
Catalog excerpts
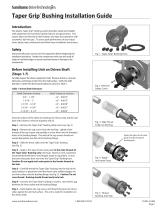
Taper Grip® Bushing Installation Guide Introduction The keyless Taper-Grip® bushing system provides simple and reliable shaft attachment for Sumitomo Speed reducers and gearmotors. This system allows bi-directional shaft rotation and stop-start operation with a powerful, slip-free grip. To assure peak performance of your equipment, please read, understand and follow these installation instructions. Safety Disconnect all power sources from the equipment before beginning this installation procedure. Handle the components with care and avoid all sharp or machined edges to prevent personal injury or damage to the components. Fig. 1 Taper-Grip® Bushing Parts Before Installing Unit on Driven Shaft (Steps 1-7) Carefully inspect the driven equipment shaft. Remove all burrs, corrosion, lubricants, and foreign matter from the shaft surface. Verify the shaft diameter is within the dimensional tolerances shown in Table 1. Table 1 Driven Shaft Tolerances Shaft Diameter (inches) 3/4” – 1-1/8” 1-3/16” – 2” 2-1/16” – 3-1/8” 3-3/16” – 4-3/4” 4-13/16” – 6-1/2” Fig. 2 Remove Safety Cover Clean all surfaces of the shaft, the bushing, the thrust collar and the unit bore with solvent to remove all grease and oil. Step 1 – Remove the Taper-Grip® bushing safety cover (see Fig. 2). Fig. 3 Slide Thrust Collar on Bushing Step 2 – Remove the cap screws from the bushing. Lightly oil the threads of the cap screws and partially re-insert them into the threaded holes in the bushing flange. The ends of the cap screws should not extend beyond the rear face of the bushing flange. Apply thin layer of anti-seize paste to male threads of bushing only. Step 3 – Slide the thrust collar onto the Taper-Grip® bushing (see Fig. 3). Step 4 – Apply a thin layer of anti-seize paste to the male threads of the Taper-Grip® Bushing only (see Fig.4). Based on tests, Sumitomo recommends Bostik Never-Seez Regular Grade or equivalent. Ensure that anti-seize paste does not enter the Taper-Grip® Bushing bore. Caution: Do not apply anti-seize paste to the female threads in the hub. Fig. 4 Apply Anti-seize Paste Step 5 – Carefully thread the Taper-Grip® bushing into the hub of the speed reducer or gearmotor until the thrust collar solidly engages the unit hub surface and the bushing flange (see Fig. 5). Caution: Do not cross-thread. Bushing should thread easily into hub. Step 6 – Unscrew the Taper-Grip® bushing to create a 1mm (0.04”) gap between the thrust collar and the bushing flange. Step 7 – Hand-tighten the cap screws until they firmly press the thrust collar against the unit hub surface. The unit is ready for installation on the driven shaft. www.sumito
Open the catalog to page 1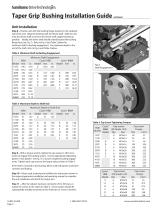
Unit Installation Step 8 - Position unit with the bushing flange located on the outboard side of the unit. Align the bushing with the driven shaft. Slide the unit onto the driven shaft as close to the driven shaft support bearing as possible. Ideally, the driven shaft should extend beyond the bushing flange face (see Fig. 7). Refer to Fig. 6 and Table 2 below for minimum shaft to bushing engagement. For maximum depth to the end of the shaft, refer to Fig. 6 and Table 3 below. Table 2 Minimum Shaft to Bushing Engagement Minimum Shaft Engagement HSM Cyclo® HBB Cyclo® BBB4 Model mm in. Model...
Open the catalog to page 2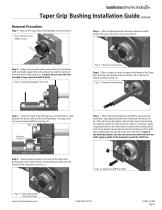
Taper Grip® Bushing Installation Guide Removal Procedure Step 1 – Remove the Taper-Grip® bushing safety cover (see Fig. 8). Fig. 8 Remove the Safety Cover Step 5 – After the liquid penetrant has been allowed to settle, remove the cap screws one at a time (see Fig 12). Fig. 12 Remove Cap Screws Step 2 – Before removing the reducer/gearmotor from the driven shaft, externally support the unit so that all its weight is removed from the driven shaft (see Fig. 9). Caution: Do not raise the unit too high. It may cause the shaft to bind. Fig. 9 Externally Support the Unit Step 3 – Check the...
Open the catalog to page 3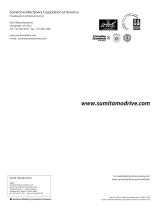
Sumitomo Machinery Corporation of America Headquarters & Manufacturing 4200 Holland Boulevard Chesapeake, VA 23323 Tel: 757-485-3355 • Fax: 757-485-7490 www.sumitomodrive.com E-mail: customercare@suminet.com www.sumitomodrive.com World Headquarters Japan Sumitomo Heavy Industries, Ltd. Power Transmission & Controls Group ThinkPark Tower, 1-1, Osaki 2-chome, Shinagawa-ku, Tokyo 141-6025 Japan Tel: +81-36-737-2511 • Fax: +81-36-866-5160 For worldwide locations, please visit www.sumitomodrive.com/worldwide ♦ Sumitomo Machinery Corporation of America Manual 19.001.61.008; Supersedes Manual...
Open the catalog to page 4All SUMITOMO (SHI) Cyclo Drive Germany GmbH catalogs and technical brochures
-
Paramax 9000 series
281 Pages
-
Helical Shaft Mount (HSM)
58 Pages
-
Bevel Buddybox 4
60 Pages
-
SERVO 6000
38 Pages
-
Motion Control DrivesE CYCLO
28 Pages
-
BEVEL BUDDYBOX 4
248 Pages
-
Cyclo® BBB5
270 Pages
-
Fine Cyclo®
123 Pages
-
PARAMAX ® 9000 Series
281 Pages
-
Fine Cyclo UA Brochure
2 Pages
-
Fine Cyclo Flyer
2 Pages
-
Precision Drives Product Catalog
20 Pages
-
Fine Cyclo F4CF – UA 25
2 Pages
-
Fine Cyclo F4CFS–UA 115
4 Pages
-
Fine Cyclo F4C–C 25
4 Pages
-
Paramax 9000
352 Pages
-
Neo Hyponic
120 Pages
-
Servo 100
58 Pages
-
Servo 6000 series
6 Pages
-
Cyclo® Drive 6000
139 Pages
-
Paramax® 9000
352 Pages
-
HSM series
58 Pages
-
Astero series
186 Pages
-
IB Series catalogues
94 Pages
-
Servo Planetary Gears EPG
6 Pages
-
Servo-Planetary Gears
4 Pages
-
Centrifuge reducers
2 Pages
-
Fine Cyclo®
114 Pages
Archived catalogs
-
Product overview
16 Pages