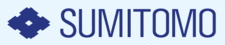
Catalog excerpts
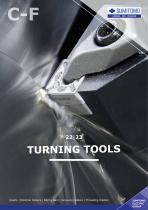
TURNING TOOLS Inserts | External Holders | Boring Bars | Grooving Holders | Threading Holders
Open the catalog to page 1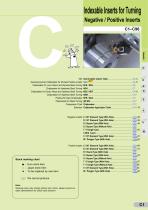
Indexable Inserts for Turning Negative / Positive Inserts. C1–C96 ISO General-purpose Chipbreaker for M-class Positive Inserts Chipbreaker for Low Carbon and General Steel Turning Chipbreaker for Hardened Steel Turning Chipbreaker for Exotic Alloys and Stainless Steel Turning Chipbreaker for Stainless Steel Turning Positive M Class Chipbreaker Chipbreaker for Steel Turning Comparison Chart Selection Stock marking chart l : Euro stock item l : Japan stock item Note: Stocking policy may change without prior notice, please consult our sales represent
Open the catalog to page 2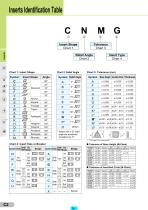
Inserts Identification Table Insert Shape Chart 1 Relief Angle Chart 2 Chart 1: Insert Shape Symbol Chart 2: Relief Angle Insert Shape Symbol Relief Angle Hole Chip Symbol Hole Style Breaker Nil No One — Face Hole Both Faces With Hole Straight hole with top end countersink (40°–60°) With Hole Straight hole with top end countersink (40°–60°) Insert Type Chart 4 Chart 3: Tolerance (mm) Symbol Nose Height Inscribed Circle Thickness ± 0,005 * Inserts with a 10° relief angle are sometimes considered as ”P” The height ”m” on sharp corner. Chart 4: Insert Hole or Breaker Tolerance of Nose Height...
Open the catalog to page 3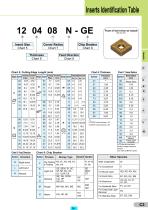
Inserts Identification Table 12 04 08 N - GE Insert Size Chart 5 Corner Radius Chart 7 Chip Breaker Chart 9 Inserts Picture of insert shown as example Feed Direction Chart 8 Chart 5: Cutting Edge Length (mm) Cutting Edge Inscribed Circle Cutting Inscribed Cutting Inscribed Shape Symbol Shape Symbol Shape Symbol Edge Circle Edge Circle Neg. Pos. Neg. Pos. Chart 7: Nose Radius CCET03X1 Insert thickness: 1,40 CCET04X1 Insert thickness: 1,80 Chart 8: Feed Direction Chart 9: Chip Breaker Round Insert (Metric) Round Insert 00 (Imperial) An ”M” after the nose radius indicates a negative tolerance...
Open the catalog to page 4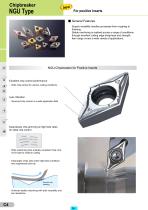
For positive Inserts General Features Superb versatility handles processes from roughing to finishing. Stable machining is realised across a range of conditioins through excellent cutting edge sharpness and strength. Item range covers a wide variety of applications. NGU-Chipbreaker for Positive Inserts Excellent chip control performance – Wide chip pocket for various cutting conditions Less Vibration – Improved chip control in a wide application field Suppresses chip jamming at high feed rates for ideal chip control Wide restraining face enables consistent chip control for light to medium...
Open the catalog to page 5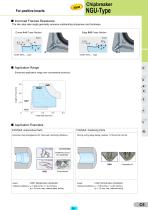
Improved Fracture Resistance The two step rake angle geometry ensures outstanding sharpness and hardness. Corner A-A Cross Section Edge B-B Cross Section Application Range Enhanced application range over conventional products. NLU Feed Rate (mm/rev) Application Examples 24CrMo5, Automotive Parts Improves chip entanglement for improved machining efficiency. Strong cutting edge design realizes 1,5 times the tool life. Chattering occurs Not applicable ap = 1,0 (2 passes) Insert: CPMT 090308 NGU (AC8025P) Cutting Conditions: vc = 200 m/min, f = 0,2 mm/rev, ap = 2,0 mm, wet, internal taper...
