolving unit for continous dissolving and pasteurisation of granulated sugar with a concentration of up to 67 °Brix. • New cross-flow filter for more efficient dissolving, lower costs by 42%, cooling energy costs by 55%, CO2 emissions by 62%, and raw material costs thanks to greater accuracy • Uncompromising food safety and quality • Future-proof flexibility with unique modular design energy consumption, and lower raw material costs • Advanced °Brix set-point control for exact dosing and huge cuts in energy and raw material costs • Continuous automatic control minimizes manual handling and cuts operator costs
Open the catalog to page 1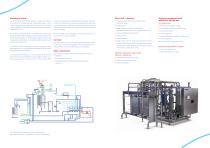
Working principle Incoming treated water is preheated in a separate water heater and fed into a dissolving tank. Granulated sugar is continously conveyed from hopper to dissolving tank. In order to maintain agitation in the dissolving tank, a pump circulates the sugar/water slurry. The slurry is pumped through a cross-flow filter, which separates dissolved sugar from sugar crystals. Sugar crystals return to the dissolving tank, while dissolved sugar passes through to an optional pasteurizer, optional decolourizing system, and to a final destination tank. An optional pasteurizer reduces...
Open the catalog to page 2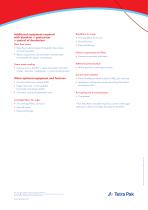
Additional equipment required with dissolver + pasteurizer + control of decolorizer Mass flow meter • Mass flow meters instead of magnetic flow meters on incoming water • When using reverse osmosis water or sweet water is recovered, this option is mandatory • Two bag filters, 25 micron • Shut off valves Pressure supervision on filters • Pressure transmitter with alarm Tower water cooling Ethernet communication • Extra section in the PHE + valves (included in the third model – dissolver + pasteurizer + control of decolorizer) • With supervisory automation system Control room solution Other...
Open the catalog to page 3All Tetra Pak catalogs and technical brochures
-
Brining system S
2 Pages
-
Mould Handling system
2 Pages
-
Ice Cream Filler A3
6 Pages
-
Ice Cream Mix unit A3
3 Pages
-
Ice Cream Mix unit A2
3 Pages
-
Powder Valve
2 Pages
-
Powder hopper
2 Pages
-
Tetra Pak® High Shear Mixer
2 Pages
-
Tetra Pak® Heat Exchangers
8 Pages
-
Tetra-laval-2017-2018
60 Pages
-
Tetralaval
60 Pages
-
Tetra Pak® Aseptic Tank VC
2 Pages
-
Tetra Pak® Aseptic Tank VD
2 Pages
-
Tetra Pak® In-line Blender D
2 Pages
-
Tetra Alblend™
5 Pages
-
Tetra Alblend 5SP
4 Pages
-
Tetra Alblend® carboblender
3 Pages
-
Tetra Alfast®B4
2 Pages
-
Mixing technology
28 Pages
-
Tetra Pak® Mixer RJCI
4 Pages
-
Tetra Alwin® Soy
2 Pages
-
The value of adding value
12 Pages
-
Tetra Magna Evaporator ? TVR
2 Pages
-
Tetra Magna Evaporator ? MVR
2 Pages
-
Tetra Alsafe® Aseptic tank
2 Pages
-
Moving Food Forward. Together?
24 Pages
-
Tetra Alex® 2
2 Pages
-
HighHygieneTank
2 Pages
-
Tetra Therm® Aseptic Drink 1
3 Pages
-
Tetra Hoyer DeepBlue?SM
4 Pages