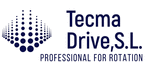
Catalog excerpts
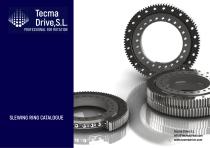
SLEWING RING CATALOGUE Tecma Drive S.L. info@tecmadrive.com www.tecmadrive.com
Open the catalog to page 1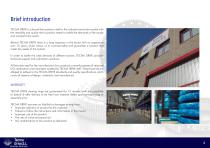
Brief introduction TECMA DRIVE is a brand that positions itself in the industrial and solar market with the versatility and quality that a product needs to satisfy the demands of the ample and overparticular sector. Behind TECMA DRIVE there is a long trajectory in the sector with an experience over 15 years, which allows us to commercialize and guarantee a product that meets the needs of the market. In order to battle the wide demand of different sectors, TECMA DRIVE provides technical support and calculation solutions. All factories used for the manufacture of our products currently...
Open the catalog to page 4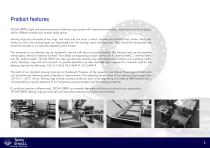
Product features TECMA DRIVE’s light and reinforced series of slewing rings comply with international standards, requirements and are approved for different simple and complex applications Slewing rings are composed of two rings, one inner and one outer, in which raceway are obtained that contain rolling elements on which the working loads are transmitted from the moving ring to the fixed one. They should be transported and stored horizontally or on specially adapted incline frames. The raceways of our slewing ring are hardened, and the soft area is properly marked. The slewing rings can be...
Open the catalog to page 5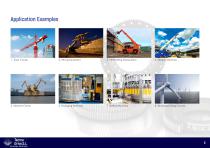
Application Examples 3. Hand Lifting Manipulators 8. Renewable Energy Sources
Open the catalog to page 6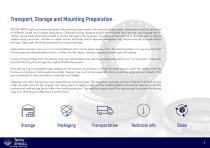
Transport, Storage and Mounting Preparation TECMA DRIVE's light and reinforced series of the slewing rings comply with international standards, requeriments and are approved for different simple and complex applications. Vibrations during transport should be minimized because they may damage the raceways. Shock loads should be avoided to prevent damage to the raceways. Caution must be taken not to dislodge seals or grease nipples during movement. Wooden or rubber spacers should be used to separate unwrapped rings stacked vertically to avoid surface damage. Gear teeth should be protected...
Open the catalog to page 7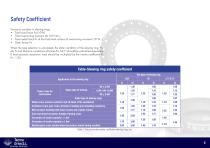
Safety Coefficient Forces to consider in slewing rings: • Total axial force Fa (104N) • Total overturning moment Mr (104 Nm.) • Total radial force Fr of the fractional surface of overturning moment (104 N ) • Gear forces Fn When the type selection is calculated, the static condition of the slewing ring, Fa, Mr, Fr and Dynamic conditions of forces Fa, Mr, Fr should be calculated separately. If host ascends, ascension load should be multiplied by the inertia coefficient K, K= 1,25. Table-Slewing ring safety coefficient The type of slewing ring Q,01 Application of the slewing ring fs Tower...
Open the catalog to page 8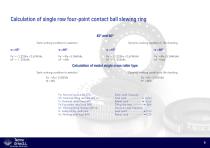
Calculation of single row four-point contact ball slewing ring 45º and 60º Static working condition to selection Dynamic working condition to life checking Calculation of model single cross roller type Static working condition to selection Dynamic working condition to life checking Fa: Nominal axial load (kN) Mr: Nominal tilting moment (kN.m) Fr: Nominal radial load (kN) Fa':Equivalent axial load (kN) M': Working tilting moment (kN.m) fs: Safety factor coefficient fd: Working axial load (kN) Static Load Capacity: Axial load (Coa) Radial Load (Cor) Tilting Moment (Mr) Dynamic Load Capacity:...
Open the catalog to page 9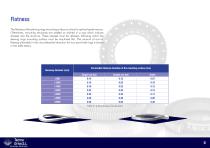
Flatness The flatness of the slewing rings mounting surface is critical to optimal performance. Oftentimes, mounting structures are welded or worked in a way which induces stresses into the structure. These stresses must be relieved, following which the slewing rings mounting surface must be machined flat. The amount of out-offlatness allowable in the circumferential direction for four-point ball rings is shown in the table below. Permissible flatness deviation of the mounting surface (mm) Single row ball Table 2: Surface flatness requirements
Open the catalog to page 10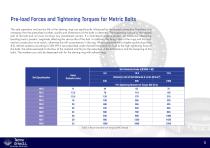
Pre-load Forces and Tightening Torques for Metric Bolts The safe operation and service life of the slewing rings are significantly influenced by the bolted connection.Therefore, it is necessary that the prescribed number, quality and dimensions of the bolts is observed. The supporting surface of the tapped part of the bolt and nut must not show any chambered corners. If a chambered angle is present, an additional alternating bending load is present, negatively affecting the service life of the bolt. In addition, the fixing holes of the rings and the connection construction must match,...
Open the catalog to page 11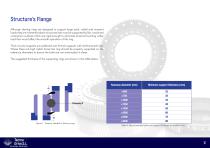
Structure’s Flange Although slewing rings are designed to support large axial, radial and moment loads they are inherently elastic structures that must be supported by flat, machined companion surfaces which are rigid enough to eliminate torsional buckling under load that would affect the smooth operation of the ring. Thick circular supports are preferred over thinner supports with reinforcement ribs. Where there are high radial forces the ring should be properly supported on the reference diameters to ensure the bolts are not overloaded in shear. The suggested thickness of the supporting...
Open the catalog to page 12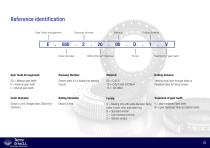
Reference identification Gear Teeth Arrangement Raceway Number Outer Diameter Rolling Element Diameter Drilling Scheme Treatment of gear teeth Gear Teeth Arrangement: Raceway Number: Drilling Scheme: SD = Without gear teeth E = External gear teeth I = Internal gear teeth Shown when it's a double row slewing ring (2). Slewing rings have through holes or threaded holes for fixing screws. Outer Diameter: Rolling Elements: Treatment of gear teeth: Shown in mm. Ranges from 200mm to 3500mm. A = Slewing ring with same diameter fixing V = gear hardened flank teeth W = gear hardened flank and bottom...
Open the catalog to page 13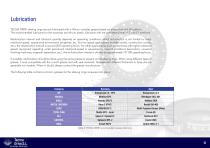
Lubrication TECMA DRIVE slewing rings are pre-lubricated with a lithium-complex grease based on mineral oil with EP-additive. The recommended lubricants for the raceways are lithium plastic lubricants with the consistency level of 2 with EP additives. Relubrication interval and lubricant quantity depends on operating conditions, which includes but is not limited to: load, rotational speed, operational environment properties, etc. For low-speed applications (mobile cranes, construction cranes, etc.), the relubrication interval is around 200 operating hours. For other applications, such as...
Open the catalog to page 14