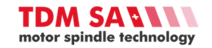
Catalog excerpts
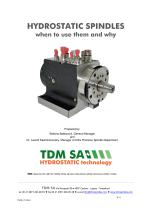
HYDROSTATIC SPINDLES when to use them and why Prepared by: Stefano Baldaccini, General Manager and Dr. Leonid Kashchenevsky, Manager of Ultra Precision Spindle Department TDM reserves the right to modify these service instructions without previous written notice. TDM SA Via Rompada 38 ● 6987 Caslano - Lugano - Switzerland tel. 00 41 (0)91 606 68 94 ● fax 00 41 (0)91 606 20 48 ● e-mail tdm@tdmspindles.com ● www.tdmspindles.com 1/11
Open the catalog to page 1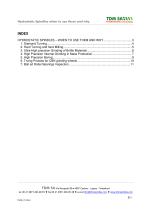
Hydrostatic Spindles when to use them and why ___________________________________________________________________________________________________________________________________________________________________________________________ TDM SA Via Rompada 38 ● 6987 Caslano - Lugano - Switzerland tel. 00 41 (0)91 606 68 94 ● fax 00 41 (0)91 606 20 48 ● e-mail tdm@tdmspindles.com ● www.tdmspindles.com 2/11
Open the catalog to page 2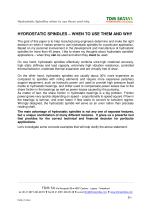
Hydrostatic Spindles when to use them and why ___________________________________________________________________________________________________________________________________________________________________________________________ HYDROSTATIC SPINDLES – WHEN TO USE THEM AND WHY The goal of this paper is to help manufacturing engineers determine and make the right decision on when it makes sense to use hydrostatic spindles for a particular application. Based on my personal involvement in the development and manufacture of hydrostatic spindles for more than 40 years, I like to share my...
Open the catalog to page 3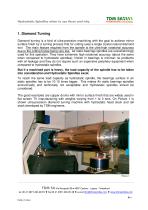
Hydrostatic Spindles when to use them and why ___________________________________________________________________________________________________________________________________________________________________________________________ 1. Diamond Turning Diamond turning is a kind of ultra-precision machining with the goal to achieve mirror surface finish by a turning process that for cutting uses a single crystal natural diamond tool. The main feature required from the spindle is the ultra-high rotational accuracy due to the cutting forces being very low. Air static bearings spindles are...
Open the catalog to page 4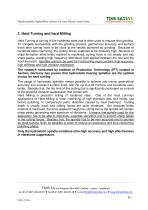
Hydrostatic Spindles when to use them and why ___________________________________________________________________________________________________________________________________________________________________________________________ 2. Hard Turning and hard Milling Hard Turning is turning of the hardened steel and is often used to replace final grinding. To compete successfully with the grinding process, geometrical accuracy and surface finish after turning have to be close to the results achieved by grinding. Because of hardened steel machining, the cutting forces expected to be...
Open the catalog to page 5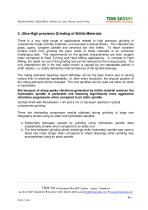
Hydrostatic Spindles when to use them and why ___________________________________________________________________________________________________________________________________________________________________________________________ 3. Ultra-High precision Grinding of Brittle Materials There is a very wide range of applications related to high precision grinding of components made of brittle materials, one example is optical lenses. The materials like glass, quartz, tungsten carbide and ceramics are very brittle. To reach excellent surface finish from grinding the parts made of these...
Open the catalog to page 6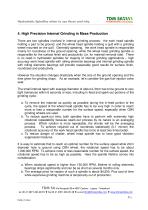
Hydrostatic Spindles when to use them and why ___________________________________________________________________________________________________________________________________________________________________________________________ 4. High Precision Internal Grinding in Mass Production There are two spindles involved in internal grinding process: the work head spindle holding a part to be ground, and the wheel head spindle holding a quill with a grinding wheel mounted on the quill. Generally speaking, the work head spindle is responsible mainly for roundness of the ground opening, while...
Open the catalog to page 7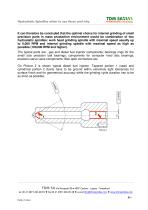
Hydrostatic Spindles when to use them and why ___________________________________________________________________________________________________________________________________________________________________________________________ It can therefore be concluded that the optimal choice for internal grinding of small precision parts in mass production environment would be combination of two hydrostatic spindles: work head grinding spindle with maximal speed usually up to 6,000 RPM and internal grinding spindle with maximal speed as high as possible (100,000 RPM and higher). The typical...
Open the catalog to page 8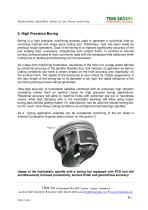
Hydrostatic Spindles when to use them and why ___________________________________________________________________________________________________________________________________________________________________________________________ 5. High Precision Boring Boring is a high precision machining process used to generate a cylindrical hole by removing material with single point cutting tool. Preliminary, hole has been made by previous rough operations. Goal of the boring is to improve significantly accuracy of the just existing hole: roundness, straightness and surface finish. In contrast to...
Open the catalog to page 9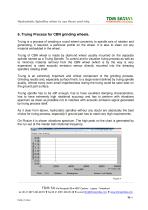
Hydrostatic Spindles when to use them and why ___________________________________________________________________________________________________________________________________________________________________________________________ 6. Truing Process for CBN grinding wheels. Truing is a process of creating a round wheel concentric to spindle axis of rotation and generating, if required, a particular profile on the wheel. It is also to clean out any material embedded in the wheel. Truing of CBN wheel is made by diamond wheel usually mounted on the separate spindle named as a Truing Spindle....
Open the catalog to page 10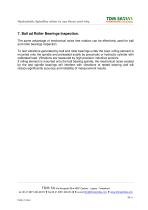
Hydrostatic Spindles when to use them and why ___________________________________________________________________________________________________________________________________________________________________________________________ 7. Ball ad Roller Bearings Inspection. The same advantage of mechanical noise free rotation can be effectively used for ball and roller bearings inspection. To test vibrations generated by ball and roller bearings under the load, rolling element is mounted onto the spindle and preloaded axially by pneumatic or hydraulic cylinder with calibrated load. Vibrations...
Open the catalog to page 11All TDM SA catalogs and technical brochures
-
MULTI-TOOLS
4 Pages
-
GRINDING MOTOR SPINDLES
8 Pages
-
motor spindle technology
6 Pages
-
COMPARISON TDM MULTI-TOOLS
1 Pages
-
B-axis
2 Pages
-
ADAPTOR SPINDLES
6 Pages