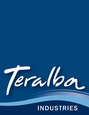
Catalog excerpts
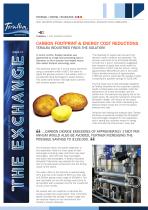
In recent months, Teralba Industries was approached by a large food processing plant in Tasmania, to find a solution that helped reduce their carbon footprint and energy costs. This particular plant has 2 in-line potato blanchers using a consistent inflow of 85°C hot water to adjust the glucose content in the potato, which is consistently being discharged to waste streams. This waste water stream has high starch content and contains potato chunks. thermal i mixing i stainless • heat transfer systems i mixing & agitating solutions i stainless steel fabrication thermal | heat transfer systems carbon footprint & energy cost reductions teralba industries finds the solution! “The feasibility of waste heat recovery from blancher water overflows was assessed. The recovery was found to be technically feasible on both line 1 and 2. Calculations suggested that recovery of waste heat would avoid the consumption of 647t coal per annum, saving approximately $84,000 per year in fuel costs. Carbon dioxide emissions of approximately 1780t per annum would also be avoided, further increasing the possible savings to $128,000.” The end result was a heat exchanger designed by Teralba Industries for the customer's specific needs. Limited space was available under the blanchers to fit a heat exchanger, and the outflow from the blancher was gravity fed to the waste drains. By using the turbulence enhanced Dimpletfo® design, the criteria for the space requirements were met whilst maintaining low pressure drops across the unit for the gravity pressure flow rate. Using the field testing and analysis data, Teralba Industries successfully installed the Dimpletfo® heat exchangers designed for this application and is saving the customer money in energy costs and also the environment, every day. kk ...CARBON DIOXIDE EMISSIONS OF APPROXIMATELY 1780T PER annum would also be avoided, further increasing the POSSIBLE SAVINGS TO $128,000. H The entrained starch and potato fragments in this application ruled out many types of heat exchangers including; plate and frame type heat exchangers, shell and tube heat exchangers and spiral heat exchangers. A Teralba Industries Dimpletfo® Monotube was selected for this duty due to the particulate entrainment and the fouling nature of the starch. The water inflow to the blancher is approximately 150C and has to be heated to 90°C at a flow rate of 6,500l/hr giving a total usage of 362kW/hr. This was calculated out and the savings were found to be excellent with a payback time for the investment of only a few months. We worked with our customer to calculate the energy savings they could expect. Their comments below illustrates the savings in steam usage and the reduced impact on the environment that Teralba's solution delivered.
Open the catalog to page 1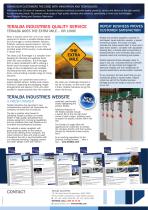
giving our customers the edge with innovation and technology. With more than 35 years of experience, Teralba Industries continues to provide quality products, service and advice on the right product for your industry needs. We provide a wide range of high quality stainless alloy products, specialising in three core technologies: Heat Transfer, Mixing and Stainless Fabrication. teralba industries quality serviceteralba goes the extra mile... or 1000! repeat business proves customer satisfaction When a request came from one of our valued customers to deliver a versatile Mixquip series 210...
Open the catalog to page 2