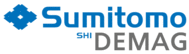

Catalog excerpts
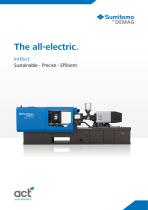
The all-electric. IntElect. Sustainable - Precise - Efficient
Open the catalog to page 1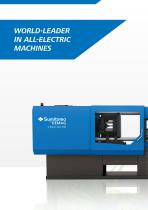
WORLD-LEADER IN ALL-ELECTRIC MACHINES
Open the catalog to page 2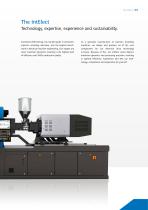
The IntElect Technology, expertise, experience and sustainability. Sumitomo (SHI) Demag, the market leader in all-electric injection moulding machines, sets the highest benchmark in electrical machine engineering. Our targets are clear; maximum dynamics resulting in the highest level of efficiency and 100% production quality. As a specialist manufacturer of injection moulding machines, we design and produce all of the core components for our electrical drive technology in-house. Because of this, our IntElect series delivers maximum dynamics and processing precision, resulting in optimal...
Open the catalog to page 3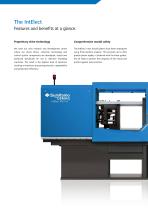
The IntElect Features and benefits at a glance. Proprietary drive technology Comprehensive mould safety We have our own research and development centre where our direct drives, converter technology and control system components are developed, tested and produced specifically for use in injection moulding machines. The result is the highest level of dynamics resulting in maximum processing precision, repeatability and production efficiency. The IntElect’s new mould platens have been redesigned using finite element analysis. This provides up to 20% greater platen rigidity. Combined with the...
Open the catalog to page 4
Intuitive control Investing in a sustainable future The IntElect control is intuitive to use and offers a variety of options for process monitoring and control. The logical and simple programming with pre-defined flexible machine sequences enables users to fully utilise the IntElect’s numerous features to optimise productivity. The electrical energy consumed by injection moulding machines is converted into heat. Part of it directly, the other part indirectly via kinetic energy, deformation and friction. All of the heat generated must be dispersed and cooled. Naturally, less heat generated...
Open the catalog to page 5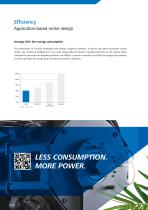
Efficiency Application-based motor design. Average 60% less energy consumption The combination of in-house developed drive motors, frequency inverters, as well as the entire servomotor control system, has resulted in building one of the most energy-efficient injection moulding machines on the market. When compared to other injection moulding machines, the IntElect is proven to consume up to 80% less energy than hydraulic machines and 20% less energy than conventional all-electric machines. IntElect Diagram: Energy saving Servo hydraulically LESS CONSUMPTION. MORE POWER.
Open the catalog to page 6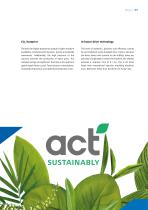
In-house drive technology The basis for higher production output is higher machine availability, combined with dynamic, precise and parallel movements. Additionally, the high precision of the machine prevents the production of reject parts. The material savings are significant. Running at the optimum speed equals faster cycles, fewer process interruptions, increased productivity, and optimised production costs. This level of dynamics, precision and efficiency cannot be accomplished using standard drive motors. Because the direct drives and controls on the IntElect series are precisely...
Open the catalog to page 7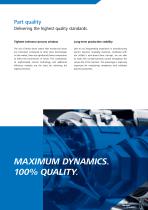
Part quality Delivering the highest quality standards. Tightest tolerance process window Long-term production stability The use of direct drives means that mechanical losses are minimised. Compared to other drive technologies on the market, there are significantly fewer components to affect the transmission of forces. This combination of sophisticated control technology and additional efficiency modules are the basis for achieving the highest precision. Due to our longstanding experience in manufacturing electric injection moulding machines, combined with the IntElect’s own-brand drive...
Open the catalog to page 8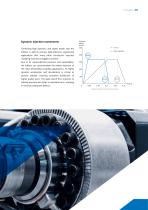
Dynamic injection movements Combining high dynamics and speed means that the IntElect is able to process tight-tolerance engineering applications that many other full-electric injection moulding machines struggle to achieve. Due to its unprecedented precision and repeatability, the IntElect can accommodate the widest selection of the most demanding moulding applications. Its highly dynamic acceleration and deceleration is critical to process stability, ensuring consistent production of higher quality parts. The rapid switch from injection to holding pressure also helps to eliminate burrs,...
Open the catalog to page 9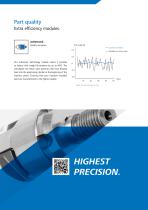
Part quality Extra efficiency modules. activeLock Quality assurance Shot weight [g] activeLock (IntElect) 0,4 Standard non-return valve Our activeLock technology module makes it possible to reduce shot weight fluctuations by up to 60%. The switchable non-return valve prevents melt from flowing back into the plasticising cylinder at the beginning of the injection phase. Ensuring that your injection moulded parts are manufactured to the highest quality. Diagram: Shot weight distribution per cycle HIGHEST PRECISION.
Open the catalog to page 10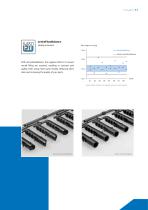
activeFlowBalance Quality assurance Part weight in shot [g] 12,14 activeFlowBalance without activeFlowBalance With activeFlowBalance, the negative effects of uneven mould filling are resolved, resulting in constant part quality when using multi-cavity moulds. Reducing reject rates and increasing the quality of your parts. Diagram: Weight distribution in the individual cavities for an injection process Example: without activeFlowBalance Example: with activeFlowBalance
Open the catalog to page 11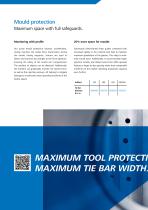
Mould protection Maximum space with full safeguards. Monitoring with profile 20% more space for moulds Our active mould protection solution, activeProtect, closely monitors the clamp force transmission during the mould closing sequence. Sensors are used to detect and transmit any changes to the force signature. Ensuring the safety of the mould isn’t compromised. The smallest of objects can be detected. Additionally, the machine can graphically monitor the ejector force, as well as the injection pressure. All helping to mitigate damage to mould tools when operating machines at the fastest...
Open the catalog to page 12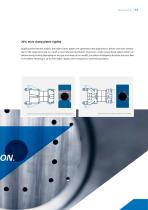
20% more clamp platen rigidity Applying finite element analysis, the IntElect series platens are optimised to the application to deliver more even distribution of the clamp force and as a result a more balanced distribution of pressure. Unlike conventional platens which can deform during locking (depending on the type and shape of the mould), our platens intelligently distribute the force flow in the platen. Resulting in up to 20% higher rigidity when compared to conventional platens. Example: Force flow and pressure distribution in a conventional tool clamping platen Example: Power flow...
Open the catalog to page 13All Sumitomo (SHI) Demag catalogs and technical brochures
-
The Future of Support
16 Pages
Archived catalogs
-
El-Exis SP
10 Pages
-
IntElect
6 Pages
-
Product brochure Systec SP
20 Pages