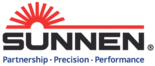
Catalog excerpts
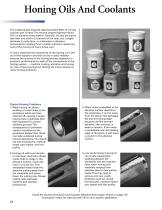
Honing Oils And Coolants The single largest expense (approximately 90%) of honing cost per part is labor. The second largest expense (about 10%) is abrasive consumption. Typically, oil cost per part is less than one tenth of a percent of the total, yet, a slight decrease in cycle time, or a decrease in abrasive consumption resulting from a better lubricant, repays the cost of the honing oil many times over. In many instances the importance of the honing oil is left out of the equation and that can be a costly mistakebecause the success of the honing process depends on precision performance by each of the components of the honing system … machine, tooling, abrasive and honing oil. Use of Genuine Sunnen Honing Oil is the solution to many honing problems. Typical Honing Problems 1. Weak honing oil allows welding of metal chips to the workpiece which are then sheared off, causing a larger total surface roughness than that expected for a given abrasive grit size. The consequence is unwanted random scratches on the workpiece deeper than those normally produced during honing operations. The results are lost productivity, material waste, part rejects, and lost profits. 3. When metal embedded in the abrasive surface rewelds to the workpiece, it is torn away from the stone. This damages the stone’s trailing edge because vitrified bonded abrasive, like concrete, is weak in tension. If the metal is embedded near the leading edge of the stone, it will leave a scratch in the abrasive surface. 2. Honing oil with low lubricity or improper chemistry allows metal chips to lodge in the abrasive surface, much like mud in a snow tire. This embedded metal holds the abrasive surface away from the workpiece and slows down the cutting rate. Slower cutting rates decrease machine and operator productivity. 4. Low performance honing oil can create catastrophic welding between the workpiece and the mandrel shoe when honing soft materials ranging from stainless steel to low carbon steels. This may lead to serious and very costly problems such as: ruined honing tools, machine failure, part rejects and lost profits. Check the Sunnen Honing Oil and Coolant Selection/Information Charts on page 174 to properly match the right Sunnen Oil to your specific application.
Open the catalog to page 1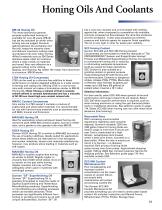
Honing Oils And Coolants MB-30 Honing Oil The most economical general purpose sulphurized honing oil available for over 40 years. MB-30 has set the standard by which other honing oils are judged. Prevents galling between the workpiece and the tool, keeps the abrasive clean and delivers maximum cutting rates and abrasive life even when honing difficult materials such as 300 Series stainless steels. Ideal for locations where a wide variety of materials are honed. Also very effective as a general cutting oil for drilling, tapping, and reaming. No matter the metal, from aluminum to zirconium,...
Open the catalog to page 2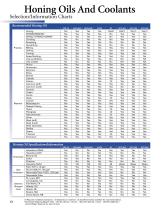
Honing Oils And Coolants Selection/Information Charts Hazardous OSHA
Open the catalog to page 3All Sunnen Products Company catalogs and technical brochures
-
SV-30 series
8 Pages
-
SV-15
8 Pages
-
Portable Hones and Accessories
20 Pages
-
DH SERIES
8 Pages
-
SV-2400 Series
8 Pages
-
Precision Honing Supplies
203 Pages
-
SHDD Series
8 Pages
-
PG Bore Gaging System
8 Pages
-
CGT KROSSGRINDING®
14 Pages
-
Portable Hones
34 Pages
-
GHSS GHTS
16 Pages
-
corporate brochure
16 Pages
-
Small Engines
5 Pages
-
Cylinder Liners
5 Pages
-
Gears
5 Pages
-
Hydraulics
5 Pages
-
Fuel Injectors
5 Pages
-
HTD Heavy Duty Tube Hone
4 Pages
-
HTC Series Honing
4 Pages
-
SH-6000
8 Pages
-
SH-5000
8 Pages
-
SH-4000
8 Pages
-
SSH-1680
2 Pages
-
SV-15 Vertical Hone
8 Pages
-
SV-2500 series
8 Pages
-
Engine Honing Equipment
66 Pages
-
Precision Honing Supplies
199 Pages
-
HTB - S Series
8 Pages
-
MBB-166
2 Pages
-
2C Tooling
2 Pages
-
CH-100
6 Pages
-
SHO Honing Oil
2 Pages
-
Heavy-Duty Push Tools
60 Pages
-
Portahones
6 Pages
-
GHTS GHSS Engine
4 Pages
-
MMT High Production
2 Pages
-
GNH Giant Portable Hone
1 Pages
-
X-SP-9003: Dial Bore Gages
8 Pages
-
GH Tooling Catalog
60 Pages
-
X-SP-5070: 21 Case Histories
24 Pages
-
M-series
12 Pages
-
MPS
9 Pages
-
Multi-Stone (MMT) Tools
2 Pages
-
GNH
1 Pages
-
Sunnen Portable Hones
20 Pages
-
X-SP-5061
29 Pages