Open the catalog to page 6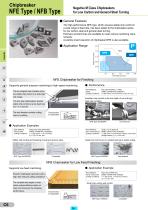
Negative M Class Chipbreakers for Low Carbon and General Steel Turning General Features The high performance NFE type, which ensures stable chip control in a wide range of feed rate, has been added to the chipbreaker series for low carbon steel and general steel turning. Extensive product lines are available to meet various machining requirements. A positive insert execution of chipbreaker NFB is also available. Application Range Feed Rate (mm/rev) NFE Chipbreaker for Finishing Supports general purpose machining to high speed machining. Work Material: Insert: Cutting Conditions: The...
Open the catalog to page 7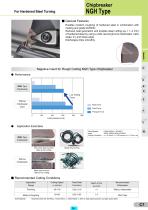
For Hardened Steel Turning General Features Enables medium roughing of hardened steel in combination with coating and grade AC503U. Reduces heat generation and enables deep cutting (ap = 1–3 mm) of hardened steel by using a wide neutral ground chipbreaker (rake angle: 4°) and sharp edge. Discharges chips smoothly. Negative Insert for Rough Cutting NGH Type Chipbreaker Performance NGH Type Chipbreaker Low Cutting Force Without Chipbreaker Insert Back Force Feed Force Principal Force 0 Application Examples Work Material: Insert: Cutting Conditions: Only minor wear occured after 40 min cutting...
Open the catalog to page 8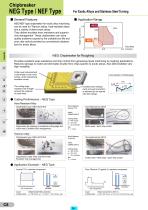
For Exotic Alloys and Stainless Steel Turning General Features Application Range NEG/NEF type chipbreaker for exotic alloy machining can be used for Titanium alloys, heat-resistant alloys and a variety of other exotic alloys. They deliver excellent wear resistance and superior chip management. These chipbreakers can solve quality problems caused by the unstable tool life and poor chip control provided by conventional chipbreakers for exotic alloys. Feed Rate 0,4 (mm/rev) NEG Chipbreaker for Roughing Provides excellent wear resistance and chip control from general-purpose machining to...
Open the catalog to page 9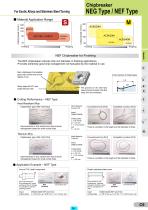
For Exotic Alloys and Stainless Steel Turning Cutting Speed (m/min) Cutting Speed (m/min) Material Application Range BN7000 NEF Chipbreaker for Finishing The NEF chipbreaker reduces chip curl diameter in finishing applications. Provides extremely good chip management not fluctuated by the material in use. Main chipbreaker that enables good chip control even at low depths of cut. Cross Section of Chipbreaker 1,2 20° Sharp edge with 20° rake angle reduces wear. The grooves on the rake face reduce heat and assist chip flow away from the workpiece. Cutting Performance – NEF Type Heat Resistant...
Open the catalog to page 10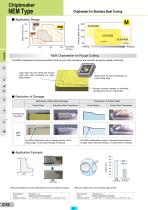
Chipbreaker for Stainless Steel Turning NEG Cutting Speed (m/min) Application Range Feed Rate (mm/rev) NEM Chipbreaker for Rough Cutting The NEM chipbreaker achieves excellent fracture and crater resistance and ensures extremely stable EGType EX Type UP Type machining. GU Type 4.0 2.0 Large radius rake face design that reduces crater wear while maintaining the cutting edge strength. Reduces boundary damage by eliminating changing points from the cutting edge. Reduction of Damage Cutting Edge Reduction of Crater Wear Boundary Wear Comparison Cross Section Crater Wear Comparison Conventional...
Open the catalog to page 11All Sumitomo Electric Hartmetall GmbH catalogs and technical brochures
-
Technical Info
55 Pages
-
CBN / PCD Tools
113 Pages
-
Drilling Tools
69 Pages
-
Milling Tools
219 Pages
-
Cutting Materials
35 Pages
-
SUMITOMO's Complete Lineup Catalog
731 Pages