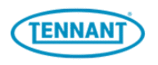
Group: Tennant

Catalog excerpts
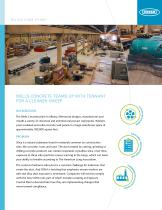
WELLS CONCRETE TEAMS UP WITH TENNANT FOR A CLEANER SWEEP BACKGROUND The Wells Concrete plant in Albany, Minnesota designs, manufactures and installs a variety of structural and architectural precast wall panels. Workers pour insulated and solid concrete wall panels in a huge warehouse space of approximately 180,000 square feet. M sites, like concrete, rocks and sand. The dust created by cutting, grinding or drilling concrete products can contain respirable crystalline silica. Over time, exposure to these silica particles causes scarring in the lungs, which can harm your ability to breathe according to The American Lung Association. create the dust. And OSHA is insisting that employers ensure workers are safe and silica dust exposure is minimized. Companies will need to comply move toward compliance. with the new OSHA rule, part of which includes creating an Exposure Control Plan to demonstrate how they are implementing changes that The control of airborne silica dust is a constant challenge for industries that Silica is a natural substance found in materials common on construction
Open the catalog to page 1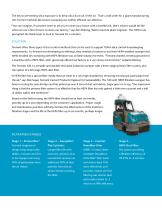
The key to preventing silica exposure is to keep silica dust out of the air. That’s a tall order for a giant manufacturing site. Former methods like broom sweeping are neither efficient nor effective. “You can imagine, if someone were to ask you to clean your house with a toothbrush, that’s what it would be like when we use a floor broom to clean our factory,” says Ben Dalsing, Wells Concrete plant engineer. The OSHA rule prompted the Wells team to look to Tennant for a solution. SOLUTION Tennant offers three types of dust control methods that can be used to support OSHA silica control...
Open the catalog to page 2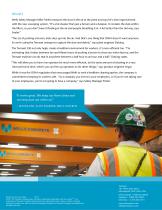
RESULTS Wells Safety Manager Mike Frieler measures the dust in the air at the plant and says he’s seen improvement with the new sweeping system. “It’s a lot cleaner than just a broom and a dustpan. It contains the dust within the filters, so you don’t have it floating in the air and people breathing it in. A lot better than the old way, says Frieler.” “The act of pushing a broom, kicks dust up into the air. And that’s one thing that OSHA doesn’t want anymore. So we’re using the Tennant sweeper to capture the dust and debris,” says plant engineer Dalsing. The Tennant S30 not only helps...
Open the catalog to page 3All Tennant catalogs and technical brochures
-
V-CAN-10
8 Pages
-
Vacuum Cleaners
8 Pages
-
2370
2 Pages
-
1610
2 Pages
-
1210 / 1215
2 Pages
-
S30
6 Pages
-
S20
6 Pages
-
6100
4 Pages
-
M20
6 Pages
-
T17
4 Pages
-
T16
6 Pages
-
T7+
4 Pages
-
T500
6 Pages
-
EX-SC-1020P
2 Pages
-
636
4 Pages
-
sentinel
6 Pages
-
i-mop-xl,i-mop
4 Pages
-
EX-SC-412 Brochure
2 Pages
-
3640 Brochure
2 Pages
-
T1B Brochure
4 Pages
-
V-LWU-13 Brochure
2 Pages
-
V-BP-6 / V-BP-10 Brochure
4 Pages
-
FM Series Brochure
2 Pages
-
F14 Brochure
2 Pages
-
EX-Spot-2 Brochure
2 Pages
-
M17 Brochure
6 Pages
-
S5 Brochure
4 Pages
-
T350 Brochure
4 Pages
-
T600e Brochure
4 Pages
-
ISS ec-H2O Testimonial
1 Pages
-
ec-H2O Testimonials GCA
1 Pages
-
Education Brochure K-12
4 Pages
-
Education Brochure
20 Pages
-
BSC Brochure
24 Pages
-
Commercial Service Brochure
4 Pages
-
TennantTrue Service Brochure
4 Pages
-
Gold Service Plan Brochure
2 Pages
-
Silver Service Brochure
2 Pages
-
Silica Dust Brochure
4 Pages
-
Hard-N-Seak Brochure
2 Pages
-
clean smarter and save
1 Pages
-
Eco-EDS™
2 Pages
-
CASE STUDY
2 Pages
-
M30 Brochure
6 Pages
-
Tennant vacuum range
4 Pages
-
T300
6 Pages
-
800
2 Pages
-
1210 / 1215
2 Pages
-
1611
2 Pages
-
V-BP-7
2 Pages
-
V-SMU-36
2 Pages
-
250
2 Pages
-
T 17
6 Pages
-
OS 3
2 Pages
-
Orbital Scrubbing
2 Pages
-
M30
6 Pages
-
S30
6 Pages
-
os3 Satellite System
2 Pages
-
os3
2 Pages
-
ReadySpace
4 Pages
-
Food & Beverage
6 Pages
-
Orbio Auxiliary Tank Sell
2 Pages
-
T1
2 Pages
-
R3
4 Pages
-
T2
4 Pages
-
T20 Ride-on scrubber-dryer
6 Pages
-
T16
6 Pages
-
S10
4 Pages
-
T12
6 Pages
-
S8 Wide Area Battery Sweeper
2 Pages
Archived catalogs
-
S3
4 Pages
-
F-Series Brochure
2 Pages
-
B1
2 Pages
-
B5 / B7
2 Pages
-
Orbio 5000-Sc
2 Pages
-
E5
2 Pages
-
V6
2 Pages
-
5680
4 Pages
-
5000-Sc
8 Pages
-
Product Range Overview EMEA
2 Pages